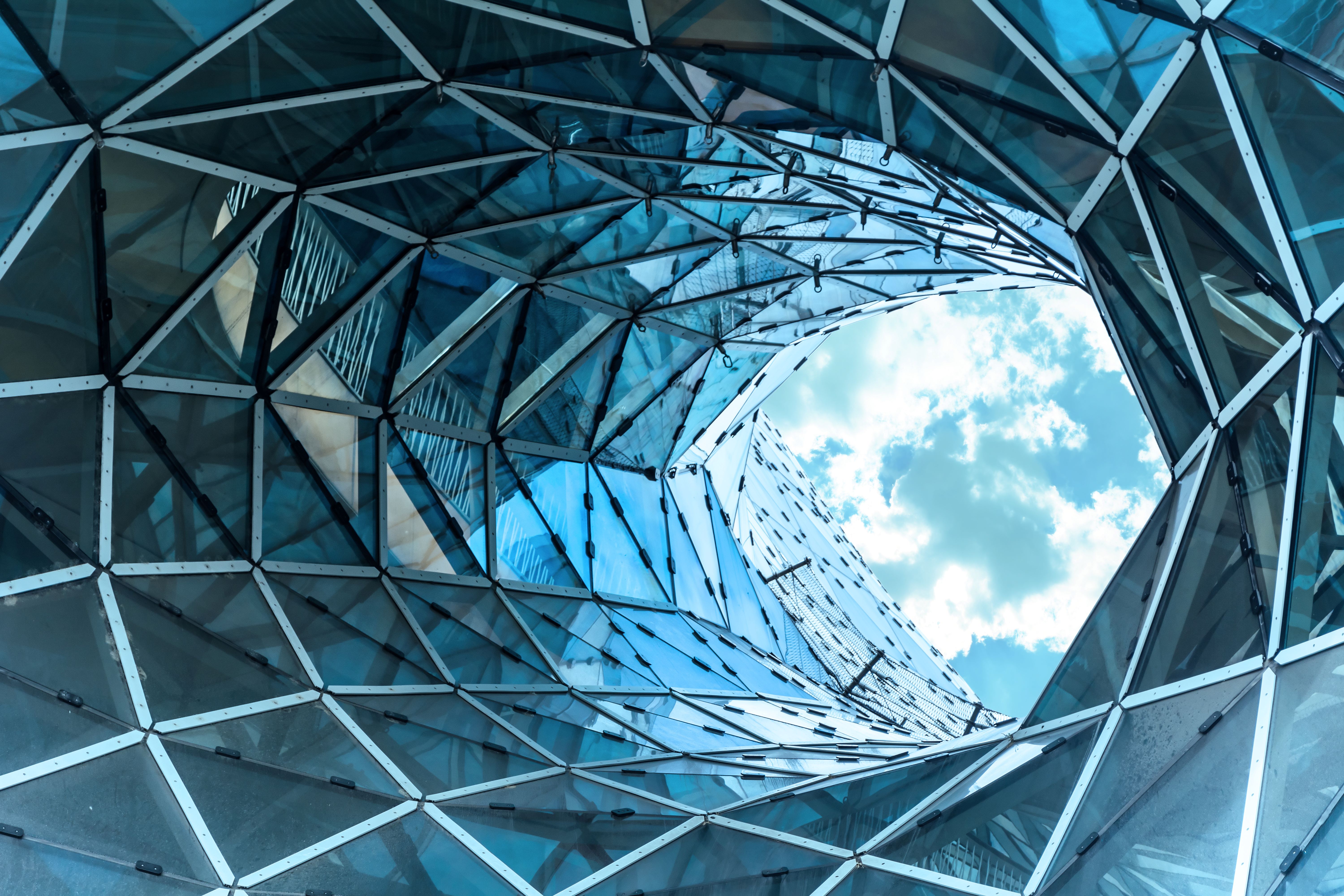
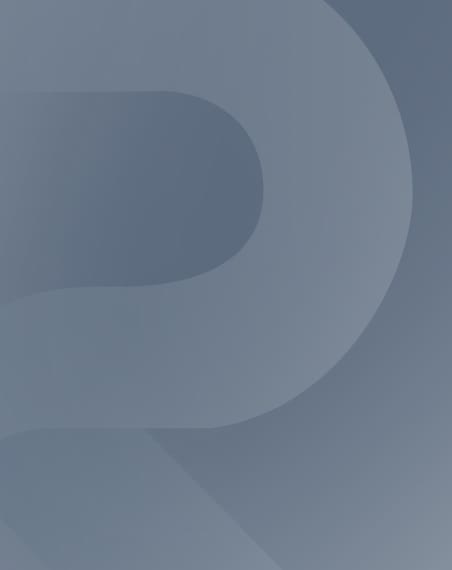
ResponsibleSteel and LESS aisbl urge robust, scrap-conscious approach to effective European steel decarbonisation
ResponsibleSteel and the Low Emission Steel Standard (LESS aisbl) today jointly release a new policy briefing, ‘The Steel Decarbonisation Scale’, urging European policymakers to adopt a more robust and realistic approach to steel decarbonisation—one that recognises the physical limits of scrap supply and incentivises genuine emissions reductions across all steel production routes.
The study highlights that Europe’s steel industry, as the world’s second-largest producer, is responsible for 6% of the European Union’s total emissions. With ambitious EU targets aiming for a 55% reduction in net greenhouse gas emissions by 2030 and net zero by 2050, the way steel decarbonisation is measured and incentivised is of critical importance.
A key finding of the study is that current policy discussions, including the European Steel and Metals Action Plan (ESMAP) and proposals for voluntary carbon labels for steel, risk undermining climate goals if they fail to account for the fundamental constraints on scrap availability. Despite a high global steel recycling rate of 85%, only about 32% of the world’s demand for new steel can currently be met with recycled scrap due to the long lifetime of steel products, according to the International Energy Agency (IEA). While the amount of available scrap is set to increase, the IEA estimates that scrap will still only be sufficient to meet 46% of steel demand by 2050.
“Steel decarbonisation requires an appropriate base for comparing steel products in terms of their global climate impact,” said Dr. Martin Theuringer, Secretary General of LESS aisbl. “Scrap is a valuable and limited resource. Any label or standard that ignores this risks distorting markets and ultimately slowing down the transition to truly low-emission steel. Our approach ensures that both primary and scrap-based production are incentivised to decarbonise, not just to compete for a fixed pool of scrap.”
ResponsibleSteel and LESS propose the adoption of a “steel decarbonisation scale” that complements traditional carbon footprinting by explicitly accounting for the ratio of scrap and primary iron used in steelmaking. This approach, already recognised by the G7 and incorporated into international standards, would:
- Prevent fruitless competition for a limited scrap supply
- Incentivise decarbonisation across all steel production routes
- Promote technology-neutral, WTO-compliant solutions
- Support the competitiveness of European industry while advancing global climate goals
“A European label for steel is a great opportunity to incentivise steelmakers to become globally competitive on their real decarbonisation progress,” said Annie Heaton, CEO of ResponsibleSteel. “A well-designed classification system will do this by taking into account scrap content in addition to the measurement of steel‘s carbon intensity, recognising that scrap will at best provide half of the world’s steel by 2050. As a result, this ‘steel decarbonisation scale’ approach incentivises investments that drive progress in the steelmaking process itself, whether in primary or secondary iron and steel making.”
The two organisations call on the European Commission to integrate the steel decarbonisation scale into the development of voluntary labels, lead markets, and investment support mechanisms, ensuring that future measures are effective, fair, and aligned with Europe’s climate ambitions.
Download the briefing here.
Access ResponsibleSteel’s approach to GHG emissions metrics here.
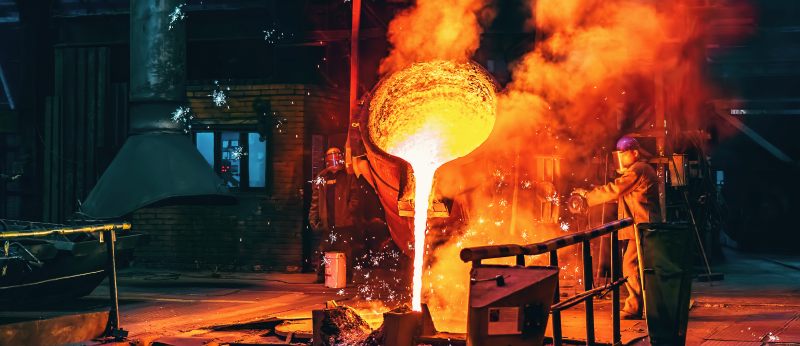
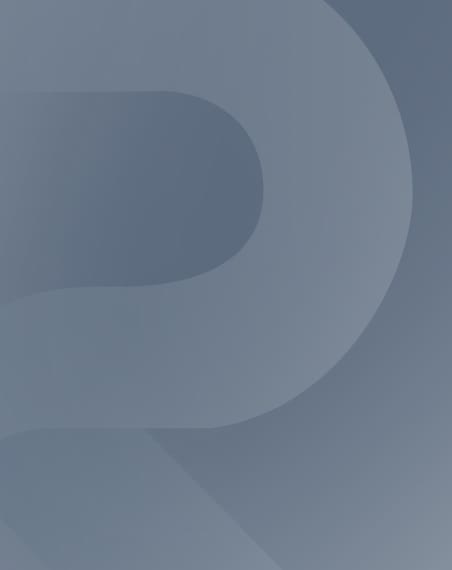
May 2025 Newsletter
This month, we’re building on the momentum from our recent AGM and Members Meeting, where we reflected on the progress of the past year and explored the key priorities for 2025.
We’ve launched a new events page for upcoming initiatives. Alongside this, we are announcing new training sessions and working groups, with workshops scheduled in the coming months.
We are also calling on members to submit guest blogs for the ResponsibleSteel website to share insights, innovations, and experiences of responsible steelmaking.
Read our latest newsletter for updates, opportunities to engage, and news from across our network.
Click here to read the full newsletter.
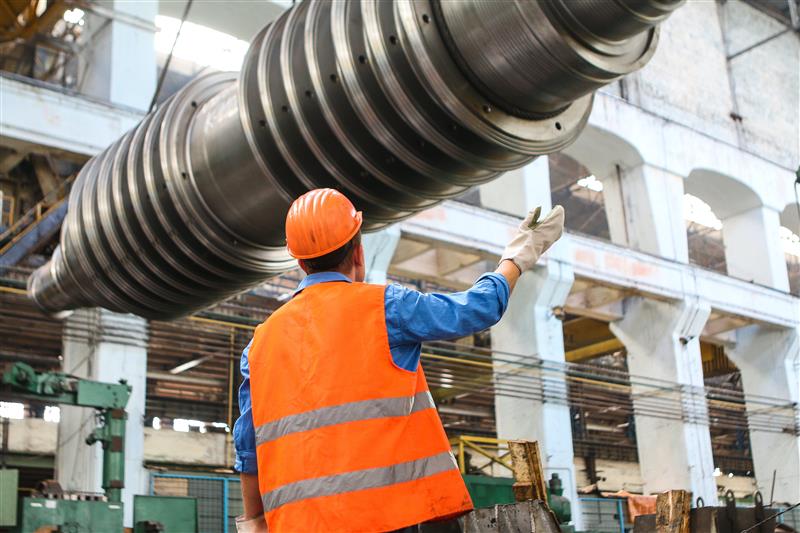
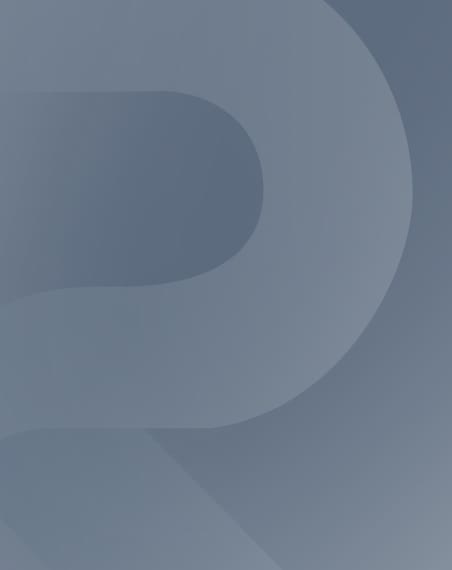
April 2025 Newsletter
This month, we’re proud to share the second ResponsibleSteel Progress Report - a chance to reflect on the major milestones achieved in 2024, highlight key learnings, and look ahead to the work still to come.
