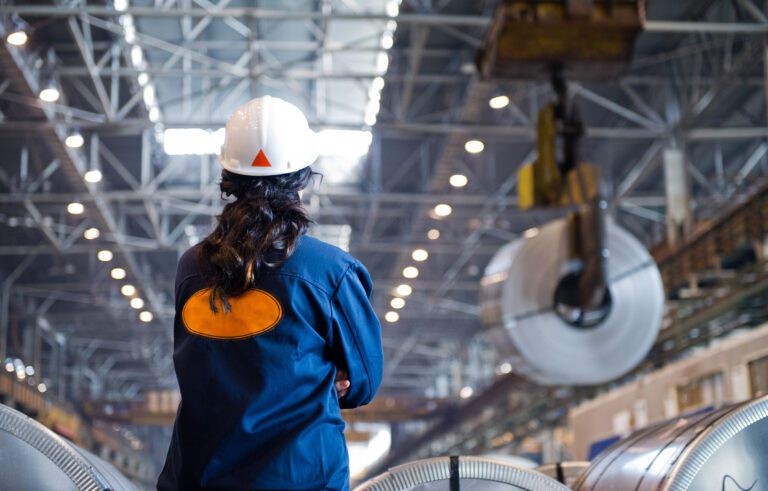
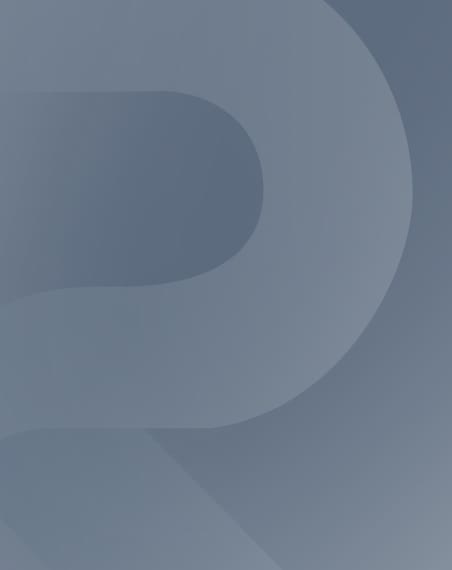
Working together to ensure the health and safety of workers in an evolving steel industry
Industrial processes can be inherently hazardous, and when accidents or work-related illnesses occur they can have serious consequences. Consequently, the first priority of any steel site should be the health and safety of workers. That is why Occupational Health and Safety is a crucial component of the ResponsibleSteel International Standard. Patrick Correa, Director for Base Metals and Mechanical Engineering for IndustriALL Global Union, discusses how we must work together to continue to ensure the health and safety of workers in an evolving industry.
The Global Day for Safety and Health at Work is an opportunity to raise awareness about the importance of workplace safety and health for employees across all industries, not least in the steel sector, where workers face a variety of hazards and risks.
Steel production is a complex and demanding process that involves exposure to high temperatures, heavy machinery, hazardous chemicals, and other physical and environmental hazards. Steelworkers face a range of potential health and safety risks, including burns, cuts, respiratory problems, hearing loss, and more.
To address these risks and promote a safe and healthy workplace for all, robust occupational health and safety (OHS) measures are essential. This can include implementing safety protocols and guidelines, providing training and education on workplace hazards, conducting regular safety inspections, and ensuring workers have access to appropriate personal protective equipment (PPE).
Unions play a key role in advocating for health and safety. By joining a union, workers can leverage collective bargaining power to negotiate for safer working conditions, better PPE, and other crucial protections.
But despite improved OHS in the sector, increasing automation, changing job requirements, evolving health and safety risks and a lack of investments from companies to ensure adequate OHS policies and resources, pose new challenges.
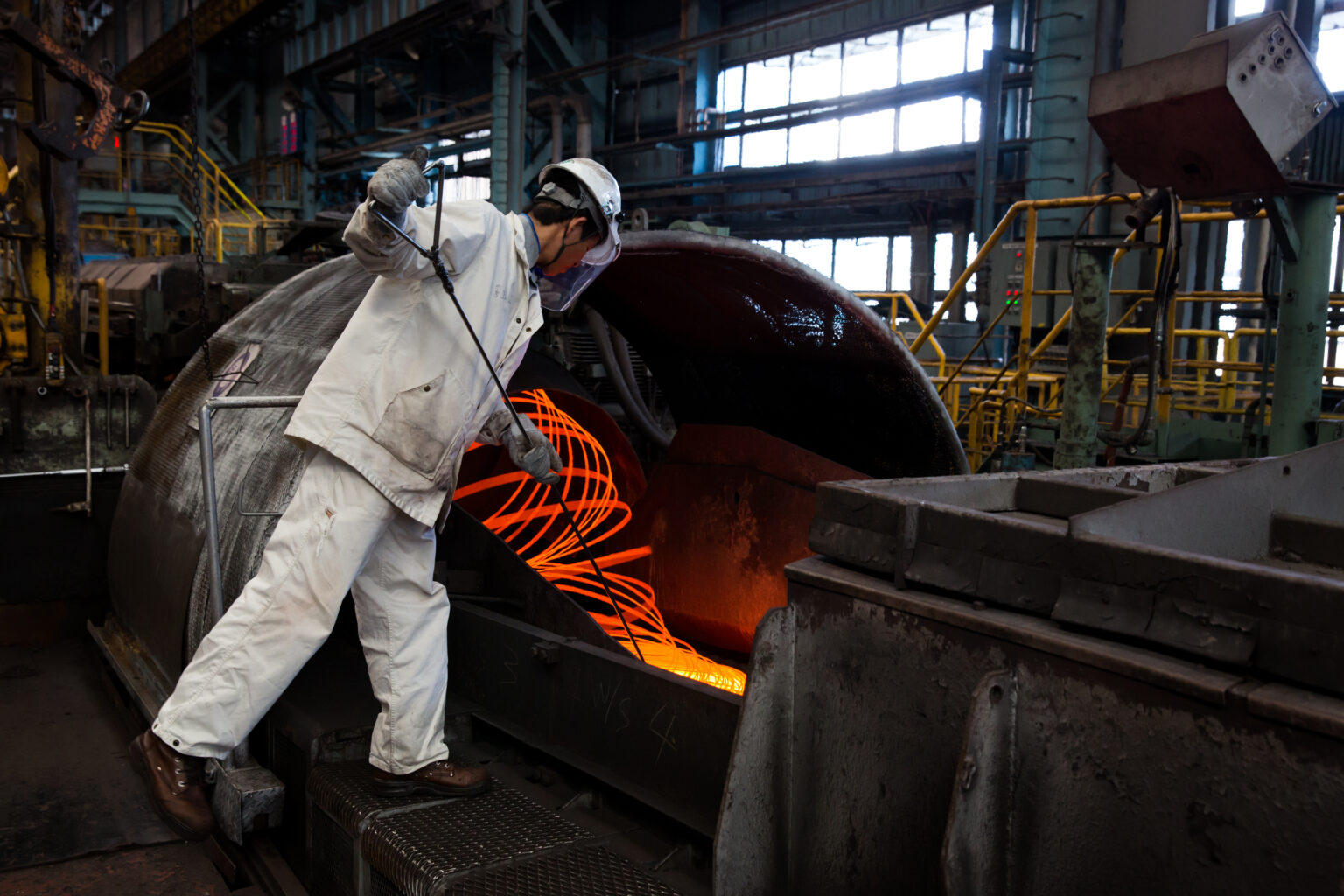
As more tasks become automated, the nature of steelworkers’ jobs will change and with that, the risks and hazards they face. Unions and employers must work together to identify and address emerging OHS concerns, like potential risks associated with robotic machinery.
As our understanding of workplace hazards and their impact on worker health and well-being continues to evolve, it is critical that OHS measures keep pace. This means that workers, unions, and employers must remain vigilant and proactive in identifying and addressing emerging risks, such as those associated with new chemicals or materials.
The Global Day for Safety and Health in the workplace is an important reminder of the critical importance of occupational health and safety in the steel sector. By promoting robust OHS measures together with the unions and addressing emerging challenges and opportunities, we can ensure a safer and healthier workplace for all steelworkers.
By Patrick Correa, Director for Base Metals and Mechanical Engineering, IndustriALL Global Union
Patrick Correa has worked in international trade unionism for 25 years, including as International Director of the CGT Métallurgie in France. He has been a member of the executive committee of IndustriALL Global Union and IndustriALL Europe and European trade union coordinator for Renault, GE Power, Engie, Nexans and Lisi. Patrick has a Master 2 degree in labour law from the University of Paris II Pantheon-Assas.
