Maximising Circular Economics for Decarbonising Steel
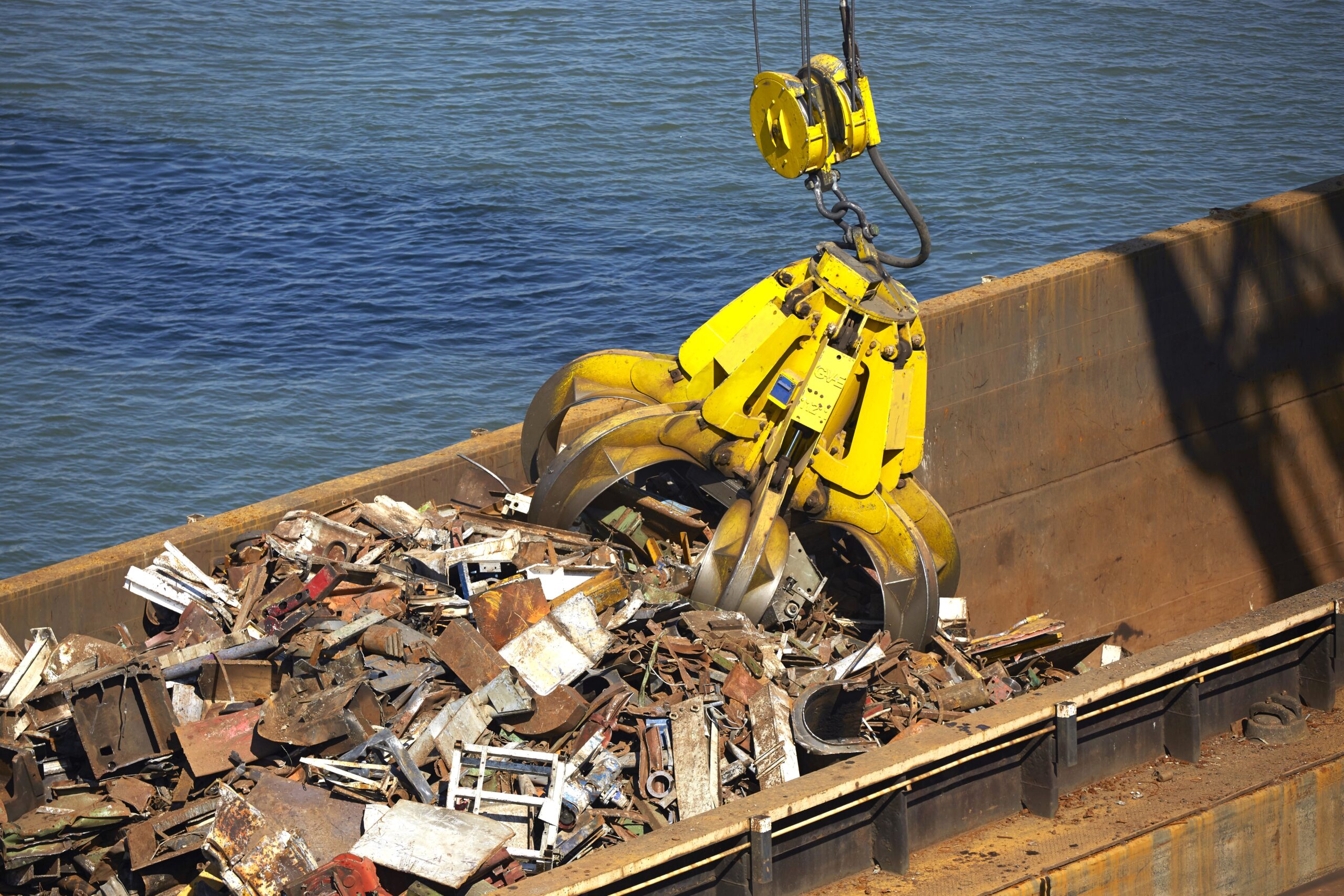
The climate challenge for the steel industry is now well-established. Steelmaking currently accounts for between 7% and 9% of global CO2 emissions. We have not only the opportunity to do things differently across the industry, but it is vital if we are to drastically reduce the amount of emissions emitted from the steel value chain, and so have a real and lasting impact on people and the planet.
Steel is often talked about as the world’s most circular material. Maximising the recovery and use of recycled steel (i.e. scrap steel) is a critical lever and the most natural way to drive decarbonisation in the steel industry. The rates of scrap recovery today are extremely high – the highest of all materials. Worldsteel estimates that steel is recovered at a rate of 85% on average – far more from some product markets. Still, there is always opportunity for further progress. And yet, frustratingly, scrap alone is just not sufficient to meet global steel demand, and even if the use of scrap was maximised, published models tell us that it won’t provide more than half of what we need to get us to net zero by 2050 (International Energy Agency, 2020).
Clearly, as more and more buildings, cars and washing machines reach the end of their useful life, we must ensure that every last tonne of scrap is recovered, in order to produce lower-footprint steel products. But this alone will not be enough if we are serious about net zero by 2050.
It is absolutely vital that we also incentivise the decarbonisation of the only other alternative, the reduction of iron ore, however this is done, and however much scrap is available to complement it. And this is why the ResponsibleSteel International Standard adopts a ‘sliding-scale’ approach to incentivise decarbonisation across all steelmaking, regardless. In effect, our thresholds provide an equitable and effective mechanism for assessing progress on core decarbonisation across the sector and have been echoed and endorsed in numerous reports, proposals and schemes, by the International Energy Agency (IEA), Science Based Targets Initiative (SBTi), the Sustainable Steel Principles, the German Steel Federation and the Australian Green Buildings Council.
There is also a third dimension here. Let’s not forget that to maximise the progress to a net zero world, we need product design to create more value from every tonne of steel we produce and so reduce demand overall. A car made with stronger steel requires less material. Ball bearings that last longer will not need to be replaced so often. In each market, therefore, policymakers will need to reward product design that lengthens the product lifetime, reduces the amount of steel needed for a given purpose, and rewards the reuse and remanufacturing of steel products.
All these three elements – scrap recycling, demand efficiency, and decarbonisation progress – will be needed to get the steel sector to net zero within the next three decades. But how much the first two of these levers can contribute will be critical to understanding the scale of the decarbonisation progress challenge. In the coming months, ResponsibleSteel will be publishing further analysis of both scrap availability and steel demand to shed further light on what is undoubtedly the industry’s biggest challenge.