Our upcoming AGM and Members Meeting will also explore important developments across our programmes. If you haven’t registered yet, now’s the time.
To mark Earth Day, we’ve published a new article examining our relationship with the planet and the role ResponsibleSteel plays in supporting its protection.
We highlight an important upcoming development relating to our decarbonisation requirements and guidance. You’ll also find the latest updates on audits, events, and training opportunities.
In this newsletter, you will find updates on:
- Our 2025 Progress Report
- New members
- Upcoming trainings
- Updates from the team
- And more...
Click here to read the full newsletter.
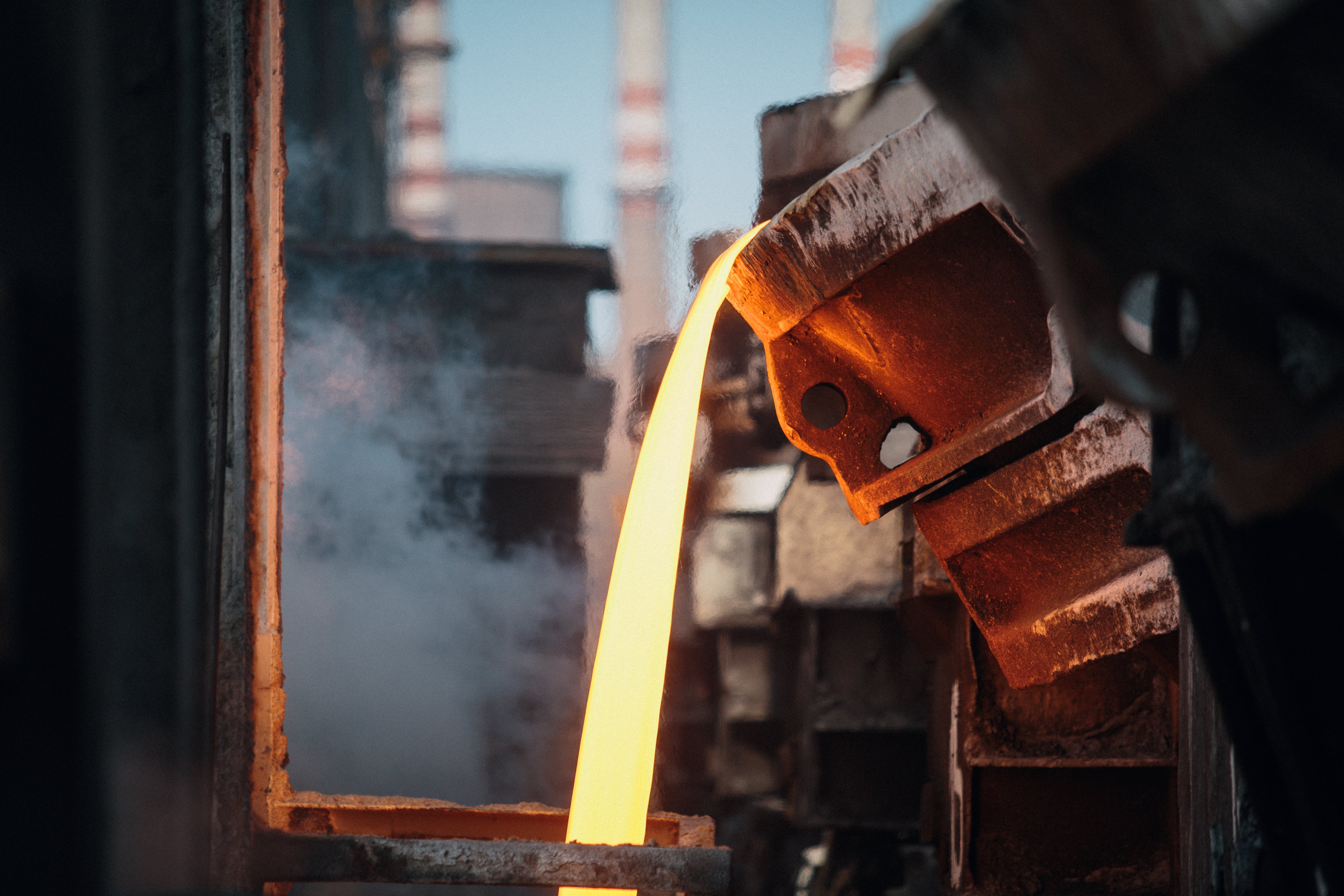
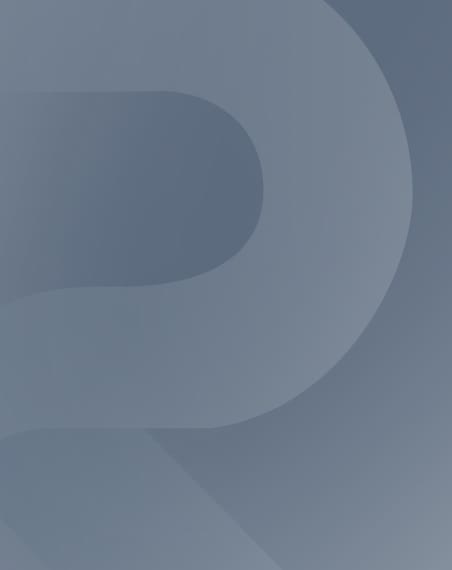
ResponsibleSteel publishes second annual Progress Report
ResponsibleSteel is fast becoming the reference tool to drive the demand, policy, and finance levers necessary for the steel industry’s transition, providing a sustainability roadmap that customers, communities, investors, and workers can all get behind.
ResponsibleSteel’s annual Progress Report provides an opportunity to measure and report on the progress of our programmes, celebrating our milestones and identifying areas for learning and improvement.
In this second ResponsibleSteel Progress Report, we track the development of new work undertaken in 2024, the growth of ResponsibleSteel's membership, and the progress of our certification programme as we look toward 2030 and beyond.
2024 was a challenging year for the industry, but despite setbacks, we continued to see real determination and progress.
In 2024, we saw a 34% increase in the number of Certified Sites, bringing the total up to 87. And we saw the first sites complete re-certifications, a true testament to the enduring value of ResponsibleSteel certification. Critically, the first Certified Steel was also launched on the market – 2.4 million tonnes produced by U. S. Steel’s Big River Steel site – marking a new era of progress.
This Progress Report examines the growth of ResponsibleSteel’s certification programme and membership in 2024, as well as featuring other highlights from the year, including:
- The launch of the International Production Standard Version 2.1
- The launch of a draft Chain of Custody Standard
- The publication of our report, Charting Progress to 1.5°C through certification
- Insights into the value of ResponsibleSteel membership and certification from our 2024 Membership Survey
Looking to the future, we continue to build on work begun in 2024 to build a market for responsibly produced, near-zero steel by engaging with and mobilising policymakers, investors, and buyers of steel.
Read the full report to find out more about our progress in 2024 and plans for 2025.
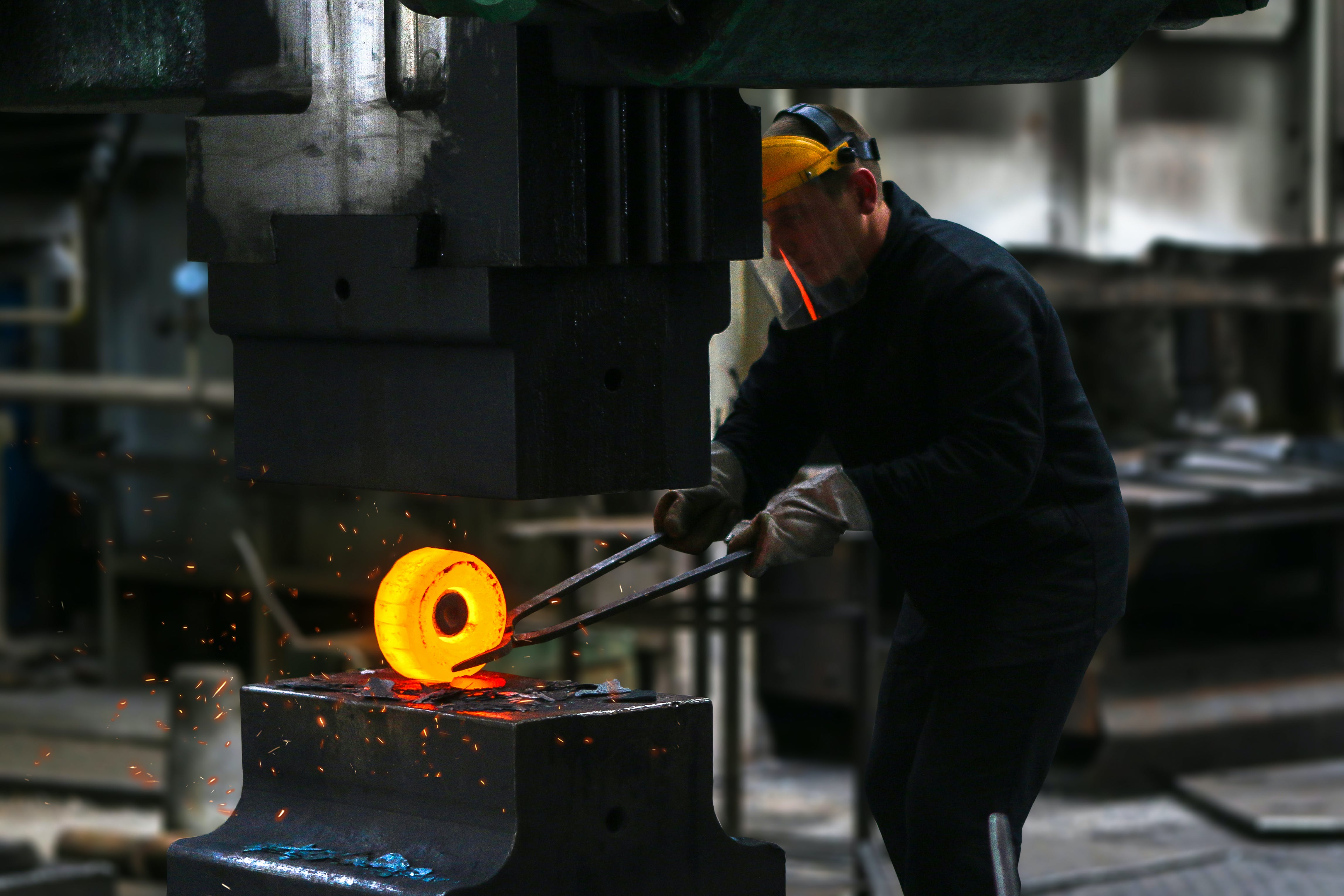
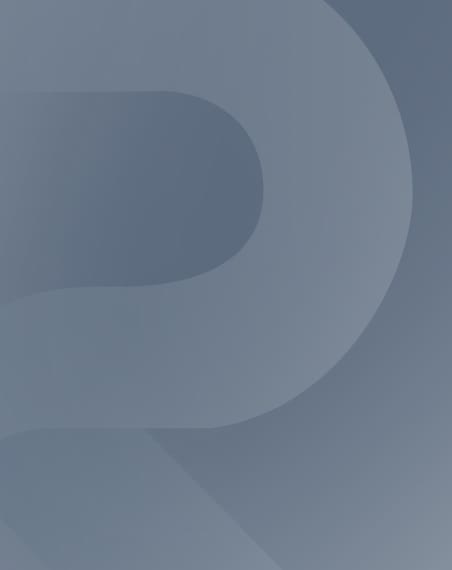
Steel Safety Day: Strengthening safety in a high-risk industry
Steel Safety Day is a reminder that safety must be a shared value across the global steel industry. Established to reduce accidents, it highlights the risks workers face daily, from heavy machinery and extreme heat to hazardous materials, and reinforces our collective responsibility to protect them.
In 2023, World Steel Association (worldsteel) members reported 61 fatalities globally, representing a global fatal frequency rate (FFR) of 0.017, the lowest on record. While this demonstrates progress, steelmaking remains a high-risk industry compared to other sectors. According to worldsteel, on average, 20% of incidents have the potential to lead to serious injuries or fatalities. Without strong safety frameworks, the risks associated with working in the steel industry can have devastating consequences for workers, families, and wider communities.