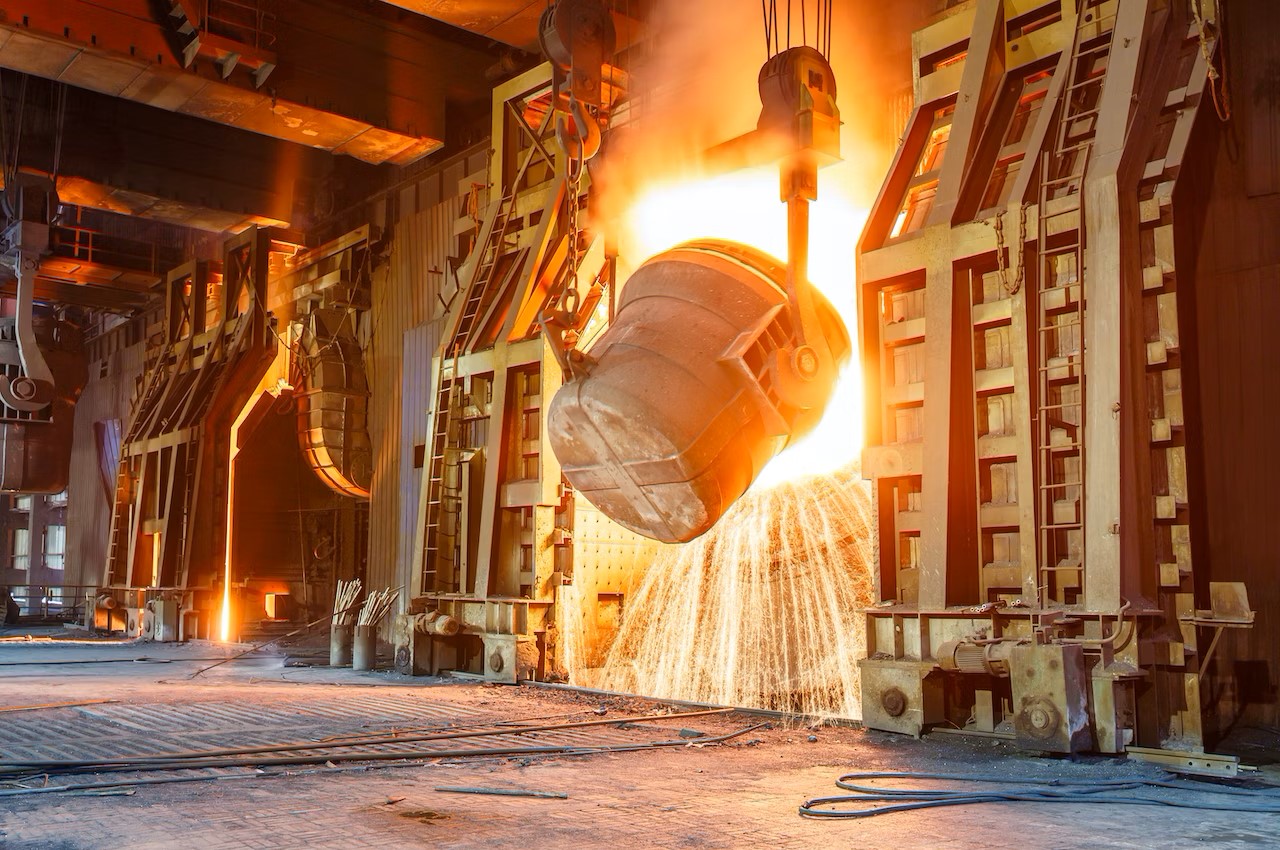
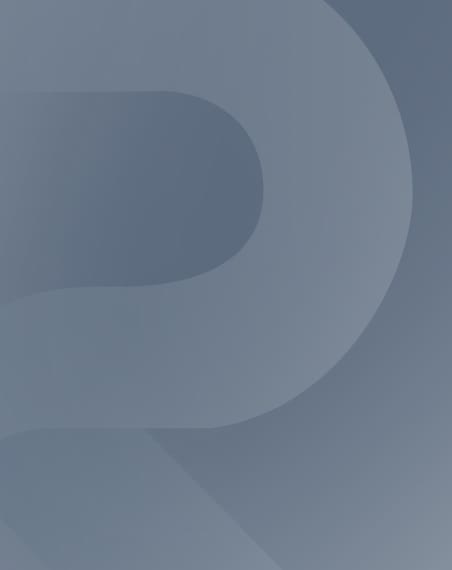
April 2023 Newsletter
Please view the April 2023 newsletter by clicking the link below:
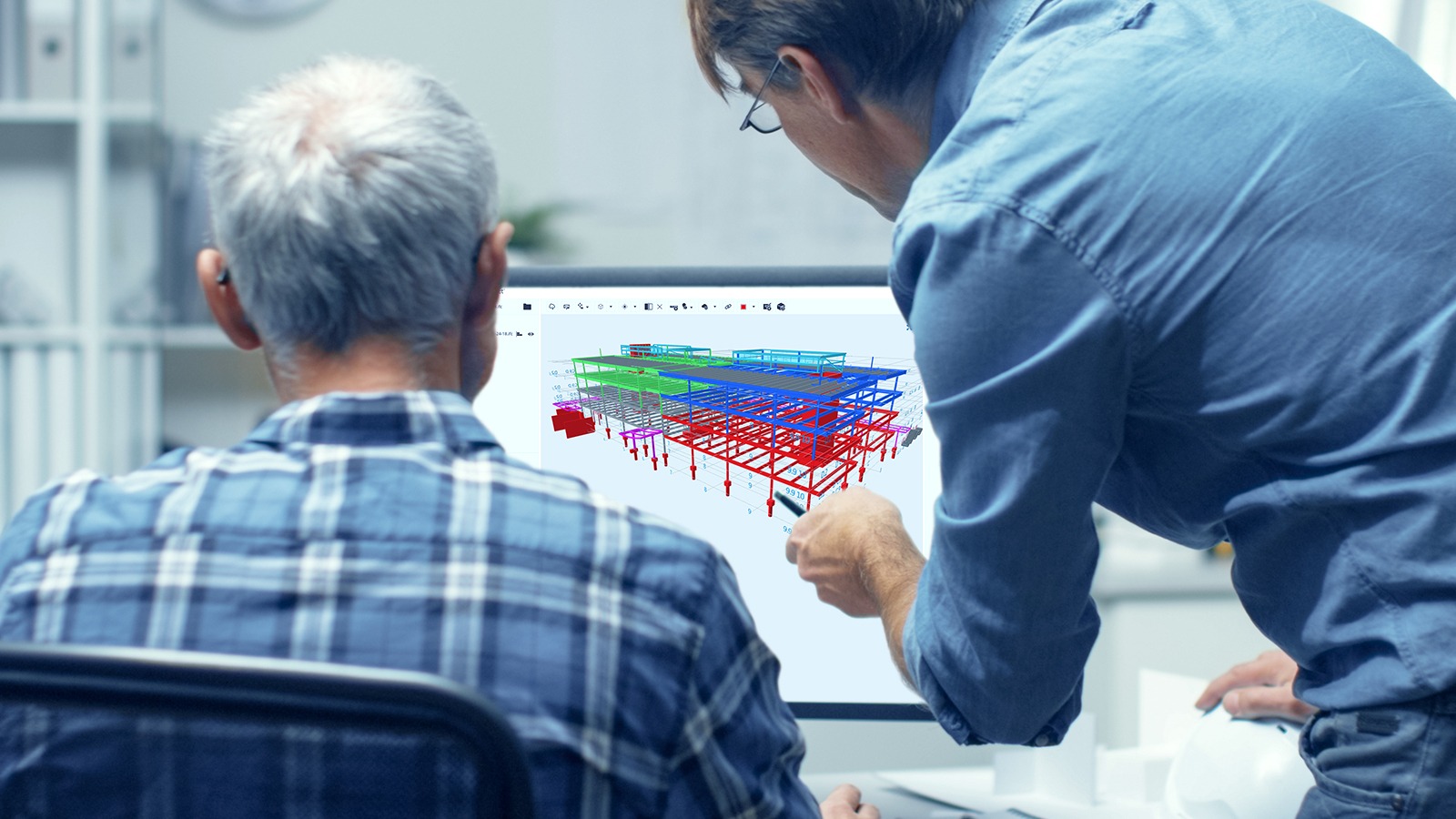
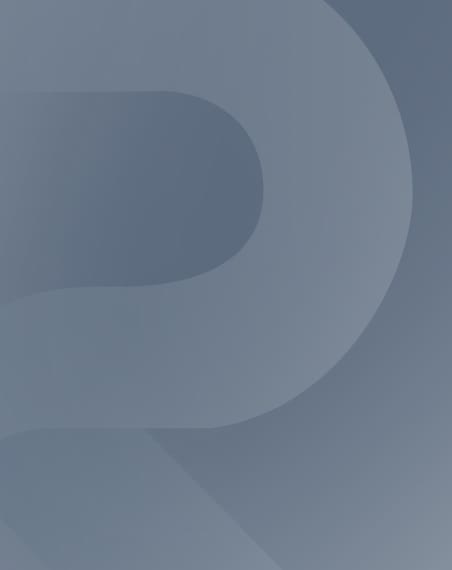
Collective Creativity will Strengthen Sustainability
The United Nations designated 21 April as World Creativity and Innovation Day, citing that the “concept of creativity is open to interpretation, from artistic expression to problem-solving in the context of economic, social and sustainable development.” Dietmar Grimm, Vice President of Corporate Strategy & Sustainability Solutions for Trimble, discusses why we urgently need to capitalise on today’s innovations to drive future change.
Now, more than ever, creativity and innovation are needed to accelerate efforts to achieve the UN’s Sustainable Development Goals (SDGs). Trimble is committed to ensuring that our mission, solutions, and initiatives align with and support the objectives of the SDGs. And joining forces with industry initiatives like ResponsibleSteel underscores that alignment.
Innovation has always been and always will be at the heart of Trimble. For almost 50 years, the company has pushed the boundaries of technology to help our customers work better, faster, safer, cheaper, and greener across the industries we serve. These are not separate goals, but actually five, highly intertwined principles. Trimble’s contribution toward helping customers operate more efficiently enables them to operate more sustainably. Examples include reducing idle time on machinery, lowering fuel consumption and emissions and reducing construction waste – all through data driven insights and decisions.
In the world of steel, our design software has enabled some of the most intriguing and intricate designs for buildings, bridges, and other structures. Technology provides endless possibilities to architects to come up with designs that really push the limits. That same technology now needs to give us the input to drive down carbon emissions across all of the construction continuum. All phases that make up an asset’s lifecycle – design, build, operate – carry emissions. That’s why our Sketchup design software portfolio includes tools that help designers make the most environmentally-friendly design decisions at the earliest possible stage, taking into consideration the effects of a building’s orientation, the local climate, the use of materials, the number and type of windows, and the application of HVAC technology. All with an eye to creating designs with the smallest environmental footprint over the long term.
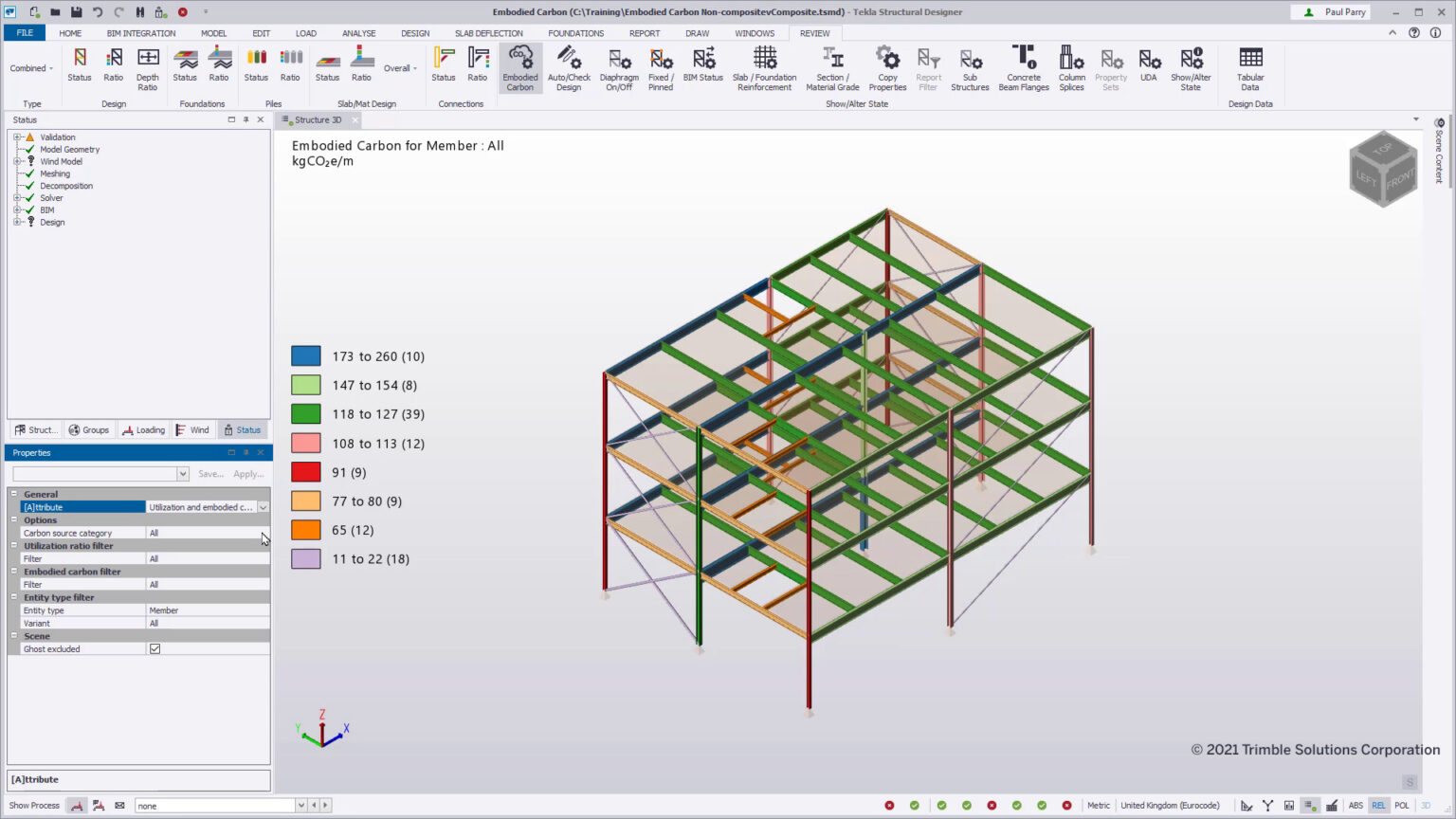
We incorporated a carbon calculator in our Tekla structural design software and worked with the One Click LCA automated life cycle emissions assessment software to offer our users enhanced visibility of the environmental impact of their structural designs. And it is also why Trimble strives to connect the traditionally separated workflows within the construction industry: to make data flow across projects to provide short- and long-term insights.
With the wider steel and construction industries being some of the largest industrial emitters of CO2, industry-wide sharing of data is crucial. With more data availability, designers can more readily come up with awe-inspiring and creative designs that still ensure our cities’ livability for decades to come. Working together with the wider industry in bodies like ResponsibleSteel has the potential to spark some interdisciplinary thinking. Many solutions to the global sustainability challenges are still years out. But we have opportunities to drive real emissions down already today if we build on the successes we already accomplished to make even more deliberately sustainable choices in all aspects of business operations. We need to challenge ourselves — on this day even more than on others — to dig deep into our collective wells of innovation and creativity and find new and lasting solutions together.