ResponsibleSteel members are making strong headway in fostering a culture of safety. At Arvedi AST, safety is a shared responsibility from leadership to the frontline. HSE Manager Fernando Camponi explains:
"In Arvedi AST, over the last few years, major efforts have been directed towards increasing the health and safety culture at every level, from management to workers, with particular reference to the key role of supervisors. As an example, we can mention the 'STAR' (Safety Training and Review) project, through which the most expert supervisors check on site the correct application of all safety operating instructions by all workers, providing, if necessary, for their revision or updating."
Meanwhile, Outokumpu has embraced technological innovation to enhance safety. Thorsten Piniek, VP of Health & Safety, comments:
"Safety of our people is our first priority. During 2024, we maintained world-class safety performance. We have implemented a structured way of doing safety behaviour observations and learning from each other across the organisation. Last year, our preventive safety actions were up 5% since 2023, so our people have done a fantastic job! In addition, our three safety robots utilising AI helped us reduce our employees' exposure to hazardous areas."
There is also a financial benefit to investing in health and safety. A 2017 study by the Institute for Work & Health in Canada found that employers investing in occupational health and safety in the manufacturing sector earned on average an estimated return of 24%.
As technology advances, so does our ability to prevent harm within the steel sector. But lasting progress relies on culture: empowering workers, building trust, and making safety the priority and default. A sustainable steel industry must first and foremost be a safe one.
At ResponsibleSteel, health and safety are core to our International Production Standard, as they are fundamental to a sustainable industry. The Occupational Health and Safety (OHS) principle embedded in our Production Standard ensures that the safety of workers is prioritised at every level of steel production. A sustainable industry must be safe for the people who power it, and without proper protections in place, there can be no true social or environmental progress.
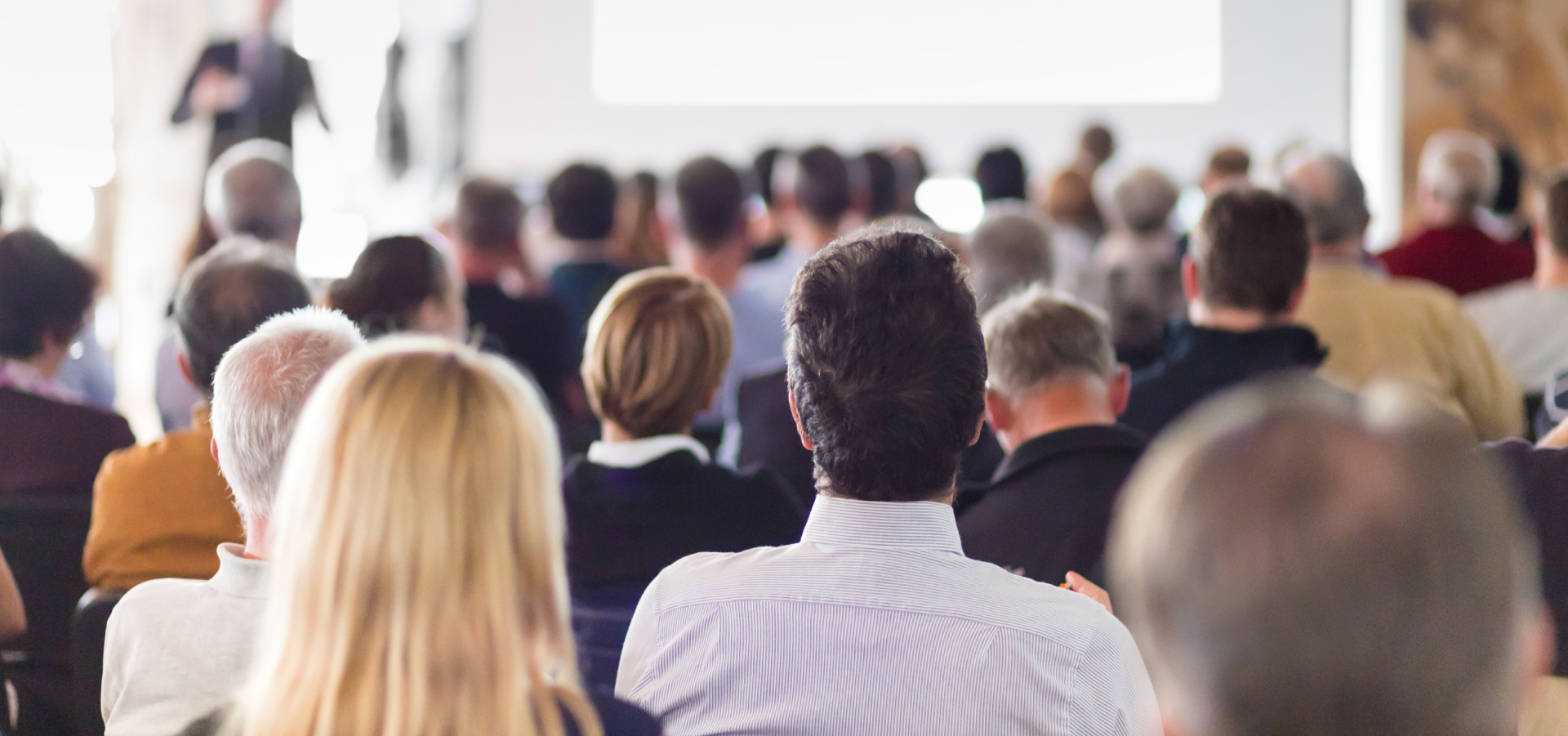
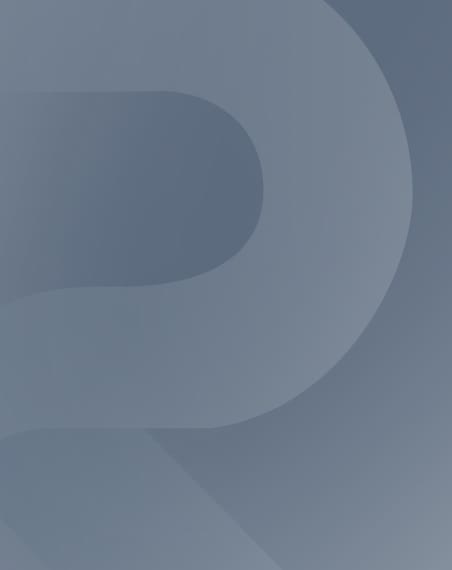
Join us at our upcoming Annual General Meeting
We are pleased to invite ResponsibleSteel members to the 2025 Annual General Meeting (AGM) of ResponsibleSteel Ltd on Monday, 19 May 2025. The meeting will be held online via Microsoft Teams.
Time:
- AGM: 12:00 – 12:30 (GMT+1)
- Members Meeting: 12:30 – 13:30 (GMT+1)
Agenda:
- Chair’s Report
- CEO’s Update
- Financial statements and reports
- Announcement of the results of the election of Directors
Registration in advance is required to attend the AGM and Members Meeting, and members must be up-to-date with their membership fees to be able to join and participate in any votes. We encourage all members to register and participate in the call.
The AGM will be followed by a Members Meeting, during which we will explore the latest developments around ResponsibleSteel and what’s in store for the rest of the year. Members will also have the chance to ask questions and provide input on a number of topics.
If you have any questions or would like to register, please contact our membership team.
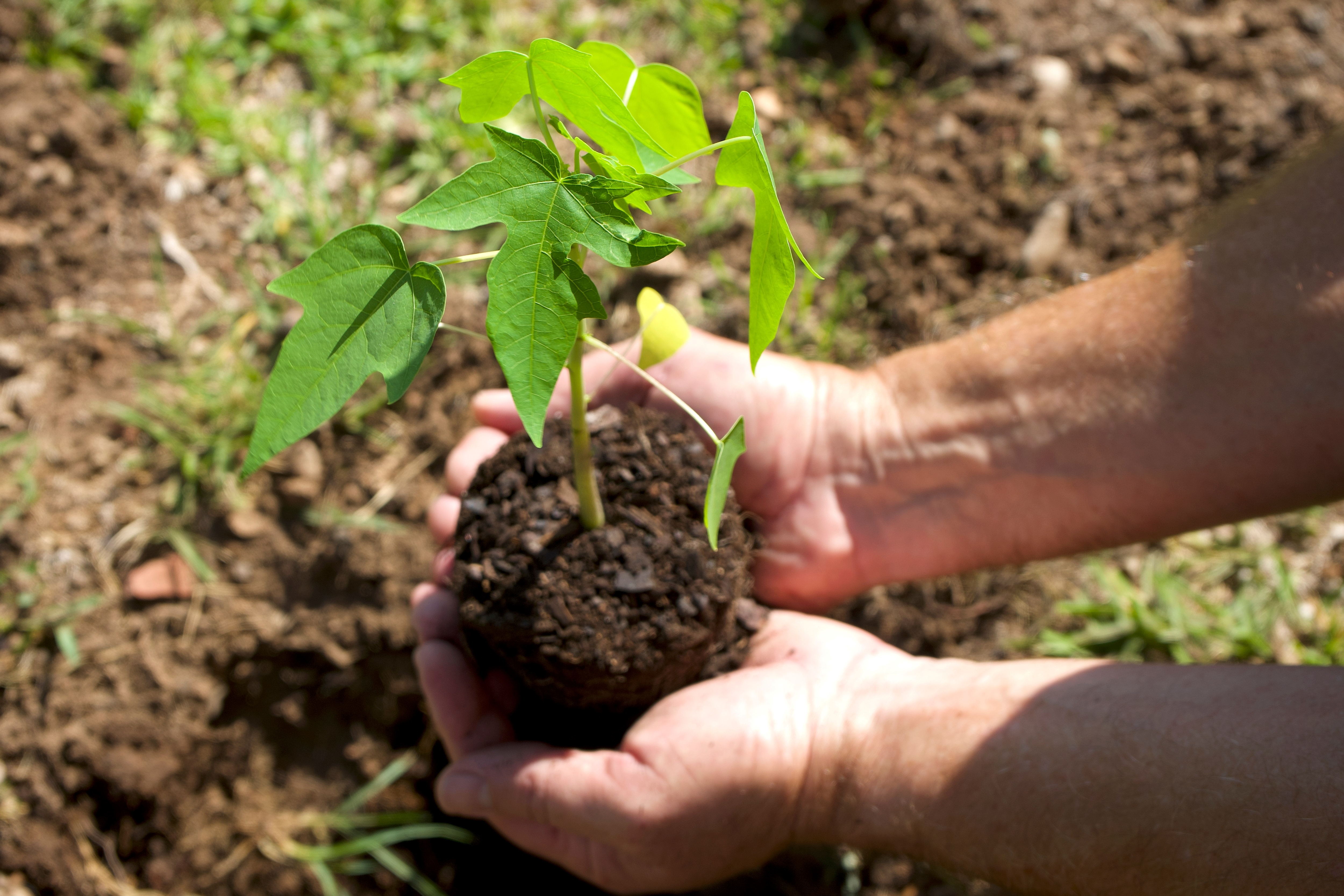
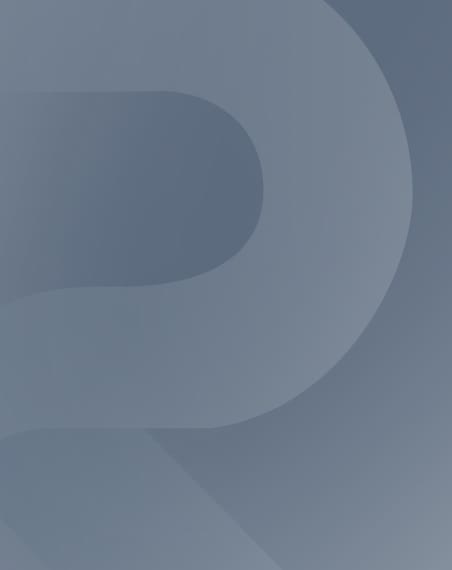
Earth Day 2025: Advancing sustainability in the steel industry
Earth Day is a moment to reflect on our relationship with the planet, and a call to protect the ecosystems and communities that sustain us. As we face accelerating climate and environmental crises, it’s clear that good intentions are not enough. Real progress requires meaningful, measurable action.
Steel is an essential part of modern life, supporting everything from clean energy systems to the infrastructure around us every day. But the way that steel is produced comes with a heavy environmental and social footprint. It’s one of the most emissions-intensive industries, and its impacts on land, water, and people are significant. At ResponsibleSteel, we believe that the future of steel must be aligned with the future of the planet. We unite businesses, civil society organisations, sustainability experts, and other industry stakeholders around a shared vision: that steel can—and must—be produced in a way that is environmentally and socially responsible. Our work is grounded in a set of shared principles that reflect the full scope of sustainability, including climate action, biodiversity protection, responsible resource use, and respect for human rights.
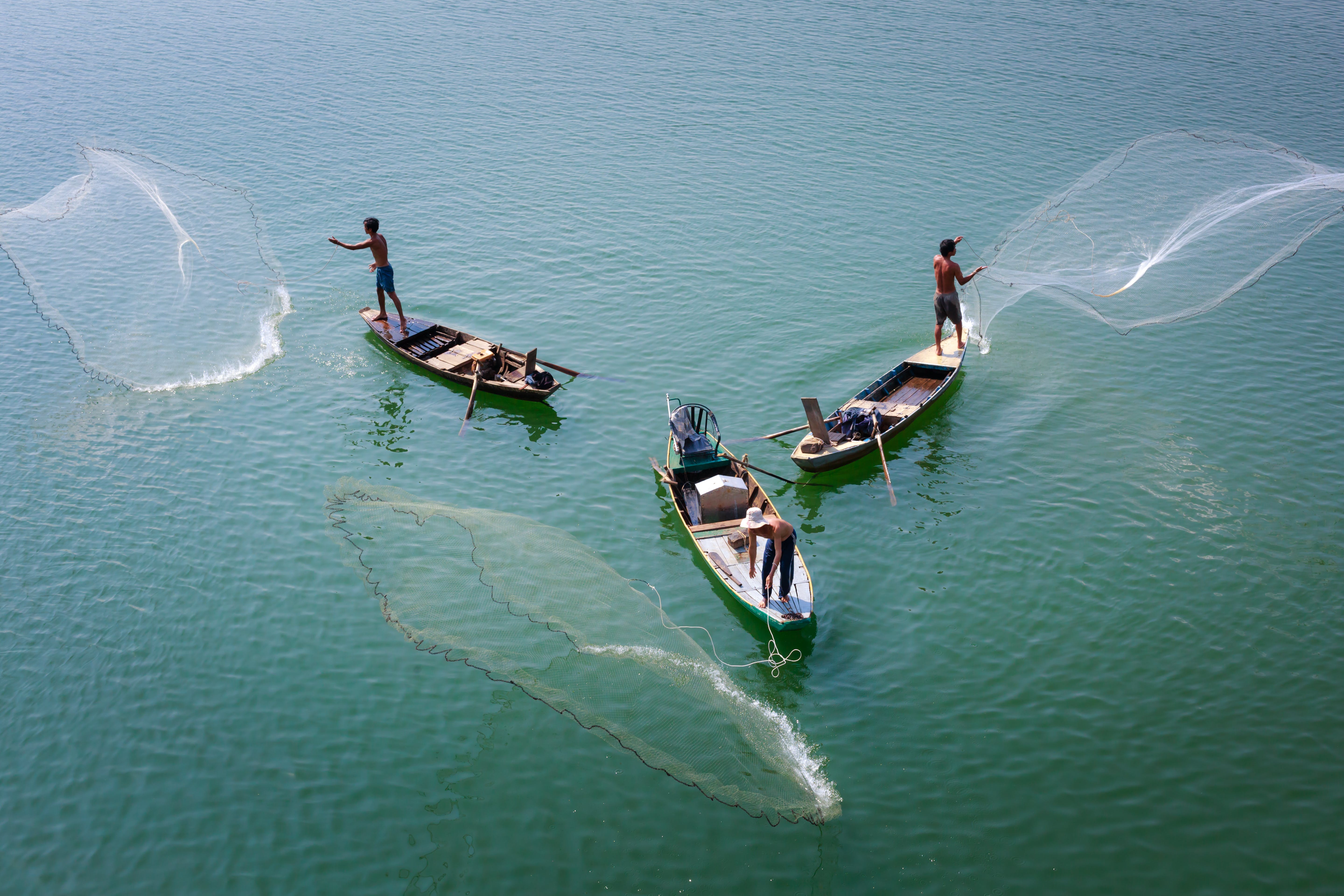
For example, our Biodiversity Principle aims to ensure that sites actively protect nature by respecting conservation areas, avoiding harm to high-value habitats, and following the mitigation hierarchy to reduce impacts. Sites are expected to assess biodiversity risks and aim for no net loss, and even a net gain, where critical habitats are involved. Our Water Stewardship Principle calls for a clear understanding of how water is used and shared in each location, with strong planning to protect water quality, support local communities, and safeguard stressed resources. By setting clear expectations like these across our Production Standard, we’re helping drive the changes the steel industry needs.
Earth Day is a reminder that environmental and social responsibility are inseparable. Steel may not be the first thing that comes to mind when we think about nature or climate, but it plays a central role in shaping both. The transformation of the industry is already underway, and must continue apace, driven by accountability, urgency, and collaboration. We don’t produce steel, but our work ensures that when it is made, it’s done with consideration for people and the planet. Because a thriving Earth requires responsible progress in every sector, including steel.
Learn more about how we’re supporting change here.
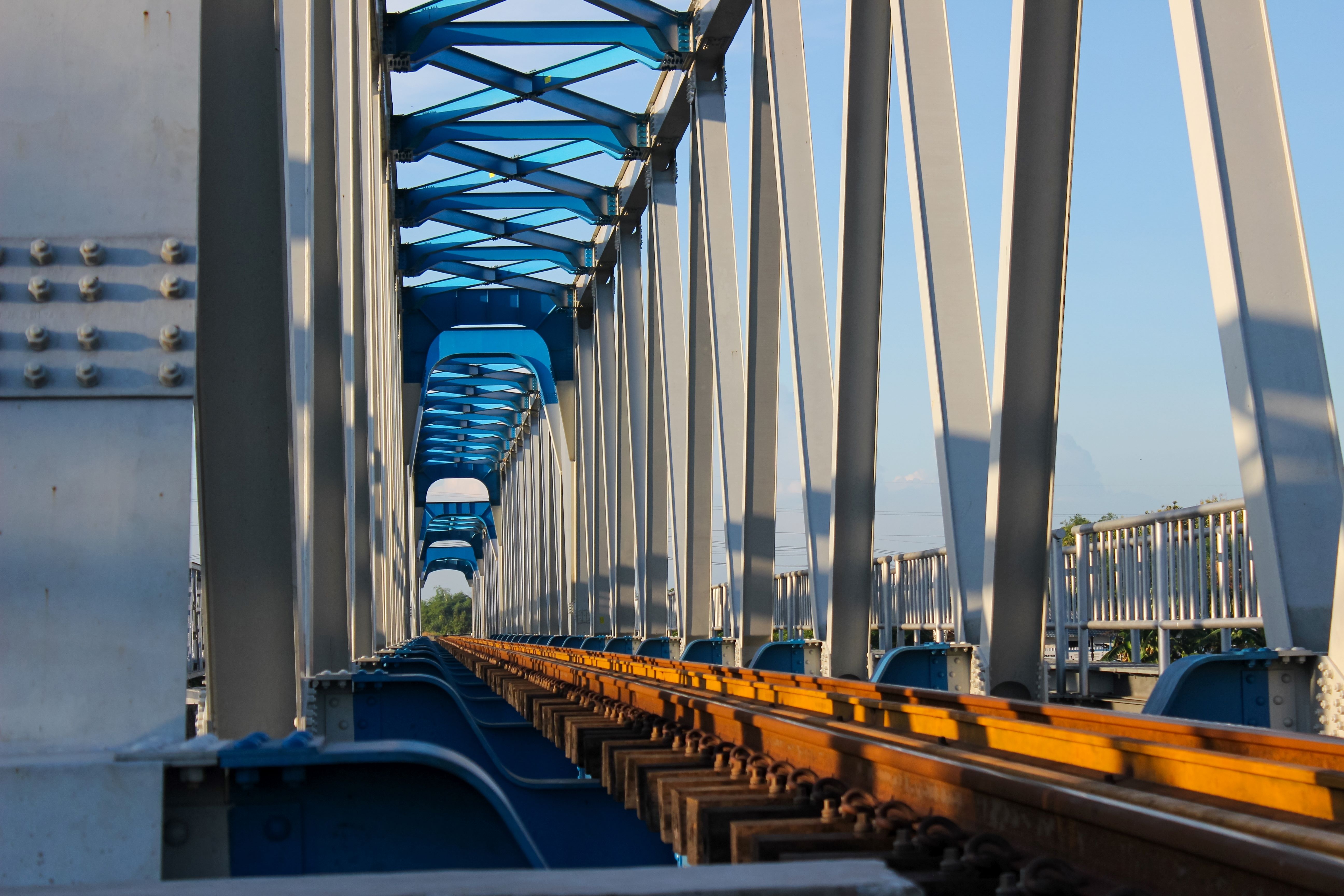
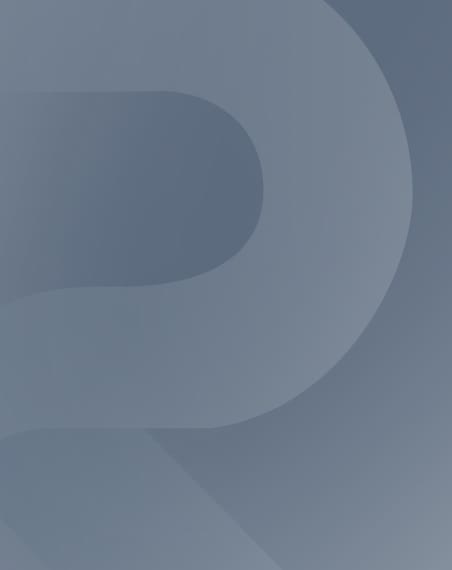
March 2025 Newsletter
This month, we were delighted to see JSW achieve its first ResponsibleSteel certifications for four sites in India, covering 83% of the company’s national steel production—an important milestone for Indian steel. And as steel policy continues to evolve rapidly worldwide, we've provided a summary of key developments from the EU, UK, China, and beyond.
We also celebrated International Women’s Day by highlighting the women driving change across the steel supply chain. In recognition of Global Recycling Day, we reflected on the history of steel recycling and the valuable lessons it offers in the journey toward responsible near-zero steel.
Additionally, we’re pleased to welcome three new members to the ResponsibleSteel community—PRCO America, ABS, and Yeşilyurt Demir Çelik. Welcome aboard!
In this newsletter, you will find updates on:
- New certifications
- New members
- Policy developments
- Upcoming audits and training
- Member survey results
- And more...
Click here to read the full newsletter.