By Dietmar Grimm, VP Corporate Strategy & Sustainability Solutions, Trimble Inc.
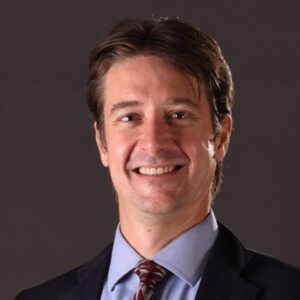
As VP Corporate Strategy and Sustainability Solutions at Trimble, Dietmar Grimm is helping the company drive profitable systems change across industries to a more productive, efficient, and sustainable, low-carbon, diverse, and equitable future for all communities.
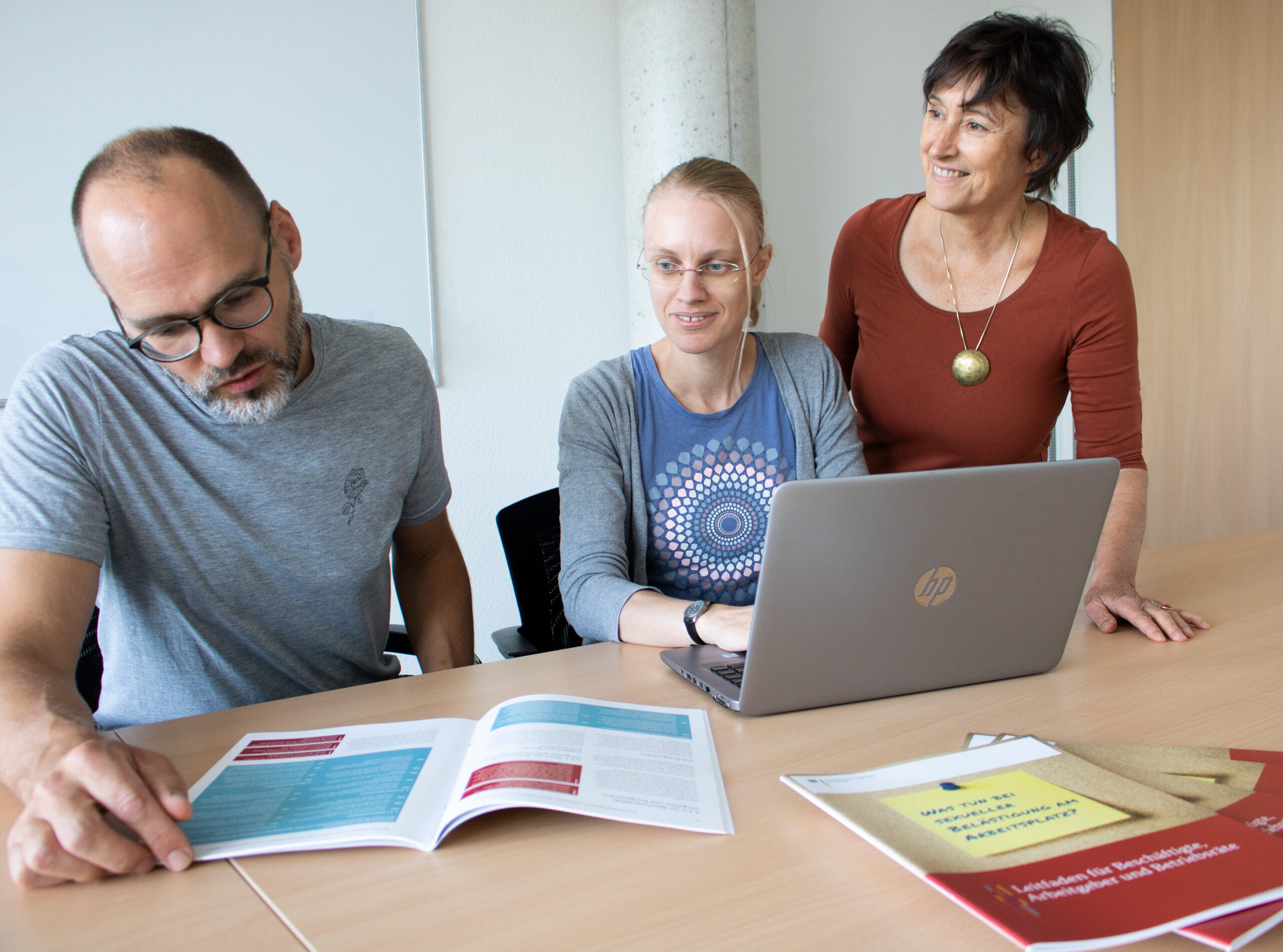
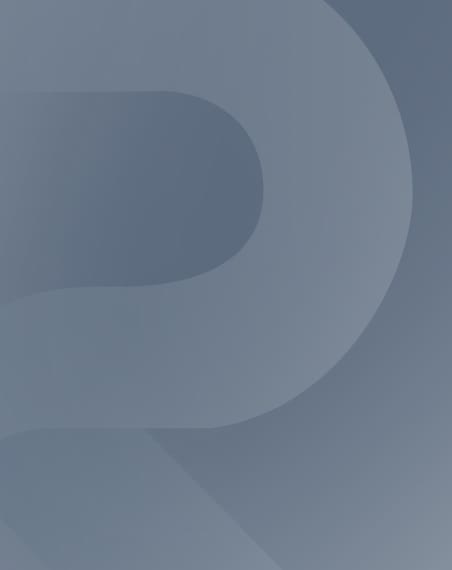
Harassment has no place in a ResponsibleSteel-certified site: Jana Loos on ArcelorMittal Bremen’s zero tolerance for harassment
ArcelorMittal Bremen in Germany was one of the first sites to become certified against the ResponsibleSteel Standard. As part of the certification process, the site had to address issues involving workplace harassment which had been raised by several female employees. Jana Loos, leader and spokesperson for ArcelorMittal Bremen’s anti-harassment project explains how the site tackled these issues and why it is so important to be vigilant and help to empower and support those who might be at risk.
A female worker received feedback from her team leader: “I like how you told the whole team that you won’t continue to tolerate their sexist comments towards you. However, my wife would never have allowed this to happen in the first place.”
Oftentimes, sexual harassment in the workplace does not constitute an overt criminal offence but is more subtly pervasive. In many cases, clumsy communication crosses the boundaries of what is appropriate in a professional environment. Or it transforms a normal social situation into an awkward one – simply because of one word too much, one touch in the wrong place or too long a gaze.
A while back, several women working at ArcelorMittal Bremen’s steel factory had the courage to disclose their experiences and seek help. A group of health experts, working council members and labour union members found the official processes wanting and united to tackle the issue. Shortly after, ArcelorMittal Bremen founded a project group to implement the social management standards required to obtain certification against the ResponsibleSteel Standard. This was the deciding factor that gave the topic the significance it needed.
The ResponsibleSteel Standard includes requirements which ensure a site identifies any risks, takes the necessary action to address such risks, and monitors the outcomes to determine where improvement is needed. Principle 6 of the recently updated ResponsibleSteel International Standard V2.0 specifically aims to make sure that “certified sites respect the rights of workers and support worker well-being.” Certified sites make the commitment to uphold labour rights and human rights, including maintaining a zero-tolerance policy for workplace harassment. Furthermore, certified sites must have effective procedures in place to understand and address any concerns raised by workers or their representatives.
Now, a few years later, ArcelorMittal Bremen has a contact person and a broad communications campaign on harassment. Trainings on the topic are implemented at all levels – comprising a seminar for new apprentices, leadership training and an awareness guide for all employees.
However, the path has not been smooth. With female staff making up only 8.6% of the workforce, some employees do not understand and even ridicule the topic. One male employee commented: “I, for my part, would like to be harassed one day!” The project team often need to stand up to such uninformed or hostile attitudes and provide basic education around these issues. The most important aim is a respectful working environment. There is no need to slander a specific person for a rude comment. Instead, the project group focuses on the empowerment of women – their approach is to equip women with the knowledge and training they need to tackle harassment situations confidently as well as raise overall awareness of the situation.
Since the beginning of the project, a noticeable change has taken place. Sexual harassment is a topic that is being talked about – even by the management board during official staff meetings with around 1,000 attendants. The goal is not “zero cases reported” – because this does not equal “zero cases” in actuality. In an atmosphere of mutual respect and encouragement, people experiencing harassment will have the courage to speak up and talk about their experiences. Therefore, the goal must be “as many cases reported as possible”.
We encourage any other organization to walk a similar path and provide their staff with all they need to tackle harassment situations. We firmly believe that this is a very important aspect of producing “responsible steel.”
By Jana Loos, Project Leader, ArcelorMittal Bremen
Please note: In the text, we only mention women being harassed by men, because this is the only constellation, we have come across so far in our organization, but we are fully aware that members of the LGTBQ+ community are exposed to similar harassment and of course, men might be harassed as well.
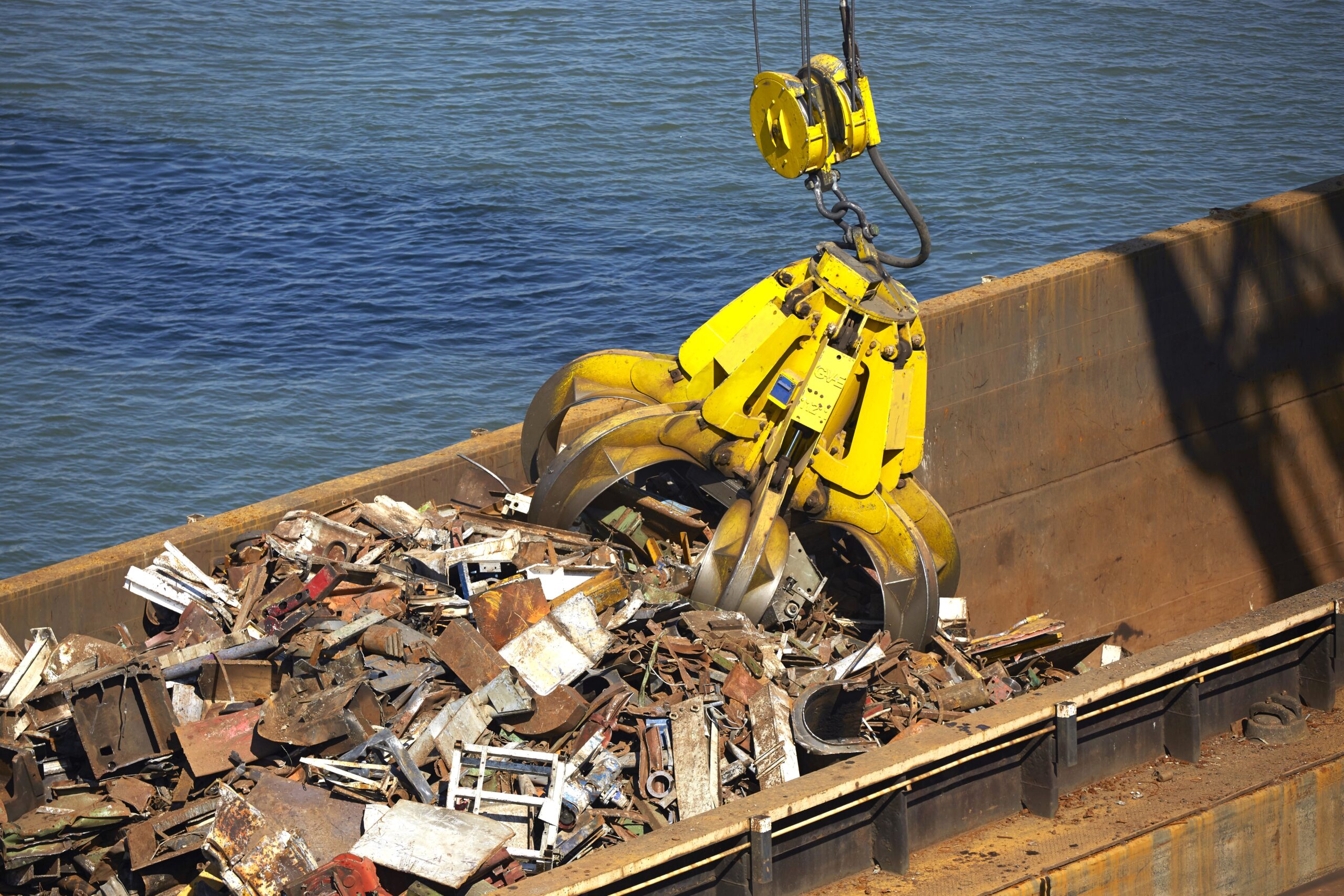
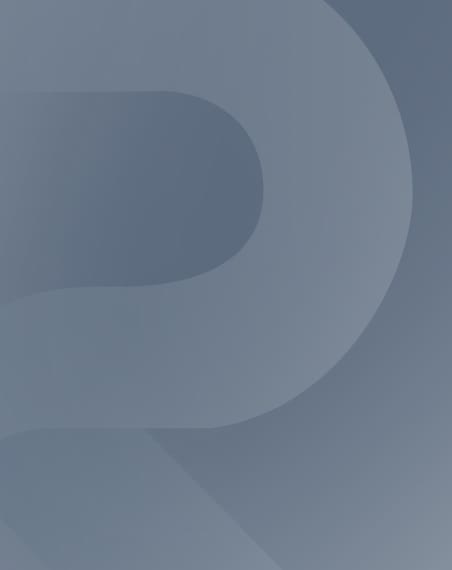
Maximising Circular Economics for Decarbonising Steel
The climate challenge for the steel industry is now well-established. Steelmaking currently accounts for between 7% and 9% of global CO2 emissions. We have not only the opportunity to do things differently across the industry, but it is vital if we are to drastically reduce the amount of emissions emitted from the steel value chain, and so have a real and lasting impact on people and the planet.