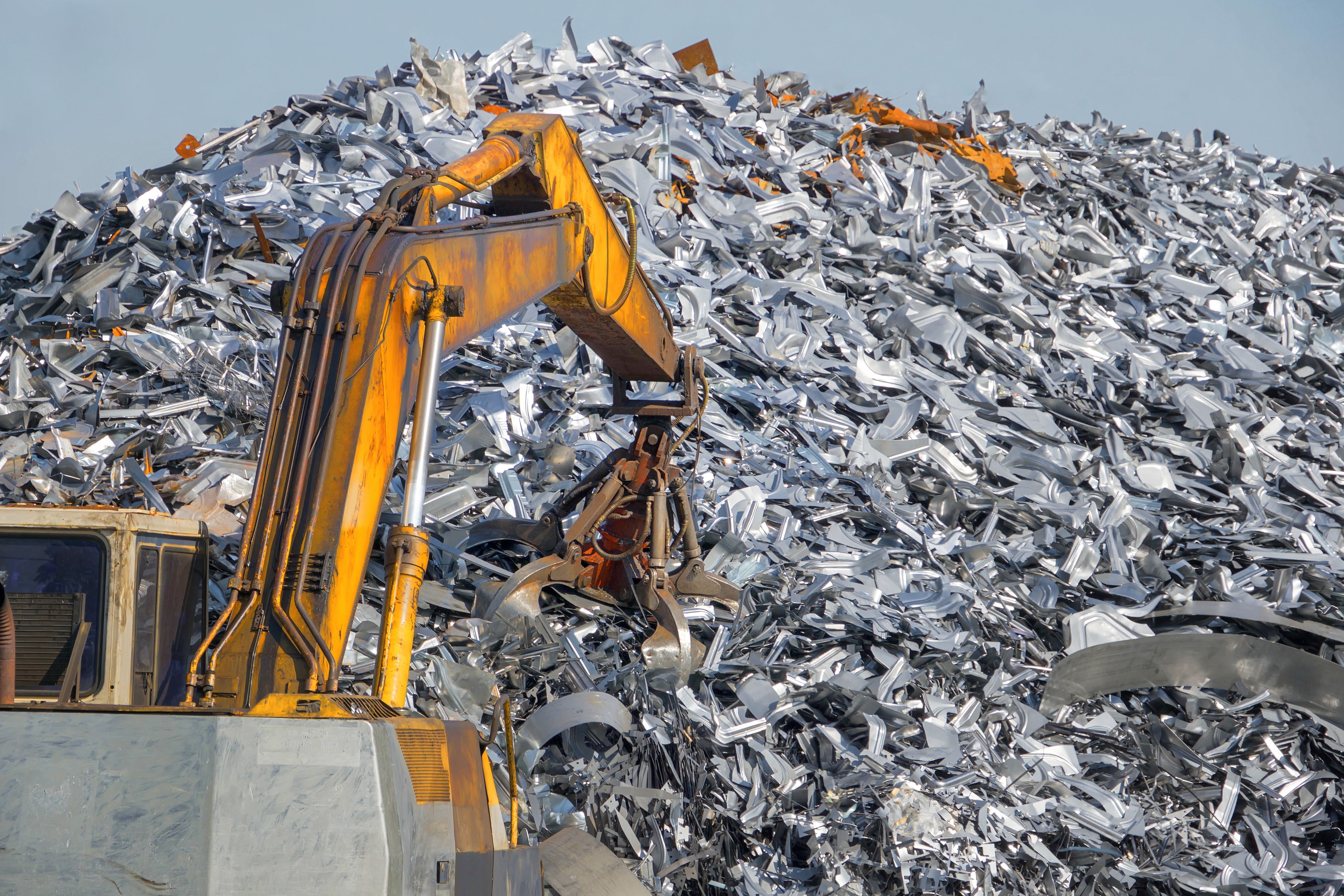
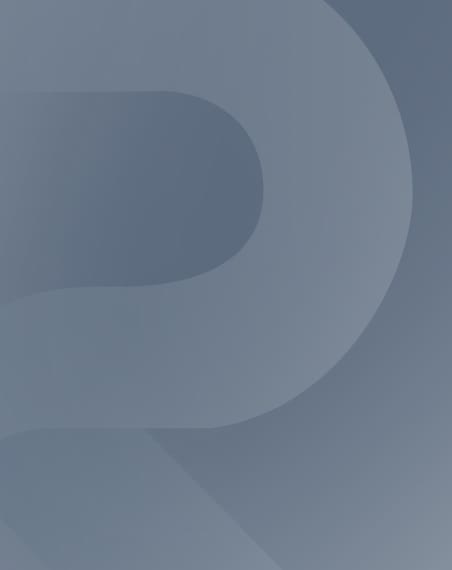
Global Recycling Day: Analysing the role of scrap in steelmaking through the years
To mark Global Recycling Day, Matthew Wenban-Smith reflects on the history of steel recycling and what it tells us about the transition to a net-zero steel economy in the future.
When it comes to recycling, it is worth taking the long view. For the first few thousand years, iron and steel recycling meant reworking rather than re-melting. The development of the blast furnace around one thousand years ago made it possible to convert steel scrap into liquid metal. And the first commercial Electric Arc Furnace (EAF), capable of using 100% scrap, was built in 1906.
Smaller, less costly to build, and more flexible to operate than blast furnaces, the spread of EAFs through the 20th century was limited only by the availability of scrap and electricity.
In the US, as demand for new steel approached saturation and as the steel in infrastructure and buildings constructed 40 or 50 years previously became available for recovery and recycling, scrap-based EAF production began to replace blast furnace steelmaking, even as the blast furnaces themselves used more scrap. Blast furnace production peaked in 1969, and no new blast furnace has been built in the US since 1980 (Construction Physics, 2023). Today, around 70% of steel in the US is made in EAFs (American Iron and Steel Institute, 2021).
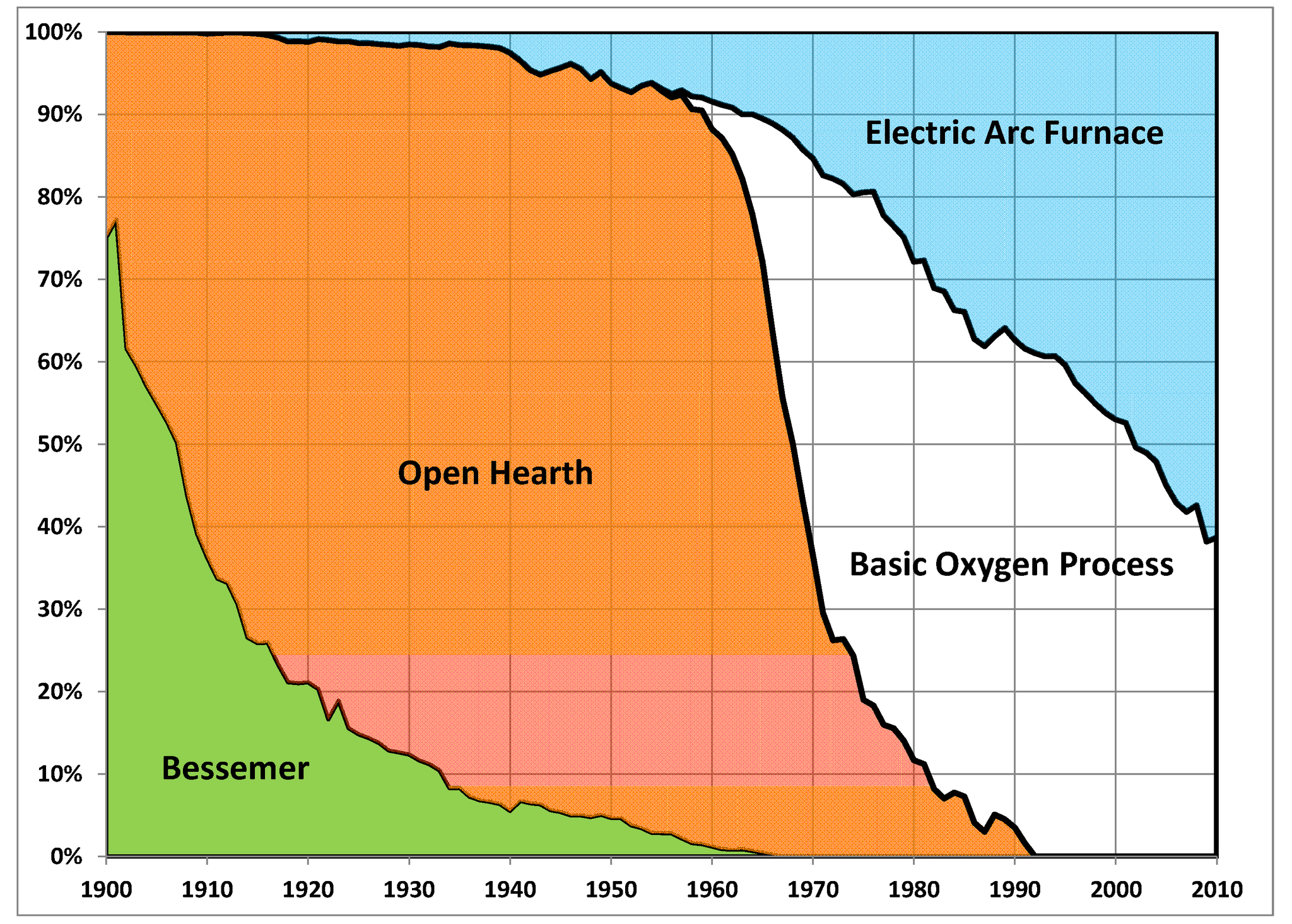
The same pattern of increasing demand, met initially from primary production and then later through a growing reliance on scrap, is now playing itself out in Europe and China, is set to take off in south Asia, and it is to be hoped will roll out across Africa. Steel production globally is projected to peak in the second half of the 21st century, with scrap supply following 30 or 40 years after that.
The growth of scrap-based production has been driven by economics, of course, rather than by any concerns about the climate or greenhouse gas emissions – but that doesn’t make it any less welcome. A tonne of steel made entirely from scrap has around one-fifth of the greenhouse gas emissions of a tonne of steel made from iron ore.
Does that mean we can all relax, and recycle our way out of the climate crisis? Sadly not.
The American Iron and Steel Institute (AISI) estimates that the USA now recycles between 70% and 80% of all of its potentially available scrap (AISI, 2021). The World Steel Association (worldsteel) puts the global recycling rate even higher than that, at around 85% for end-of-life scrap.
Then why, despite these impressive recycling rates, is there currently only enough scrap to meet around one-third of the global demand for steel? The main reason is that scrap availability reflects the level of steel production a generation ago, rather than today. Steel production in 1985 was around 720 million tonnes. Today it is around two billion tonnes. Even without taking account of end-of-life recovery and furnace yield losses there is no way to make those numbers add up.
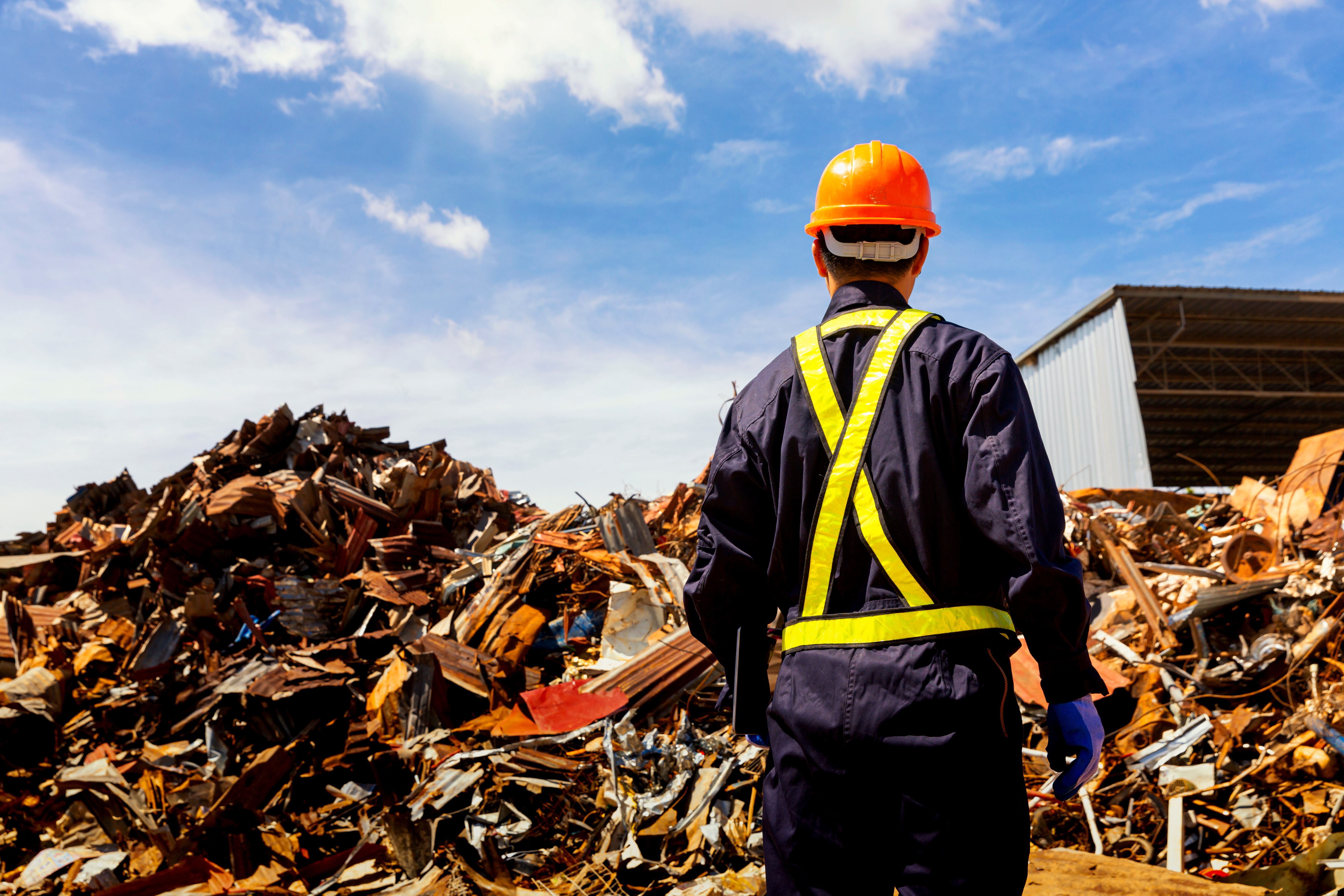
As demand for steel levels off in the future, a higher proportion of that demand will be met from scrap. In its ‘Sustainable Development Scenario’, in which the end-of-life recycling rate rises to 90%, the IEA estimates that there would be enough scrap to meet 45% of the demand for steel in 2050 (IEA, 2020). That is something to celebrate. But to put it the other way around, it would mean that 55% of the world’s steel – perhaps 1.2 billion tonnes of it – would still be made directly from iron ore.
To have any chance of limiting climate change to ‘well below 2 degrees’ and at the same time respecting the aspirations of 9 to 10 billion people, two things therefore need to happen. Firstly, the vast majority of primary steel will need to be made using ‘near zero’ emission sources of iron – using hydrogen-based direct reduction iron (DRI), direct electrolysis, biofuels, carbon capture or other new processes. And secondly, the electricity used in steelmaking will need to be generated with near zero emissions, whether it is used to power electric arc furnaces, hydrogen production, or direct electrolysis.
Those are the twin challenges for policy makers, steelmakers and steel users, and they apply across the whole sector.
To meet those challenges, they, and we, need to be able to compare the GHG emissions performance of all steelmaking on a like-for-like basis, whether steel is made from 100% scrap, 100% primary iron, or from any ratio of inputs in between – an approach pioneered in the ResponsibleSteel Production Standard, and recommended by the IEA, German Steel Association and others.
So let’s hear it for the recyclers, but also for the ‘near zero’ power generators, and the ‘near zero’ iron innovators.
And for a successful transition to a net-zero steel economy.
By Matthew Wenban-Smith
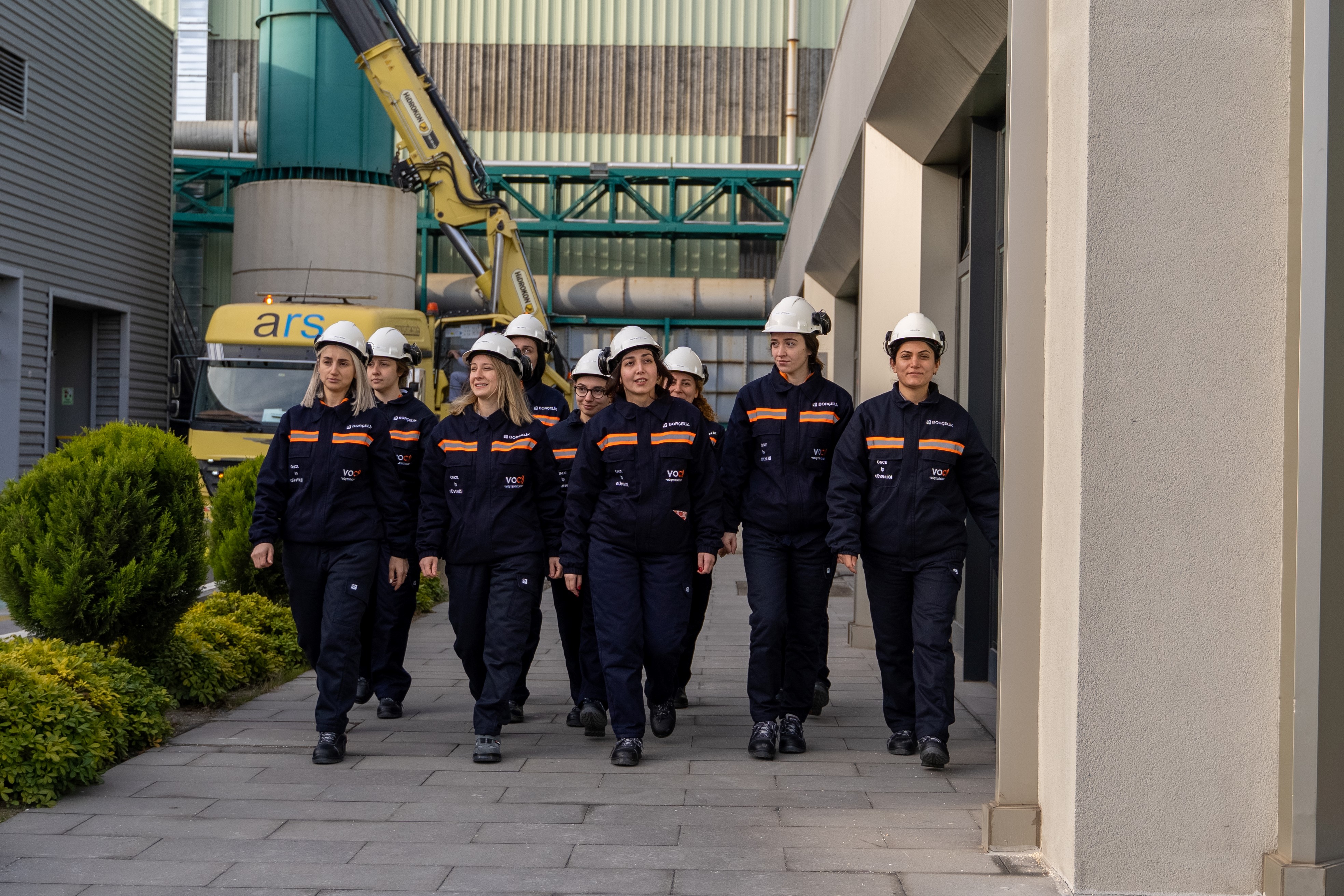
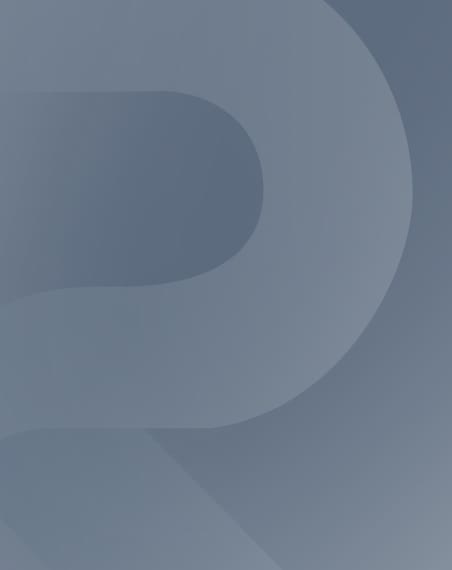
International Women's Day: Celebrating women working across the steel supply chain
In the second half of the twentieth century, women's participation in the global workforce grew remarkably. In the United States, female participation in the workforce surged from around 33% in 1948 to over 50% by the late 1970s (U.S. Bureau of Labor Statistics). Similarly in Europe, countries like France and Germany saw a rise from around 45% in the 1960s to over 60% by the 1980s (OECD, 2021). And in South America, Brazil also witnessed significant progress, with participation growing from approximately 18% in 1960 to 40% in 1980 (World Bank, 2020).
Despite these advancements, industries like steel, mining, and metals remained predominantly male-dominated. A 2019 broad analysis of 66 global steel, metals, and mining companies revealed that women made up between just 3% and 29% of the workforce (S&P Global). Within the steel industry specifically, women account for only about 15% of the workforce, a figure that has remained largely unchanged over the past decade (World Steel Association, 2020). These figures illustrate the persistent challenges to achieving gender diversity within the steel and metals sectors, underscoring the need for continued progress.
As workplaces evolve and diversity initiatives gain momentum, more women are entering and excelling in traditionally male-dominated sectors. Their contributions are driving innovation, improving workplace culture, and challenging longstanding societal barriers.
In recognition of International Women’s Day, ResponsibleSteel is spotlighting a few of the women who are driving change across the steel supply chain – celebrating their impact, resilience, and leadership and emphasising the need for greater diversity and inclusion in the metals sector.
Above image courtesy of Borçelik
.png)
Elle Gatto
Assistant Team Leader - Finished Product Shipping, ArcelorMittal Dofasco
Elle has been with ArcelorMittal Dofasco for just over five years. As an Assistant Team Leader in Finished Product Shipping, she's passionate about working on the floor and ensuring steel moves efficiently. Her department is the last line of defense - she takes great pride in knowing that her role contributes to guaranteeing that only the highest-quality steel reaches customers. For Elle, being part of a team that keeps production running smoothly is rewarding and motivating, and she's looking forward to continuing to grow in the industry.
What is it like to be a woman in the steel industry?
"Being a woman in the steel industry has its challenges, but also presents unique opportunities for growth and leadership. It's empowering to contribute to an industry that is traditionally male-dominated, proving that diversity leads to stronger teams and more creative solutions. While there may be moments of being one of the few women in the room, I see it as a chance to break barriers and inspire the next generation of women in manufacturing and engineering fields."
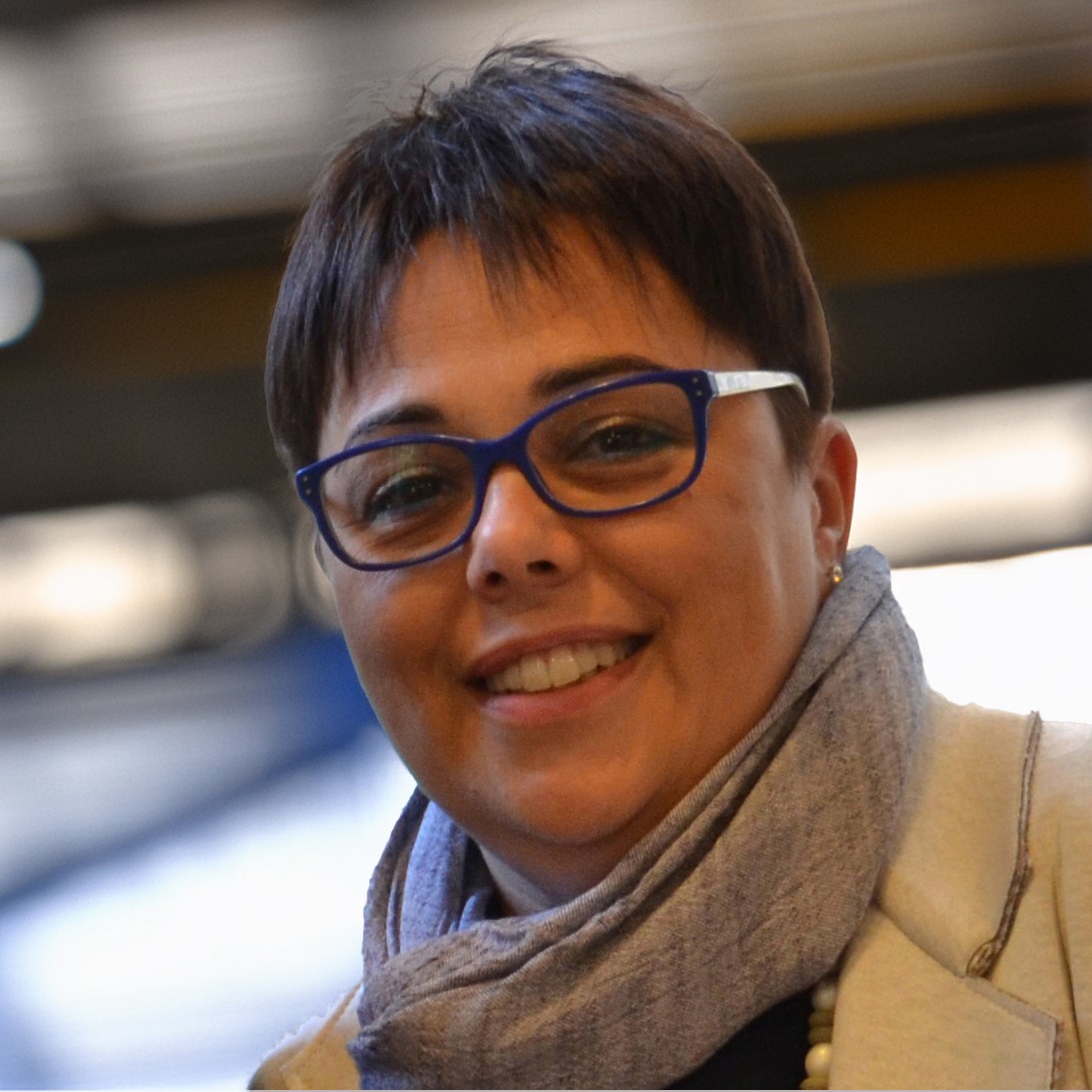
Stefania Bonaiuti
Supplier Carbon Neutral, SKF
Stefania began her 28-year journey at SKF working in bearing product lines and later serving as the marketing manager for steel-related offerings. Currently, she focuses on Supplier Carbon Neutral deployment. Her career spans sustainability projects aimed at achieving net zero carbon emissions. Her experience in the steel industry and commitment to promoting sustainable practices continue to play an important part in advancing SKF's sustainability initiatives. She values the diverse perspectives women bring to the industry and actively supports gender balance and leadership development programmes at SKF.