Steel is often talked about as the world’s most circular material. Maximising the recovery and use of recycled steel (i.e. scrap steel) is a critical lever and the most natural way to drive decarbonisation in the steel industry. The rates of scrap recovery today are extremely high – the highest of all materials. Worldsteel estimates that steel is recovered at a rate of 85% on average – far more from some product markets. Still, there is always opportunity for further progress. And yet, frustratingly, scrap alone is just not sufficient to meet global steel demand, and even if the use of scrap was maximised, published models tell us that it won’t provide more than half of what we need to get us to net zero by 2050 (International Energy Agency, 2020).
Clearly, as more and more buildings, cars and washing machines reach the end of their useful life, we must ensure that every last tonne of scrap is recovered, in order to produce lower-footprint steel products. But this alone will not be enough if we are serious about net zero by 2050.
It is absolutely vital that we also incentivise the decarbonisation of the only other alternative, the reduction of iron ore, however this is done, and however much scrap is available to complement it. And this is why the ResponsibleSteel International Standard adopts a ‘sliding-scale’ approach to incentivise decarbonisation across all steelmaking, regardless. In effect, our thresholds provide an equitable and effective mechanism for assessing progress on core decarbonisation across the sector and have been echoed and endorsed in numerous reports, proposals and schemes, by the International Energy Agency (IEA), Science Based Targets Initiative (SBTi), the Sustainable Steel Principles, the German Steel Federation and the Australian Green Buildings Council.
There is also a third dimension here. Let’s not forget that to maximise the progress to a net zero world, we need product design to create more value from every tonne of steel we produce and so reduce demand overall. A car made with stronger steel requires less material. Ball bearings that last longer will not need to be replaced so often. In each market, therefore, policymakers will need to reward product design that lengthens the product lifetime, reduces the amount of steel needed for a given purpose, and rewards the reuse and remanufacturing of steel products.
All these three elements – scrap recycling, demand efficiency, and decarbonisation progress – will be needed to get the steel sector to net zero within the next three decades. But how much the first two of these levers can contribute will be critical to understanding the scale of the decarbonisation progress challenge. In the coming months, ResponsibleSteel will be publishing further analysis of both scrap availability and steel demand to shed further light on what is undoubtedly the industry’s biggest challenge.
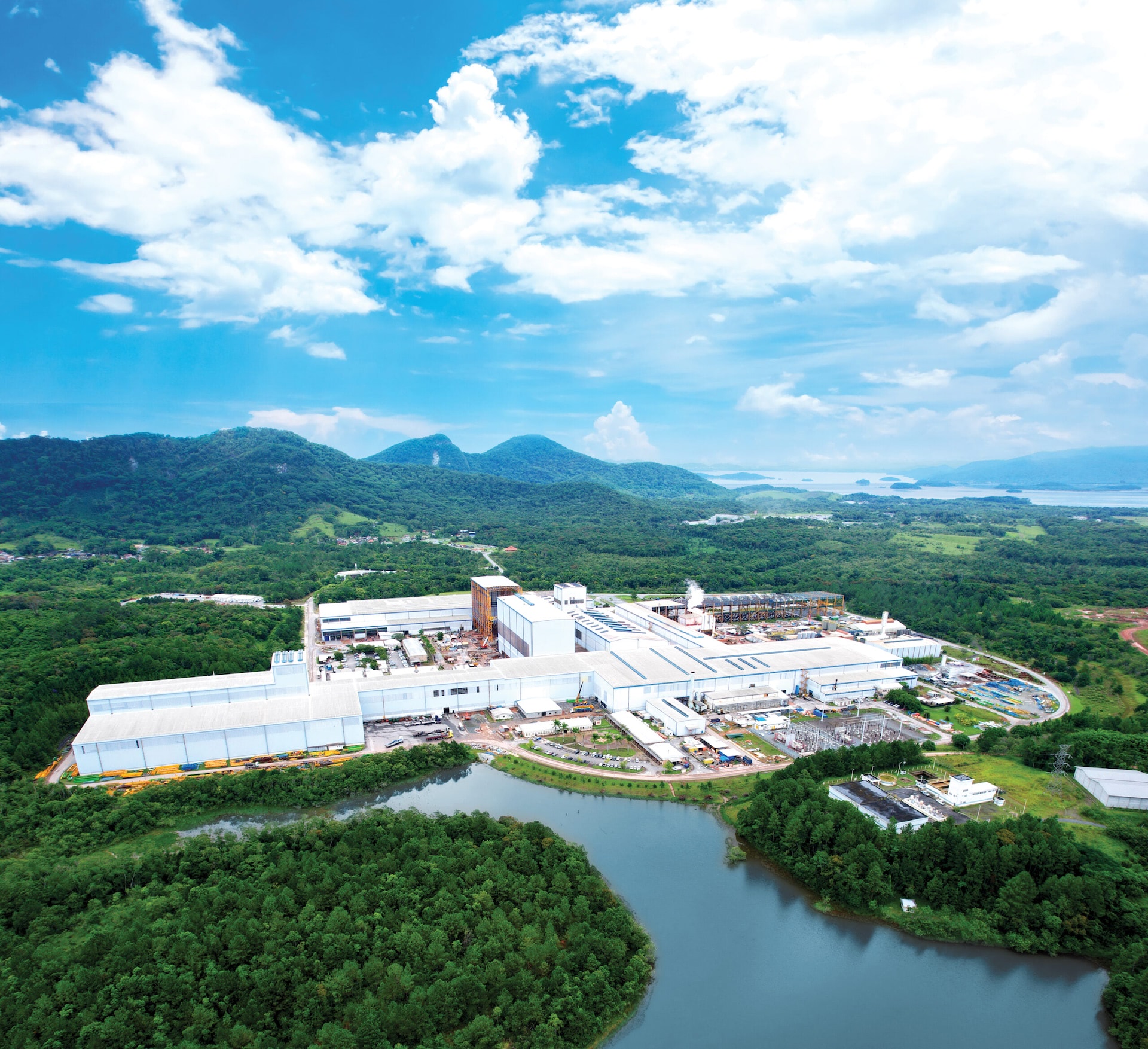
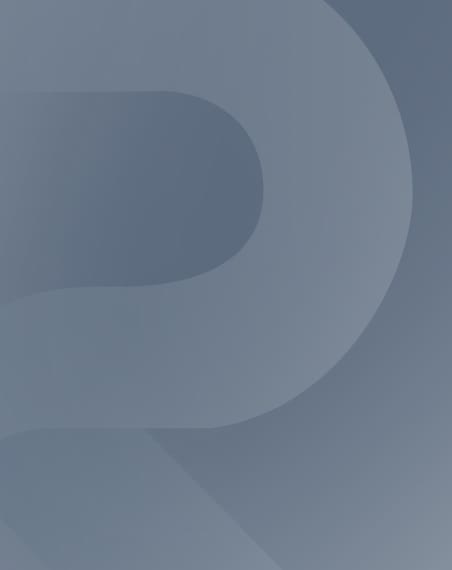
ArcelorMittal Vega Becomes ResponsibleSteel Certified
ArcelorMittal Vega in São Francisco do Sul, Santa Catarina, has recently been successfully audited and certified against the ResponsibleSteel International Standard, recognising not only the site’s efforts to implement responsible production processes, but also efforts to implement social and sustainability transformations and encourage diversity and inclusion.
The certification’s rigorous auditing process lasted around a year and took place during the largest expansion works completed in Vega’s history, requiring an investment of US$350 million. The audit was performed by the independent consulting firm DNV (Det Norske Veritas). Auditors observed the processes implemented onsite and interviewed a range of company leaders, employees, suppliers, third parties, and representatives from the government and entities and institutions from within the local community.
ArcelorMittal Vega is the group’s third Brazilian unit to receive ResponsibleSteel certification, ArcelorMittal Tubarão and ArcelorMittal Monlevade having obtained certification in 2022. ArcelorMittal aims to have all of the group’s production units in Brazil certified in the coming years.
For Jorge Oliveira, CEO of ArcelorMittal Aços Planos LATAM, this achievement demonstrates the company’s commitment to responsible and sustainable steel production and its respect for individuals. “ResponsibleSteel certification also reinforces our main purpose, which is to manufacture smart steels for people and the planet, and represents a milestone in Vega’s history, given that this year marks two decades of operations,” Oliveira affirmed.
ResponsibleSteel’s CEO, Annie Heaton commented, “This is the third certification of ArcelorMittal’s operations in Brazil and highlights the growing momentum in the sector to produce responsibly sourced net zero steel in South America. ArcelorMittal Vega has produced a clear roadmap to achieving their target of net zero emissions by 2050. And it’s critical that the responsible production of steel goes beyond decarbonization, ensuring effective management of resources and respect for workers and local communities. This certification demonstrates ArcelorMittal Vega’s commitment to meeting ResponsibleSteel’s broad set of ESG requirements. An example of this is their commitment to greater gender equality, with a goal of achieving up to 25% women in leadership positions by 2030. This is a significant adjustment in a traditionally male-dominated industry.”
The report by DNV highlighted the site’s Environmental Management System and the site’s commitment to preserving biodiversity in the region by promoting the identification and continuous monitoring of species of fauna and flora present in its Private Natural Heritage Reserve (RPPN), which occupies one third of the industrial site, in addition to the preparation of a Biodiversity Master Plan. Through means of its Water Master Plan, Vega also seeks to guarantee a reduced impact on public water sources by reusing an average of 98% of water collected onsite.
“Receiving this global certification in a year that marks 20 years of operation at the Vega unit as we move towards our largest expansion efforts to date demonstrates that we remain steadfast in our objective for sustainable steel production and commitment to community development, individual safety and respect for the environment,” Sandro Sambaqui, General Manager of ArcelorMittal Vega, stated. The expansion, which began in 2021, is expected to expand the site’s annual production capacity from 1.6 million to 2.2 million tonnes.
The audit report also recognised initiatives implemented to promote inclusion, diversity and social transformation. For example, the site has introduced incentive to increase representativeness among the female workforce in positions that were previously largely held by men. The Technical Sustainability Program, which, since 2018, has aimed to train, place value and offer qualifications to young people living in São Francisco do Sul within the region’s labor market, has contributed to achieving gender equity. Approximately 89% of the students participating in the program are employed at ArcelorMittal Vega or other companies in the region – a development opportunity that has also benefited female professionals. All of ArcelorMittal’s Brazil units have set targets to increase the number of women throughout all areas of the company, including operational, administrative and leadership positions, to 25% of the workforce by 2030.
Read the audit summary here.
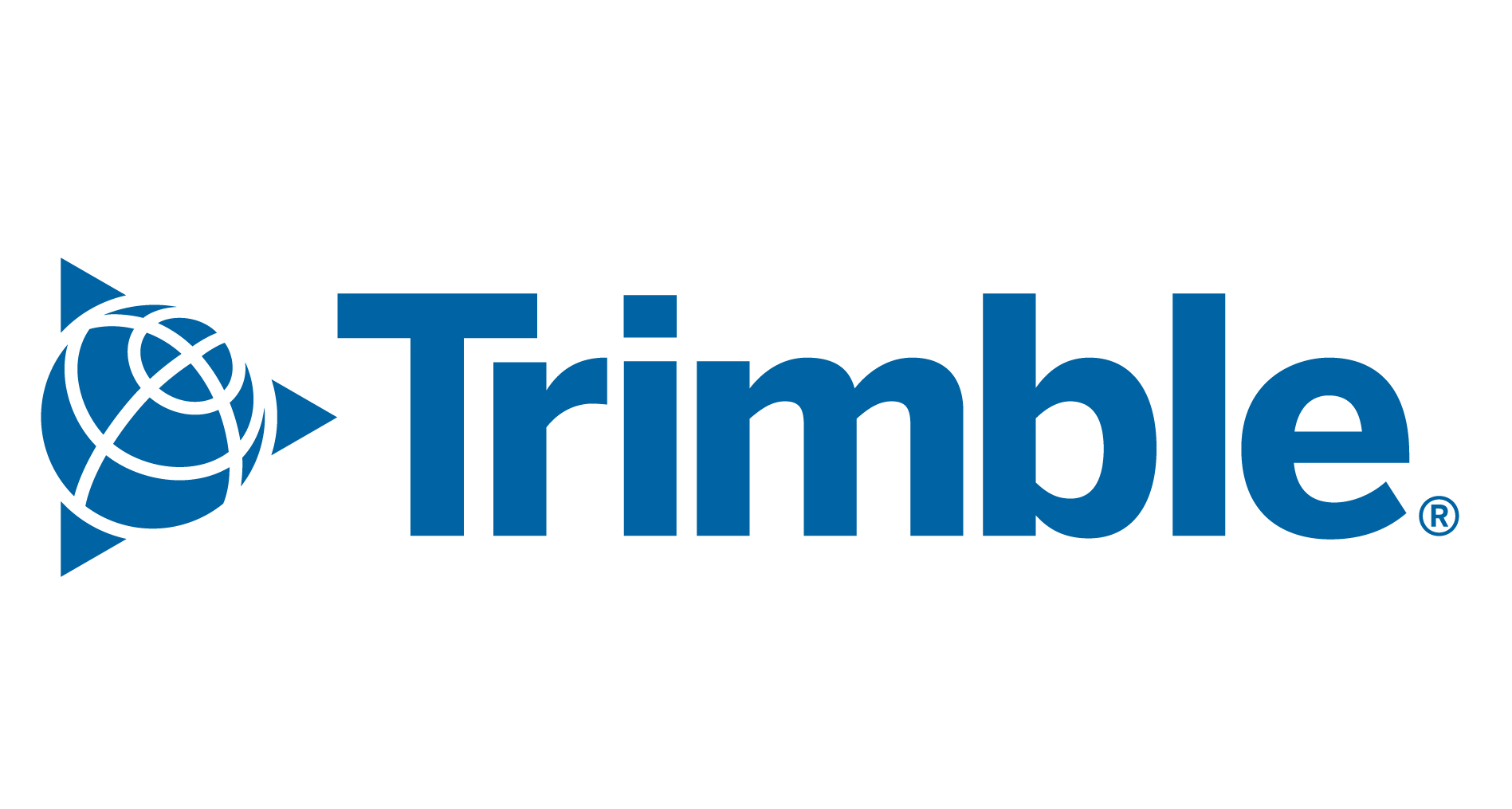
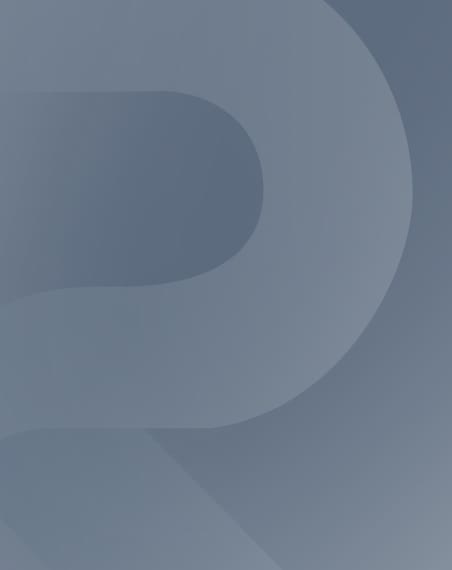
Trimble Joins ResponsibleSteel
Trimble has become the first Building Information Modeling (BIM) software technology provider to join ResponsibleSteel. Trimble’s Tekla software is one of the construction industry’s most widely used software product suites for the design, engineering, fabrication and detailing of steel structures.
With owners and operators of both building and infrastructure assets increasingly expecting their construction partners to choose sustainably sourced materials, there is a growing opportunity and urgency for the steel industry to minimize its environmental impact. With Trimble’s Tekla software solutions, engineering, detailing and construction firms and fabrication workshops can more effectively calculate and plan the use of steel in steel structures and in steel reinforcement in concrete structures.
Tekla’s Embodied Carbon Calculator enables designers and detailers to assess the potential environmental implications of designs to quickly compare various structural options’ carbon impact. Additionally, a plugin to Tekla Structures enables the upload of material quantities in a design to One Click LCA, a lifecycle assessment software that helps users calculate and reduce the environmental impacts of their designs.
“Thanks to its industry-wide nature, ResponsibleSteel has the ability to bring about impactful change to the way steel is created, sold, sourced and applied,” said Päivi Puntila, director, Business Development and Sustainability Lead for the Structures Division at Trimble. “As one of the key players in design software for steel structures, Trimble solutions have contributed to making construction more sustainable by raising efficiencies, helping avoid waste during construction, and enabling data reporting on the climate impact of projects. Our membership of ResponsibleSteel is further proof of our commitment to helping protect and build a better world to drive a sustainable future.”
Annie Heaton, ResponsibleSteel’s CEO, commented, “As the only global multi-stakeholder initiative for the responsible production of steel, we have created a platform where companies from across the steel value chain can come together to learn and work together to shape the future of the industry. Trimble, as a leading software supplier for the construction industry working to improve productivity, safety, transparency, and sustainability, will be a valuable addition to the ResponsibleSteel membership community. Buildings and construction make up around 39 percent of global carbon emissions, 11 percent of which is from construction and the manufacture of building materials such as steel. Tekla software allows engineers to measure and compare the carbon footprint of different structural designs, helping to reduce their environmental impact.”
“Companies, through industry associations, are uniting to advance sustainability to empower collective action. Associations provide opportunities to share best practices, collaborate on challenges important in their industries and set standards on GHG emission and the sourcing of input materials,” said Dietmar Grimm, vice president, Trimble Corporate Strategy and Sustainability. “By aligning with ResponsibleSteel, Trimble and Trimble technologies can play an important role in helping to drive the production and use of low-carbon steel as well as help position the construction industry as a sustainability innovator.”
In 2022, Trimble received approval for its emissions reduction targets by the Science Based Targets initiative (SBTi), a coalition of the CDP, the United Nations Global Compact, the World Resources Institute, and the World Wide Fund for Nature, joining a growing number of companies taking urgent action on climate change. Trimble has also joined forces with other companies and climate leaders in the Business Ambition for 1.5°C campaign, the We Mean Business Coalition and the Race to Zero Campaign.
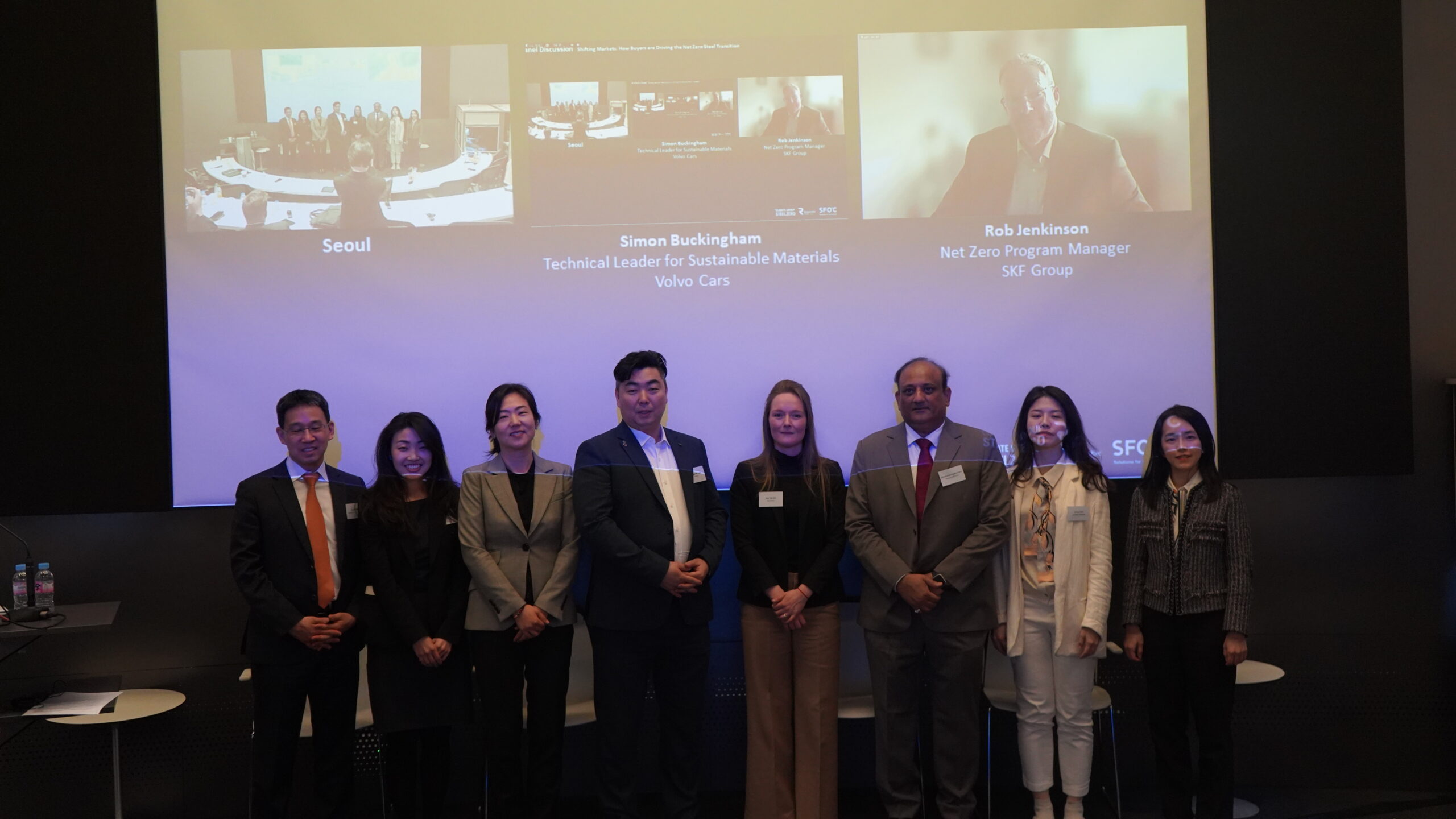
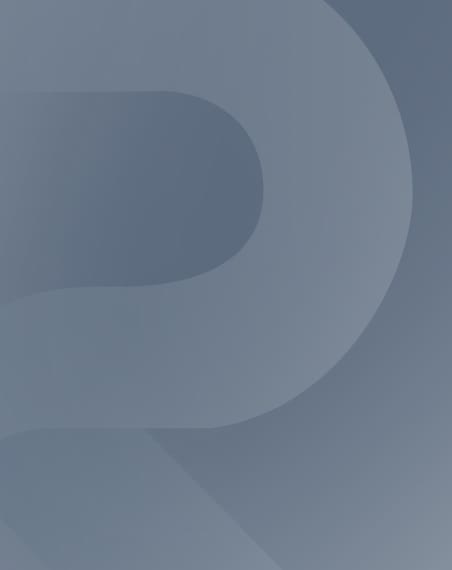
March 2023 Newsletter
Please view the March 2023 newsletter by clicking the link below:
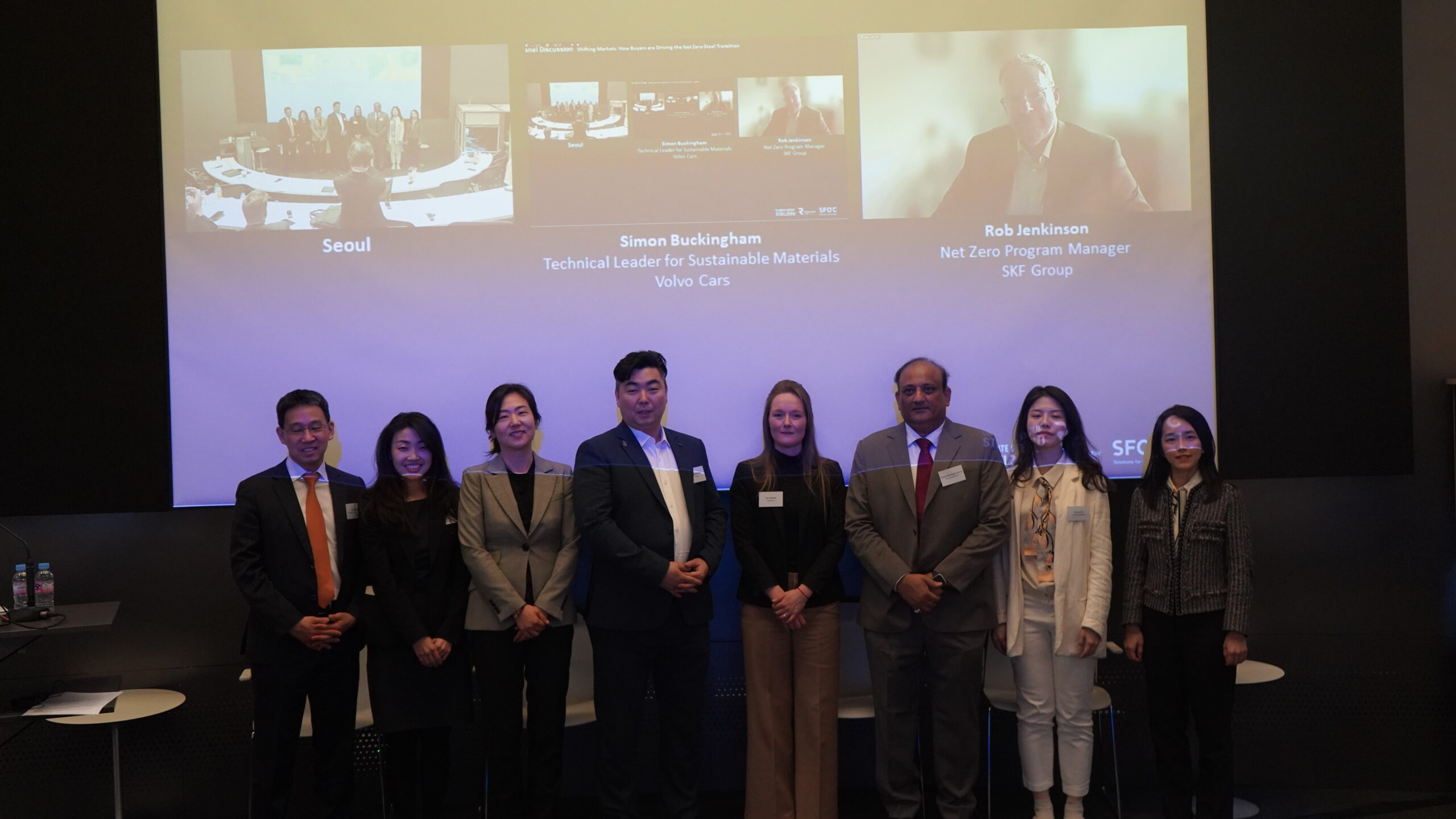