What are your hopes for the future of the steel industry?
"Over the years, I have encountered many women in this field who brought diverse perspectives and innovative solutions, which are valuable in an evolving industry. Therefore, ensuring gender diversity remains crucial.
The future of the steel industry holds immense potential, rooted in sustainability, innovation, and inclusivity. Embracing cutting-edge technologies will enhance efficiency and reduce environmental impact. At SKF, we drive innovation with steel products that support our customers' sustainability goals. Collaboration within the industry and with other sectors is essential for sustainable change. We are proud to be part of initiatives like ResponsibleSteel, SteelZero, and RE100. By sharing knowledge and leveraging each other's strengths, we can tackle challenges effectively and drive the industry towards a more sustainable and prosperous future."
It's empowering to contribute to an industry that is traditionally male-dominated, proving that diversity leads to stronger teams and more creative solutions. - Elle Gatto, ArcelorMittal Dofasco
Tuana Çabuk
Production Engineer - Continuous Galvanizing Line, Borçelik
Tuana graduated with a degree in Mechanical Engineering. She has been working as a Production Engineer in the Continuous Galvanizing Line at Borçelik for two years. As a production engineer, she takes part in projects related to occupational safety, production processes, and quality performance of the lines she is responsible for.
What is it like to work in the steel industry?
"The steel industry is highly competitive and involves production processes that require advanced technology. As a result, it demands strong expertise in both engineering and production. Being actively involved in production processes and participating in various projects helps me to develop myself to be a better engineer. Since the steel industry is dynamic and requires technical proficiency, I believe that taking an active role in the manufacturing field, especially as a production engineer, provides a significant advantage.
Although the workforce is predominantly male, I take pride in contributing to the industry and promoting diversity as a female engineer. Gender diversity is a crucial issue, but I believe it should not be measured by having an equal number of men and women in every setting. Instead, it should be achieved by ensuring equal opportunities and a fair working environment for everyone. I feel fortunate to work in an organisation that supports this principle."
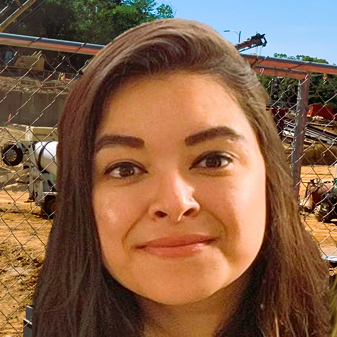
Dr. Ankita Gangotra
Senior Manager, World Resources Institute US
Ankita leads WRI's efforts to decarbonise the industrial sector through technology and policy innovation. Her work focuses on decarbonising the cement and steel industries, climate-oriented trade policies, green procurement standards, and fostering international cooperation. Ankita’s work includes advising U.S. policymakers and supporting industrial decarbonisation efforts in countries like India. Previously, she was a postdoctoral research fellow at Georgetown University, where she researched technology and policy options for industrial decarbonisation in the U.S.
What is it like to be a woman working on steel and heavy industry?
"I was apprehensive when starting work on the steel and industrial sector more broadly due to its male-dominated nature, but I’ve been inspired by the incredible women working on steel decarbonisation and their fierce advocacy. It’s been empowering to be surrounded by such passionate colleagues who are driving meaningful change. I hope we can accelerate the pace of steel decarbonisation while ensuring a just and equitable transition that benefits both communities and workers in the sector."
It's been very nice being a mentor and a point of call for other women. I like to think I've made other women in the industry proud. - Ashlea Muscat, BlueScope
Ashlea Muscat
Operations Manager Painting and Finishing Department, BlueScope
Ashlea joined the industry as a cadet in 2014 straight from university. After eleven years in the industry, she now runs the coil painting and finishing department at BlueScope’s Port Kembla Steelworks, looking after 126 people across 3 units and leading on day-to-day management, development, and process improvement across the department. Women now make up over 22% of BlueScope's site operators, a significant increase from 3% in 2017.
How did you get started in the steel industry?
"I first began in the industry as a cadet and I love all of the problem solving and challenging roles that I've held. It's been very nice being a mentor and a point of call for other women. I like to think I've made other women in the industry proud."
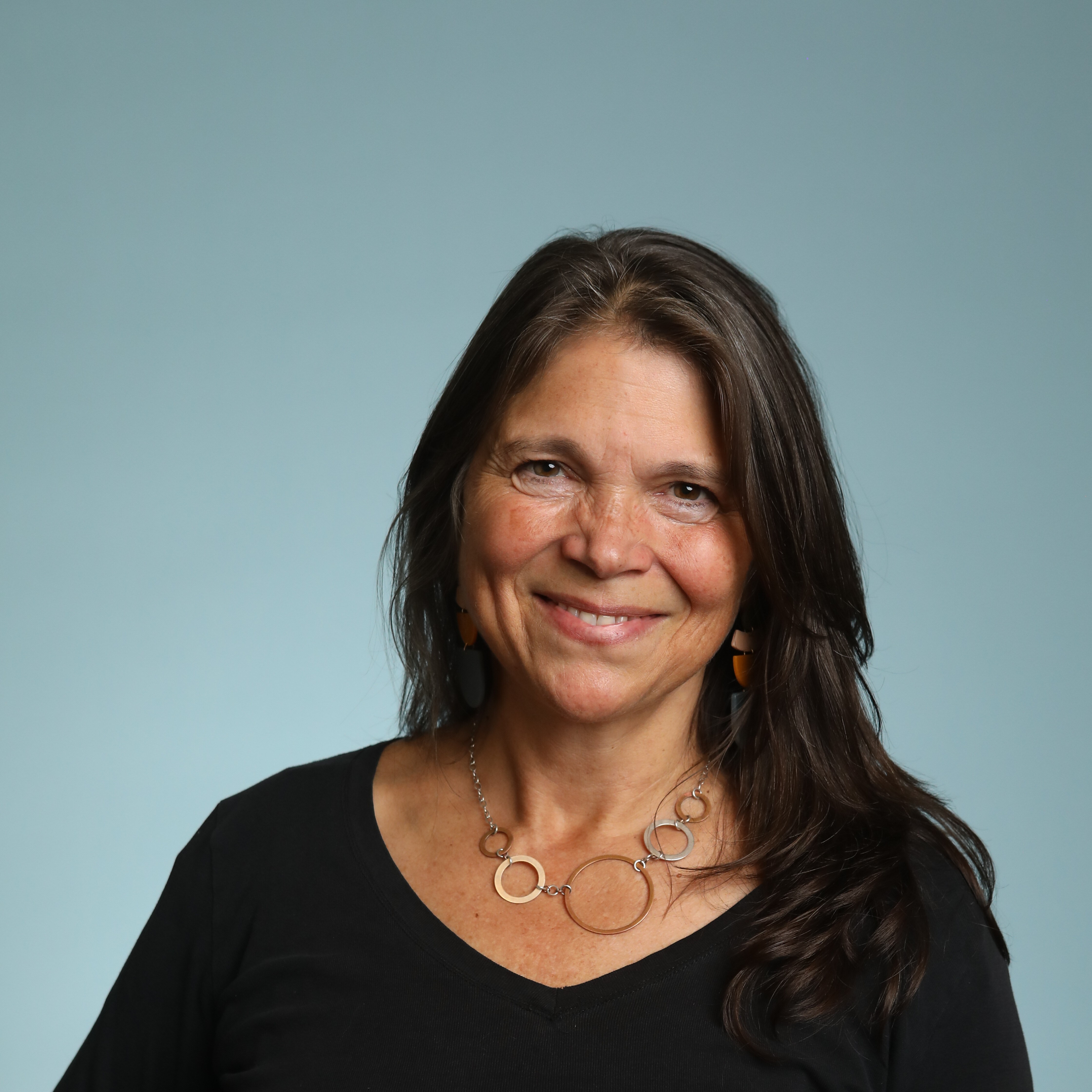
Aimee Boulanger
Executive Director, Initiative for Responsible Mining Assurance
Aimee has worked on mining issues for over 25 years, with substantial experience in directly affected communities. She has served IRMA’s leadership since 2011 and her role is to guide an organisation which is fully accountable to multi-stakeholder leadership, creating market value for more responsible business practices while ensuring credibility and accountability to all stakeholders.
What are your hopes for the future of the steel and mining sectors?
"I hope for a future where companies that create the products we rely on every day are valued not just for what they make, but for how they make it, ensuring that people, their lands, and their wellbeing are respected at every step. This means greater transparency in industries like mining and steel, so we acknowledge our shared impact and work together to reduce harm. And as we do, I hope we centre the voices of women—whose leadership, labour, and lives are so often overlooked—so that the benefits of industry are shared more equitably by all."
I hope for a future where companies that create the products we rely on every day are valued not just for what they make, but for how they make it... And as we do, I hope we centre the voices of women—whose leadership, labour, and lives are so often overlooked—so that the benefits of industry are shared more equitably by all. - Aimee Boulanger, IRMA
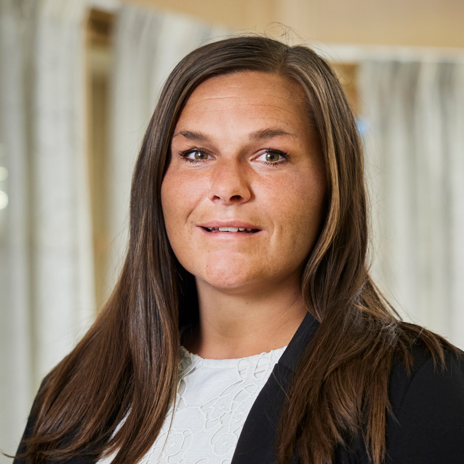
Angelica Olsson
Manager - Safety and Sustainability, Outokumpu
Angelica has worked her whole career in different types of industries. Before joining Outokumpu, she worked for several years in the paper industry as well as in the sawmill industry. She's held various positions, but she has the most experience in Supply Chain Management. She joined Outokumpu in 2018 and her first role was as a Safety Engineer for fire and security issues. Since 2022, she has worked as a Safety & Sustainability Manager.
What is it like to work in the steel industry?
"The steel industry has been by far the most interesting and challenging industry that I’ve worked in. The products we produce are fascinating and we all need to work every day to ensure that the way we produce steel is safe and sustainable. In my role as a Safety & Sustainability Manager, I’m fortunate to work with a great team of safety and sustainability engineers, and together we work hard every day, enabling our mills to produce safe and sustainable stainless steel. I really feel that the work we do makes a difference."
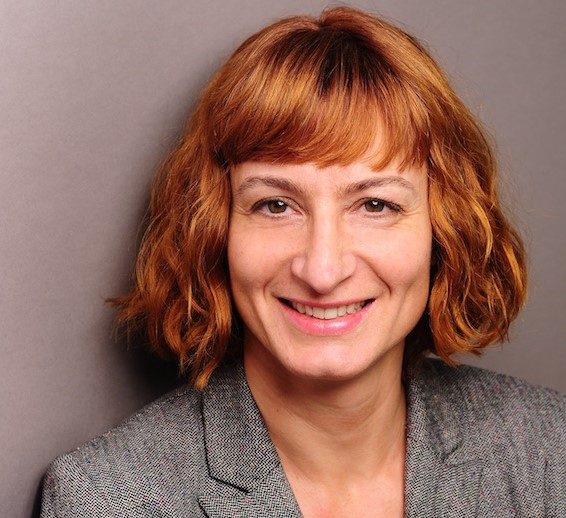
Marnie Bammert
Independent Consultant to ResponsibleSteel
Marnie is an independent consultant with 20 years of experience in developing, implementing and communicating sustainability certification and verification programmes. She has worked with ResponsibleSteel since early 2018. Marnie started her journey in the field of sustainability with oekom Research AG, a rating agency specialised in sustainable and ethical investments. She then moved to the Marine Stewardship Council (MSC), holding various positions including Deputy Director Europe. Since then, Marnie has worked as a consultant on projects ranging from protected areas to infrastructure, mining and nature-based solutions.