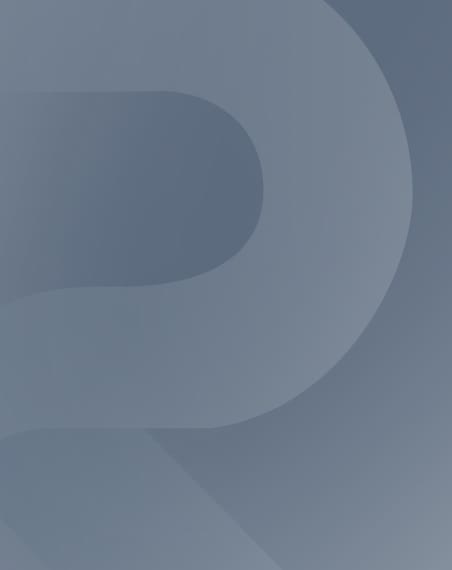
Climate Leaders to Drive Decarbonisation in South Korean Steel
On Thursday March 23rd, the Climate Group (SteelZero), ResponsibleSteel and Solutions for Our Climate (SFOC) held a special multi-stakeholder industry seminar to discuss decarbonisation of the steel industry and pragmatic solutions to tackle climate change. The event, “Decarbonising South Korean Steel – Aligning Customer Demand and Production Pathways” is the first of its kind to be held in South Korea.
Industry experts and practitioners across the steel value chain gathered to share their expertise on steel decarbonisation pathways and corporate climate leadership. The event brought together corporates with investors and civil society to discuss the most effective and pragmatic routes to rapid decarbonisation, technical breakthroughs and the role companies across the steel value chain can play to support the growing sustainable steel market in South Korea.
South Korea’s steel industry is a major domestic industrial and economic sector, and a dominant player on the world stage. In 2021, South Korea ranked as the world’s 6th largest steel-producing country, with 71.4 million tons of crude steel accounting for a 3.8% share of global production. Additionally, the South Korean steel industry is an important material supplier for major related industries such as automotive, construction and shipbuilding, with a huge inter-industrial linkage.
Attendees included some of the leading players in the steel industry – both steel producers and downstream customers such as POSCO, Hyundai Steel, SeAH Steel, SeAH Besteel, Donguk Steel, Hyundai Motor Group, Schneider Electric, WSP, A.P. Moller Maersk, Ørsted and others.
Annie Heaton, CEO at ResponsibleSteel said, “In 2022, POSCO together with ResponsibleSteel announced the certification of Pohang and Gwangyang Steelworks against the ResponsibleSteel Standard – one of the biggest steel sites in the world to achieve this accolade. This event will build on this momentum, create new partnerships and accelerate steel decarbonisation in South Korea and across the global steel value chain.”
Jen Carson, Head of Industry, Climate Group said, “All players right across the steel industry have a key role to play in accelerating decarbonisation. That’s why it’s incredibly important that steelmakers, steel consumers, policy makers, investors and civil society come together and take action on net zero steel. This conference is a pivotal moment in building a shared understanding of the current progress on lower emissions steel production in South Korea. And crucially, the opportunities for net zero steel production and procurement.”
Anna Song, Lead – Steel, Industry, SFOC said, “The steel industry around the world plays a vital role in curbing industry emissions to be on track with the 1.5 degree Paris Agreement, and Korean steel is no exception. The steel buyers on the demand side will play an especially significant role this decade because they create the business need for a rapid transition towards decarbonisation of the Korean steel industry.”
The event signalled an important exchange of ideas between key global and Korean industry players across the steel value chain. Momentum on steel decarbonisation is expected to continue building in the coming months, with the annual SteelZero Summit set to take place in Singapore on June 8, as part of the broader Climate Group Asia Action Summit. The Summit will focus on bringing together decision makers and business leaders from the steel and energy sectors to accelerate Asia’s role as an economic, green powerhouse – with a clear path to net zero. It’s part of the roadmap to Climate Group’s flagship event Climate Week NYC.
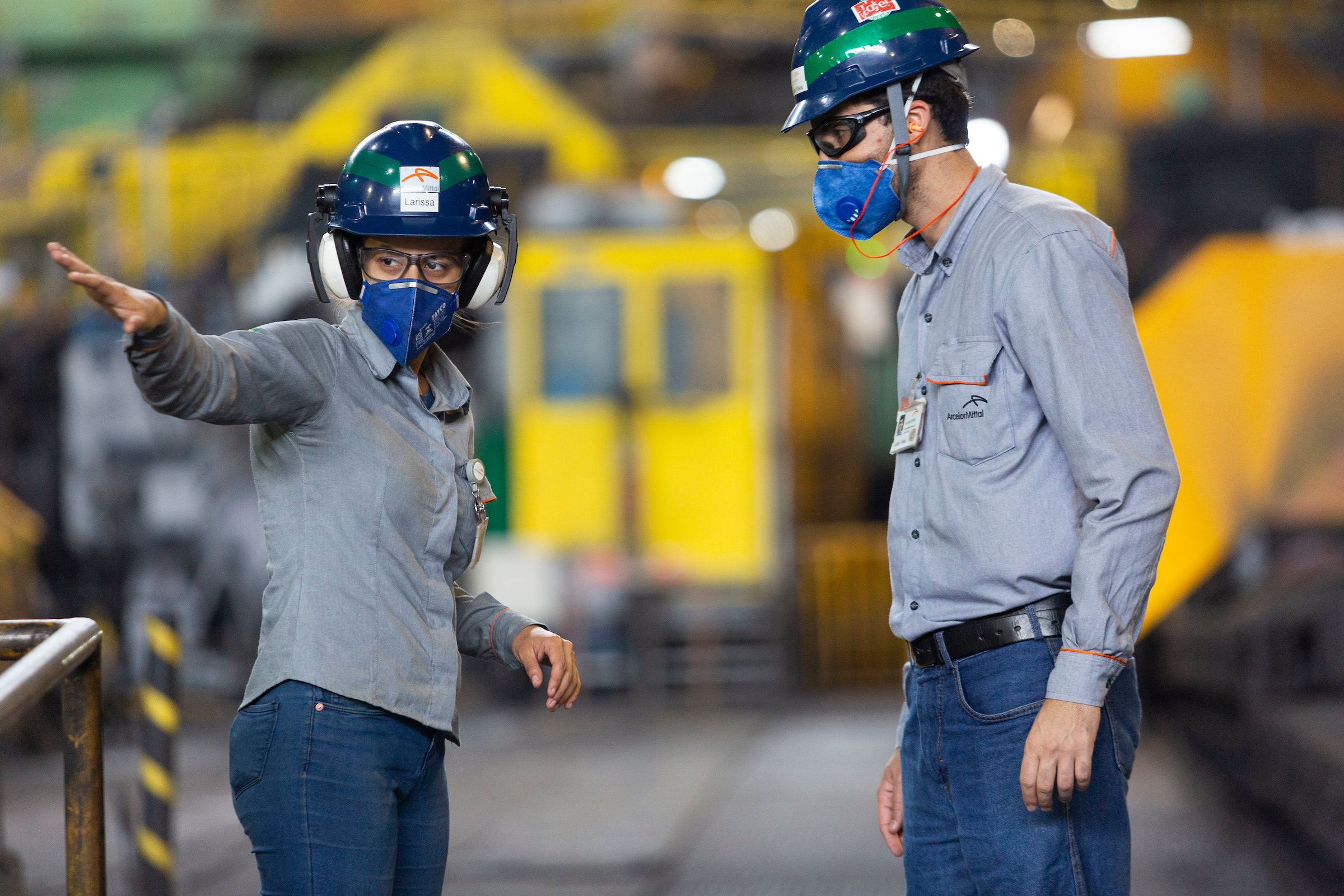
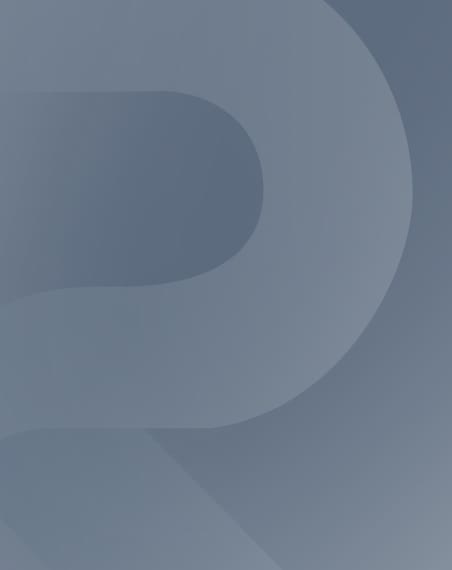
Celebrating Women in Steel: Gender equity, slow but steady steps
To celebrate International Women’s Day, Sofia Trombetta, Director of People, Health and Wellness at ArcelorMittal Long Steels LATAM and a global sponsor of diversity and inclusion for ResponsibleSteel Member ArcelorMittal, explores the slow but steady progress being made in the company as well as the wider industry to promote gender equity.
Despite advances in women’s rights and the greater occupation of spaces in the public and private spheres, society remains unequal in gender issues. In the global steel industry, the scenario is not different. We are a company of a traditional and mostly male sector. Aware of our responsibility, ArcelorMittal leads this transformation to build a more equitable community.
According to the World Economic Forum, gender inequality at work will only end in 253 years. Companies play an essential role in accelerating this process of social evolution. Research shows that more diverse teams (with more women and people with different backgrounds and profiles) bring better results to companies. In the case of its Brazilian operation, ArcelorMittal joined UN Women in 2020 and launched the goal of having 25% of women in leadership positions in its workforce by 2030.
To move in this direction, the company has adopted Woman Career Pathing, which focuses on mentoring and developing women in leadership with the goal of career acceleration. Another initiative is STEAM Girls, aimed at girls from 13 to 18 years old, with the objective of contributing to the improvement of teaching and learning in Science, Technology, Engineering and Mathematics. And the project “Elas na Siderurgia” aims to train women who were apprentices.
In addition, ArcelorMittal’s Tubarão unit – located in the municipality of Serra (ES) and the first steel plant in the Americas to obtain certification of its operations against the ResponsibleSteel Standard – is also aligned with this purpose. The plant, together with the unit of Vega (SC), held the 2nd edition of the Woman Award last year. The trophy was created to identify and recognize women, in various areas of activity, who are at the forefront of business or transformative social projects in the States of Espírito Santo and Santa Catarina, and for its third edition this year, will launch a public notice at national level. The action reinforces the company’s commitments to encourage female empowerment.
At the steel plant in Monlevade (MG) – another unit in Brazil to receive ResponsibleSteel certification – the company’s specific goal for women in leadership positions gained the attention of auditors during the certification process. The company has about 14,000 employees, approximately 14% of whom are women and 21% of those hold leadership positions. A breakthrough that already demonstrates the effect of our gender-inclusive actions.
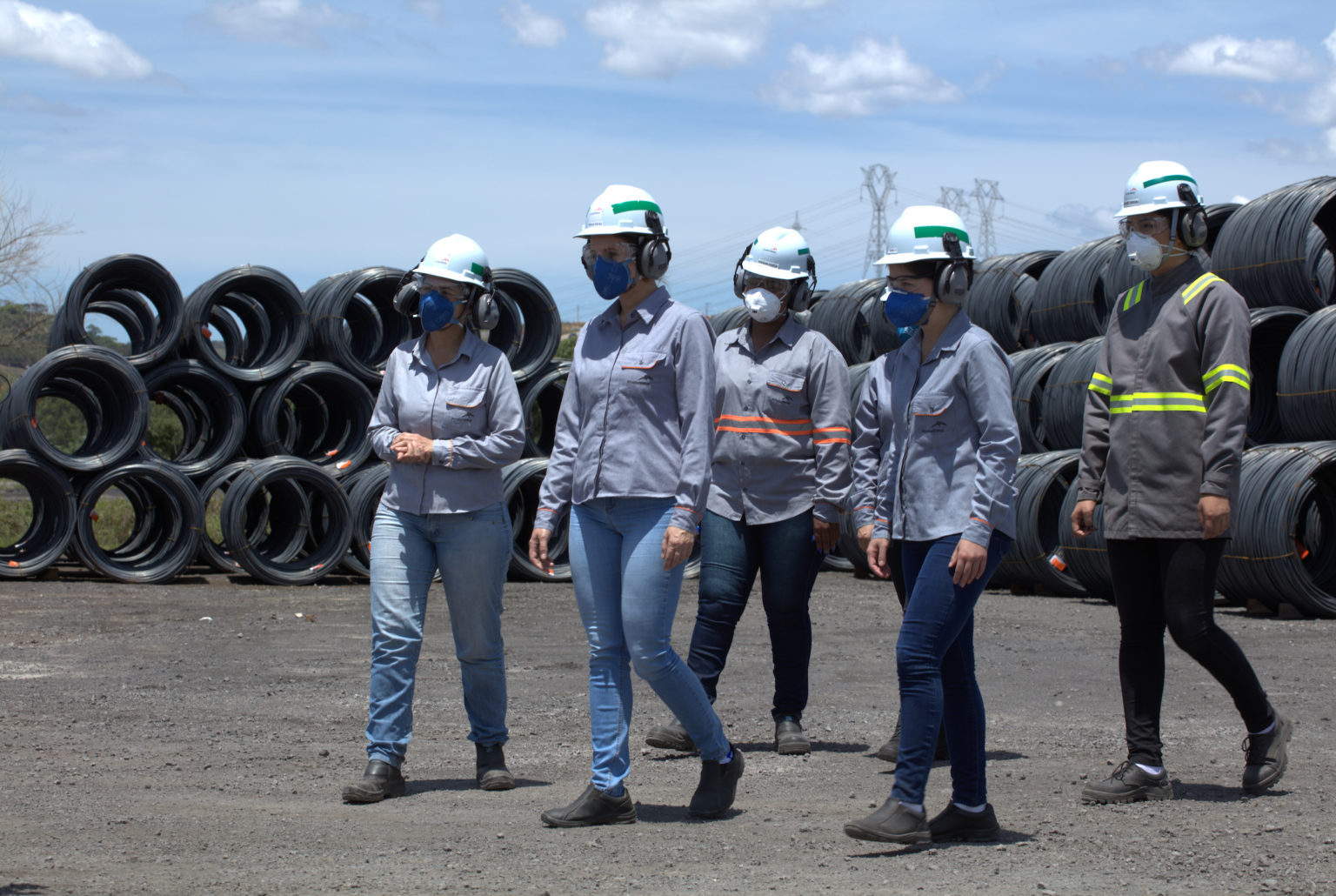
Diversity and Inclusion is a theme that has been on the agenda at a global level since the creation of the ArcelorMittal Group’s Gender Diversity Steering Committee. In 2019, with the constitution of the Diversity and Inclusion Committee in the Brazilian operation, the company began the effective design of a program that supports the definition of the strategy and the setting of metrics and KPIs. In this way, ArcelorMittal in Brazil promotes respect, acceptance and appreciation of diversity not only as concepts, but as values in daily practice.
And the initiatives that support these values are not restricted to ArcelorMittal’s internal workforce. We have revisited several programs to promote greater representation of women in the company. The I AM Qualificar program offered technical training and qualification courses in steel processes for residents of Itatiaiuçu, Itaúna, Mateus Leme and the wider region. At the time, campaigns were created to specifically attract the female population of these locations. In another program, called I AM Expert, there was an increase in applications from women for the vacancies offered. The last cycle of the Apprentice program had countless girls interested in entering the industrial sector.
The company wants to create a more welcoming, fair and plural environment for women. We understand this is a challenging journey, but we are committed to achieving this goal by 2030.
By Sofia Trombetta, Director of People, Health and Wellness at ArcelorMittal Long Steels LATAM
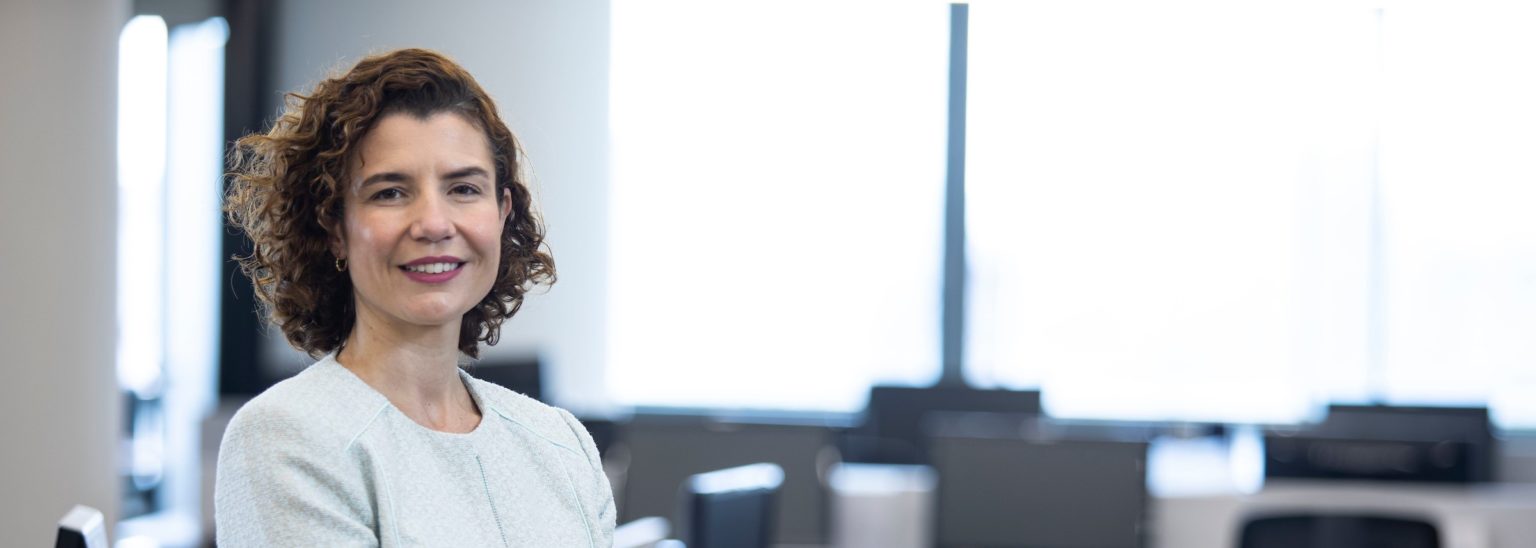
Sofia Trombetta is Director of People, Health and Wellness at ArcelorMittal Long Steels LATAM and a global sponsor of diversity and inclusion in the ArcelorMittal Group.