Why did you first begin working on the steel industry?
"People tend to focus on GHG emissions when discussing sustainability challenges of the steel sector. But the climate crisis cannot be solved in isolation. Working with ResponsibleSteel, I wanted to raise awareness for other important issues that the sector faces - human and labour rights, biodiversity, water stewardship, to name just a few. They are all connected to the climate question. I am proud to have played an instrumental part in creating the ResponsibleSteel Standard since it brings all of those issues together."
I envision a future for steel where much greater systems thinking, as well as intra- and inter- sector collaboration, drives progress - all enriched by the leadership of women. - Jen Carson, Climate Group
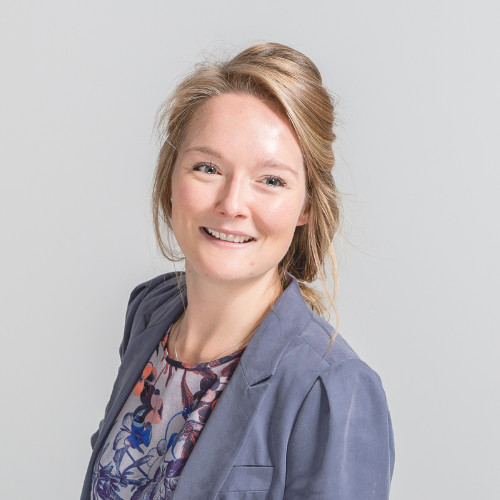
Jen Carson
Head of Heavy Industry, Climate Group
Jen Carson leads the strategy and growth of Climate Group's SteelZero and ConcreteZero. With a decade's worth experience working in the sustainability sector, she works to accelerate heavy industry decarbonisation. Jen joined Climate Group in 2021 after leading energy market research as an Associate at Delta-EE in Australia. Previously, she held various roles at Delta-EE, including creating its first cross-technology research service, as well as at The Carbon Trust, Dunelm Energy, and Kier Group.
What are your hopes for the future of the steel industry?
"I envision a future for steel where much greater systems thinking, as well as intra- and inter- sector collaboration, drives progress - all enriched by the leadership of women. By elevating the contribution of the demand side, and championing a competitive, decarbonised future, we will build a resilient steel industry that sets new standards for what is and isn't acceptable."
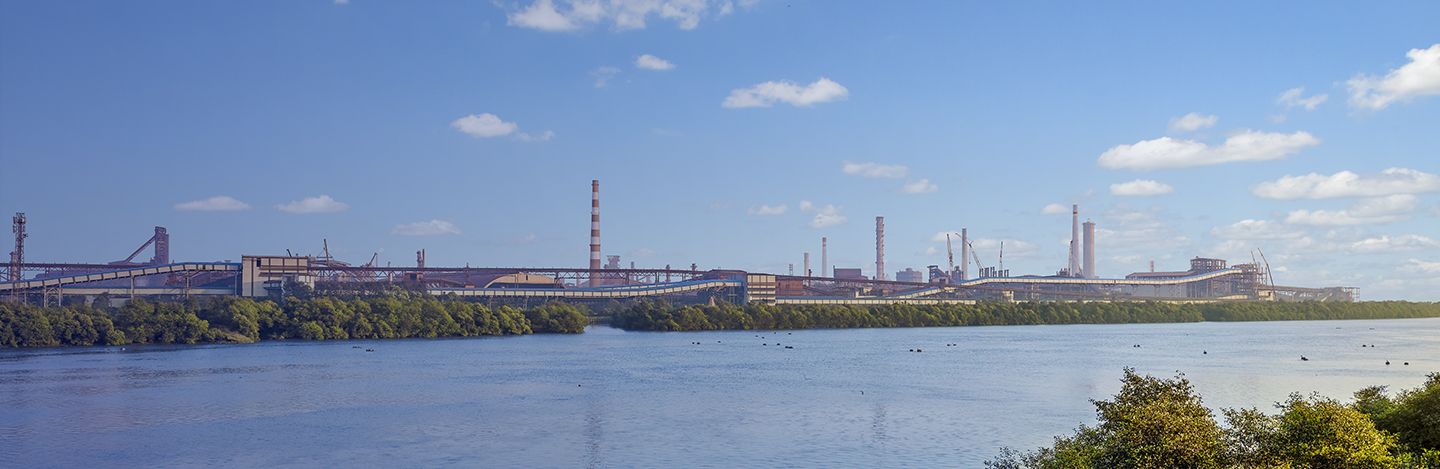
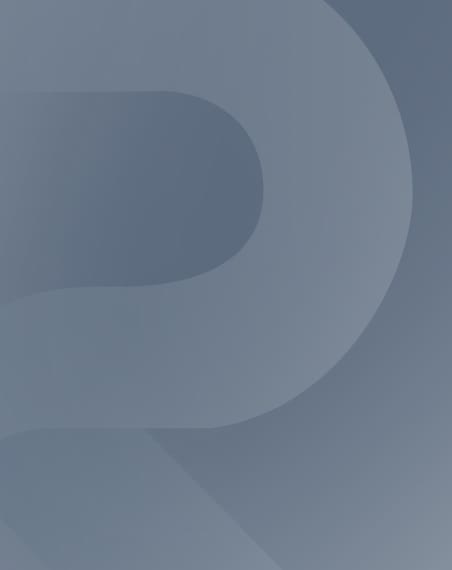
JSW Steel achieves its first ResponsibleSteel certifications for four sites
JSW Steel has achieved Core Site Certification for its Vijayanagar, Dolvi, Salem and Tararpur sites - the group's first certifications against the ResponsibleSteel International Production Standard.
Over the last four decades, JSW Steel has gone from a single unit to a leading steel producer with operations across India and the US. The company's Vijayanagar site has the largest single-site steelmaking capacity in India, able to produce up to 13 million tonnes per annum. The certification of Vijayanagar along with three other sites means that JSW Steel now has 83% of its steel production in India covered by ResponsibleSteel Core Site Certification.
Jayant Acharya, Joint Managing Director of JSW Steel, commented, "The ResponsibleSteel Certification for our 4 sites is a testament to our unwavering resolve to future proof our business by addressing the emerging global challenges while we transition to a sustainable world. I congratulate the team of ResponsibleSteel, the certification body, the assurance panel, and the entire family of JSW Steel for achieving this milestone. We are committed to certifying all our steelmaking sites by 2028."
JSW Steel serves customers across the automotive, machinery, construction, and engineering industries. Together, the four sites employ over 13,000 workers and 29,000 contractors.
Annie Heaton, CEO of ResponsibleSteel commented “Congratulations to JSW for achieving these four ResponsibleSteel certifications. By choosing to adopt an international standard which addresses not only emissions but a wide breadth of environmental and social issues, JSW is demonstrating ambition, foresight and leadership as a global industry player. This means being open to external monitoring, being ready to engage on opportunities for improvement with local stakeholders and laying the foundations for a responsible transition to near zero. As the second largest steel producing country globally, India has a real opportunity to emerge at the helm of the industry’s shift to sustainable practices. JSW's certifications mean that today we’re proud to have some 29% of India’s steel capacity certified against the ResponsibleSteel International Production Standard. We look forward to their next steps in deepening this journey.”
In addition to consulting workers and contractors as part of the audit, several external stakeholders were involved in the process. Representatives from local police, government, NGOs, schools, colleges, hospitals and citizen forums were invited to give input to the audit. Stakeholders had the opportunity to discuss the performance of the site in relation to health and safety, training opportunities, environmental issues, and the site's impact on the local community.
Take a look at the certificates and public audit summaries here.
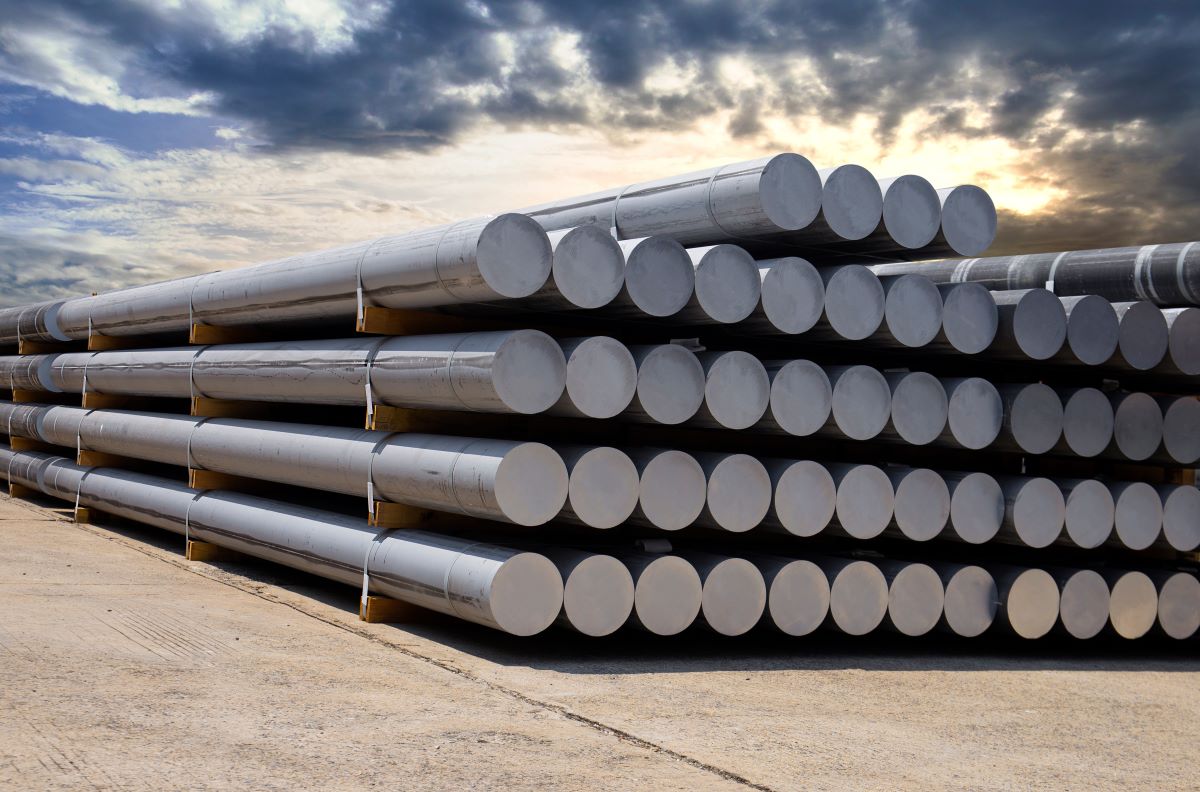
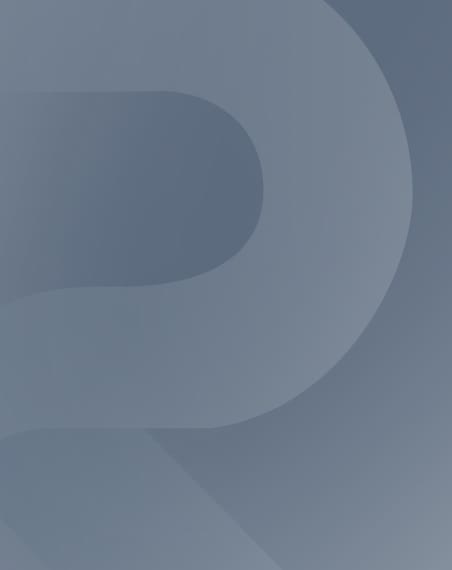
February 2025 Newsletter
This month, we’re excited to share valuable new resources with members and stakeholders to help you talk about ResponsibleSteel. Our new explainer video highlights the value of our programme, and we’ve published several guides on key areas - perfect for sharing with your internal and external stakeholders.
The survey results are in, offering insights to shape our priorities for the year ahead. Auditors can now join our first training sessions of the year for a deeper dive into the Core and Progress Level requirements, and we have published a blog examining our project on standards' role in a just transition.
In this newsletter, you will find updates on:
- Our new animated explainer
- Upcoming auditor training dates
- Events we are attending
- Our new guides to ResponsibleSteel
- Member survey results
- And more...
Click here to read the full newsletter.