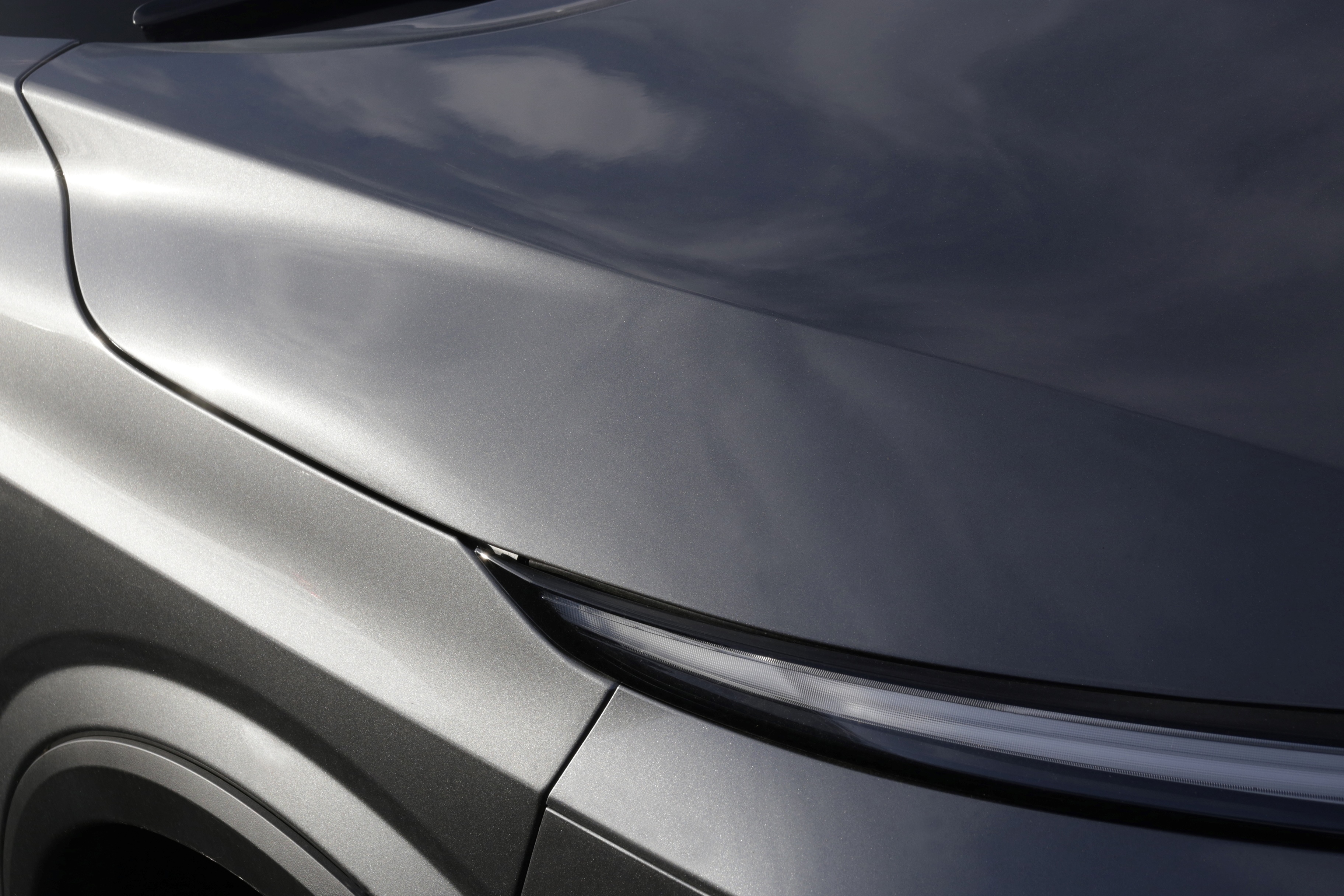
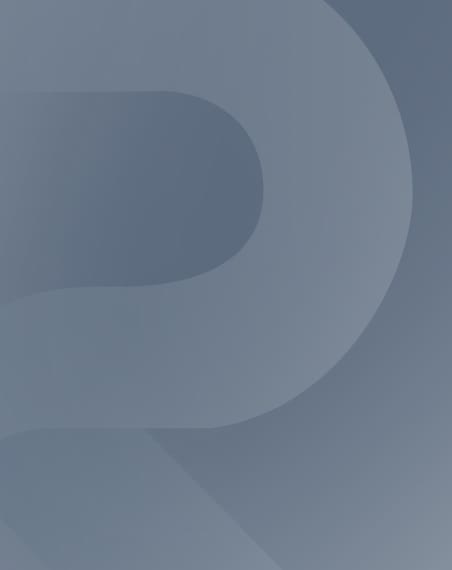
Decarbonising South Korean Steel: Aligning Customer Demand and Production Pathways
On Thursday March 23rd, the SteelZero, ResponsibleSteel and Solutions for Our Climate (SFOC) will be hosting a special multi-stakeholder industry seminar in Seoul to discuss decarbonisation of the steel industry and pragmatic solutions to tackle climate change.
The event will bring together industry experts, businesses across the steel value chain, investors, and civil society to share their expertise on steel decarbonisation pathways and discuss the most effective and pragmatic routes to rapid decarbonisation, technical breakthroughs and the role companies across the steel value chain can play to support the growing sustainable steel market in South Korea.
South Korea’s steel industry is a major domestic industrial and economic sector, and a dominant player on the world stage. In 2021, South Korea ranked as the world’s 6th largest steel-producing country, with 71.4 million tons of crude steel accounting for a 3.8% share of global production. Additionally, the South Korean steel industry is an important material supplier for major related industries such as automotive, construction and shipbuilding, with a huge inter-industrial linkage.
The event will feature an important exchange of ideas between key global and Korean industry players across the steel value chain. Momentum on steel decarbonisation is expected to continue building in the coming months, with the annual SteelZero Summit set to take place in Singapore on June 8, as part of the broader Climate Group Asia Action Summit. The Summit will focus on bringing together decision makers and business leaders from the steel and energy sectors to accelerate Asia’s role as an economic, green powerhouse – with a clear path to net zero. It’s part of the roadmap to Climate Group’s flagship event Climate Week NYC.
Contact us to find out more.
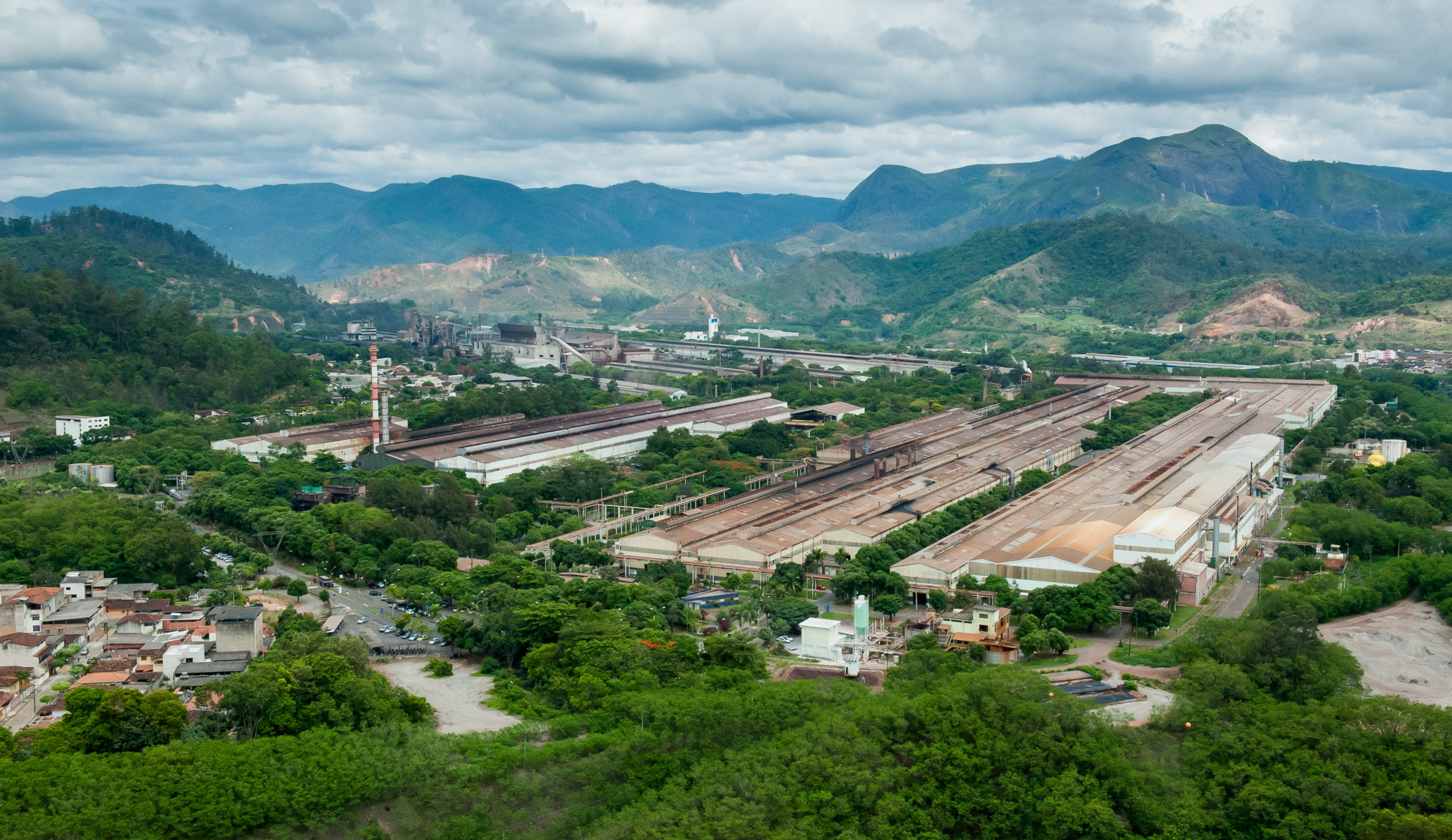
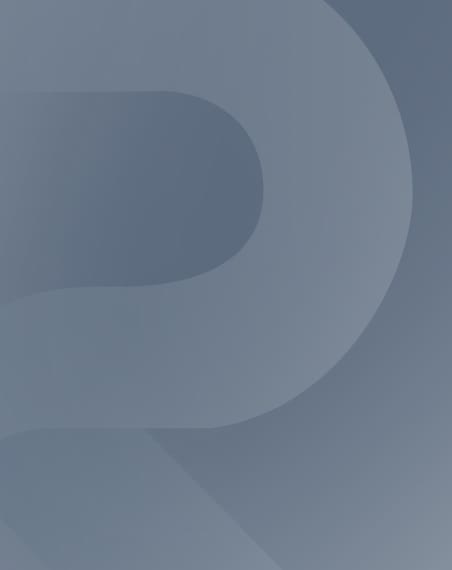
Aperam Earns Second ResponsibleSteel Certification for Aperam South America
Following a rigorous audit process by AFNOR lasting around 12 months, Aperam South America has achieved certification against the ResponsibleSteel Standard Version 1.1.
According to Aperam South America’s CEO, Frederico Ayres Lima, the site decided to pursue certification against the ResponsibleSteel Standard to further strengthen its commitment to sustainability and, strategically, to promote and make corporate responsibility more widely recognised.
Lima commented, “ResponsibleSteel is critical to our goal of striving for leadership in environmental excellence. We have one of the smallest carbon footprints in the industry and strive to adopt best practices in terms of ethics, governance, community engagement and corporate citizenship.”
He added, “This certification reinforces our commitment to sustainability, since it is part of our mission to offer the market steel solutions produced in a responsible manner.”
To obtain certification, the auditors interviewed a wide range of stakeholders and conducted several technical visits. In total, the auditors conducted over 60 interviews to map stakeholders’ perceptions of Aperam South America.
For the company’s Executive Manager of Health, Safety and the Environment, Robson Machado, this was a challenge that brought a different perspective on some issues. “It was an opportunity to reflect on our practices and see the improvements we can make,” stated Machado.
Aperam South America is an integrated producer of Flat Stainless, Electric and Special Steel. It has a total production capacity of 900,000 tonnes of steel per year and employs over 4000 workers and contractors.
ResponsibleSteel CEO Annie Heaton commented, “We’re very proud to have Aperam South America join a growing number of sites globally that have been certified against the ResponsibleSteel Standard. It is the second Aperam site to become certified, Aperam Stainless Europe being one of the earliest sites to achieve ResponsibleSteel certification back in 2021. This indicates Aperam’s continued determination to show leadership in each region they operate in. Aperam South America is working to build an inclusive and diverse working environment, one which also aims to give back to the local community. Just one example is the inclusion and diversity plan led by volunteers which the site has put in place to combat discrimination and stereotyping.”
Heaton continued, “The site also set up the OIKOS biological reserve through Aperam’s Acesita Foundation, and this has become not only a thriving hotspot for biodiversity but an important environmental education centre for the area, helping to preserve the nearby habitat for future generations and reflecting the site’s commitment to both people and the planet.”
Read the full audit summary here and watch Aperam South America’s CEO make the announcement here.