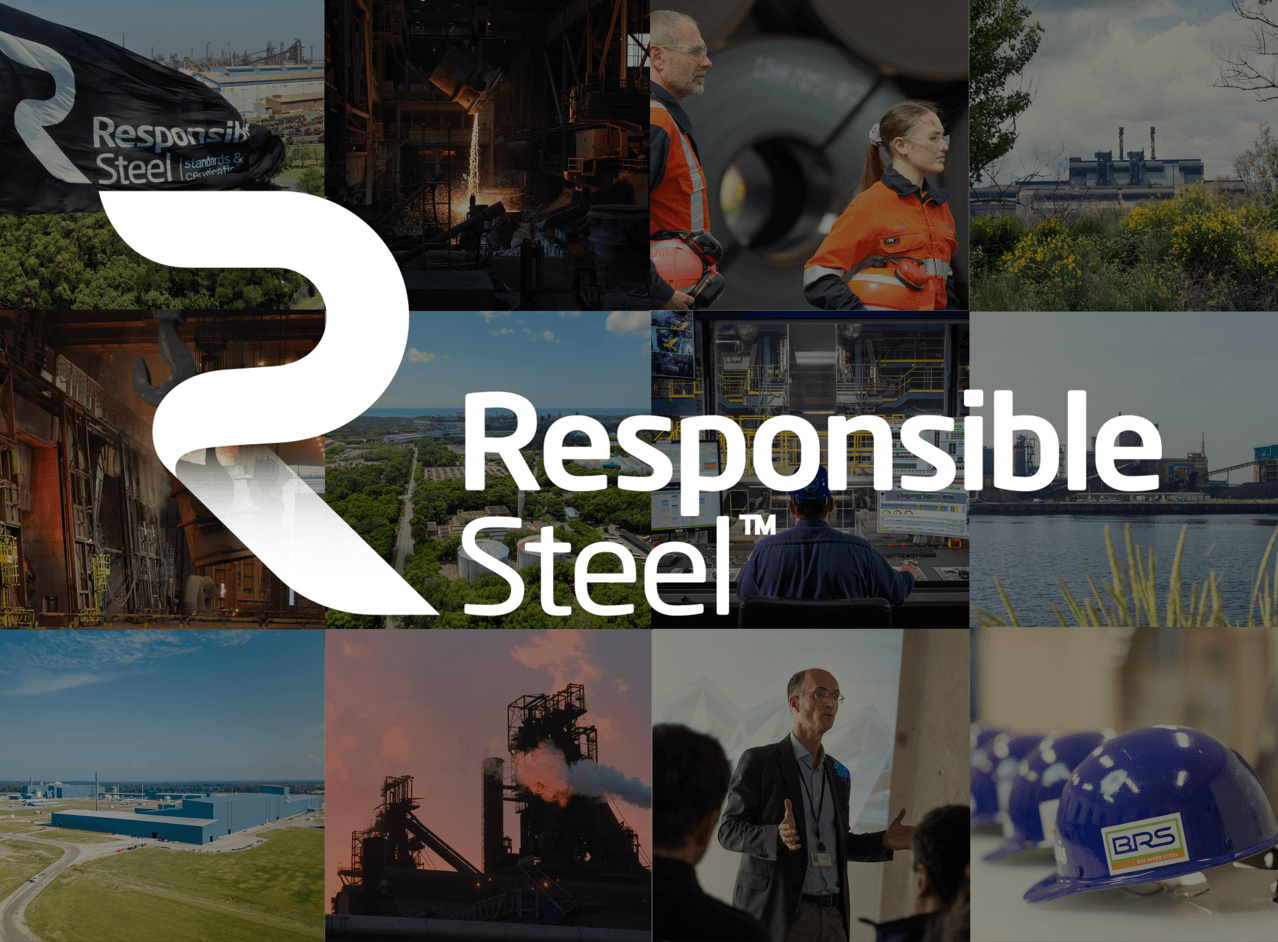
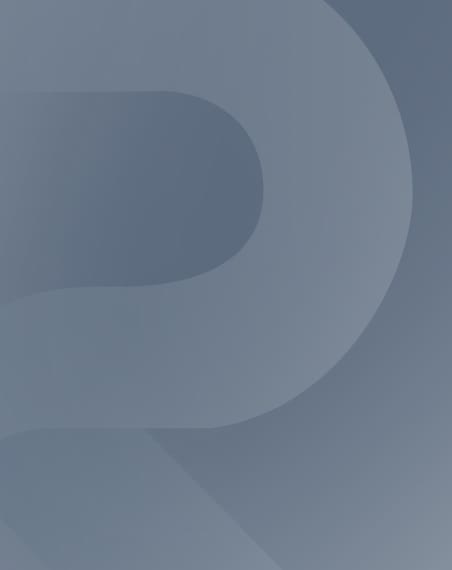
Introducing ResponsibleSteel’s Decarbonisation Progress Audit Tool
To support steelmaking sites in preparing for external audits against Principle 10 of the ResponsibleSteel International Standard V2.0, ResponsibleSteel has now issued a ‘Decarbonisation Progress Audit Tool’.
Designed specifically to support the determination of a steelmaking site’s Progress Level according to criteria 10.6 of the Standard, the tool consists of a series of templates in which the necessary data can be input to calculate the site’s Embodied Crude Steel GHG Emissions Intensity and % scrap in relation to criteria 10.4. As a result of these two calculations, made correctly, a site will be able to see which Progress level they would meet before seeking an external audit.
As well as being used by steel sites self-evaluating their emissions in preparation for an independent ResponsibleSteel Progress audit, the tool can also be used at the pre-production stage by project developers wanting to self-assess their emissions projections ahead of external validation. The Decarbonisation Progress Audit Tool is available to:
- ResponsibleSteel members
- Steelmakers engaging in the First Movers Coalition Near-Zero Steel 2030 Challenge
Steelmakers using the tool will be able to get a clear idea of where they stand on the road to near-zero steel using ResponsibleSteel’s Progress Levels. However, they won’t be able to claim that their sites have achieved ResponsibleSteel Progress Level certification until they have been through an audit against the ResponsibleSteel International Standard and awarded such a certificate by a ResponsibleSteel-approved Certification Body. Any such claims will have to be in line with ResponsibleSteel Claims Guidance.
If you have any questions about the Decarbonisation Progress Audit Tool and how to use it, please contact assurance@responsiblesteel.org. If you would like to receive the tool, please register your interest here.
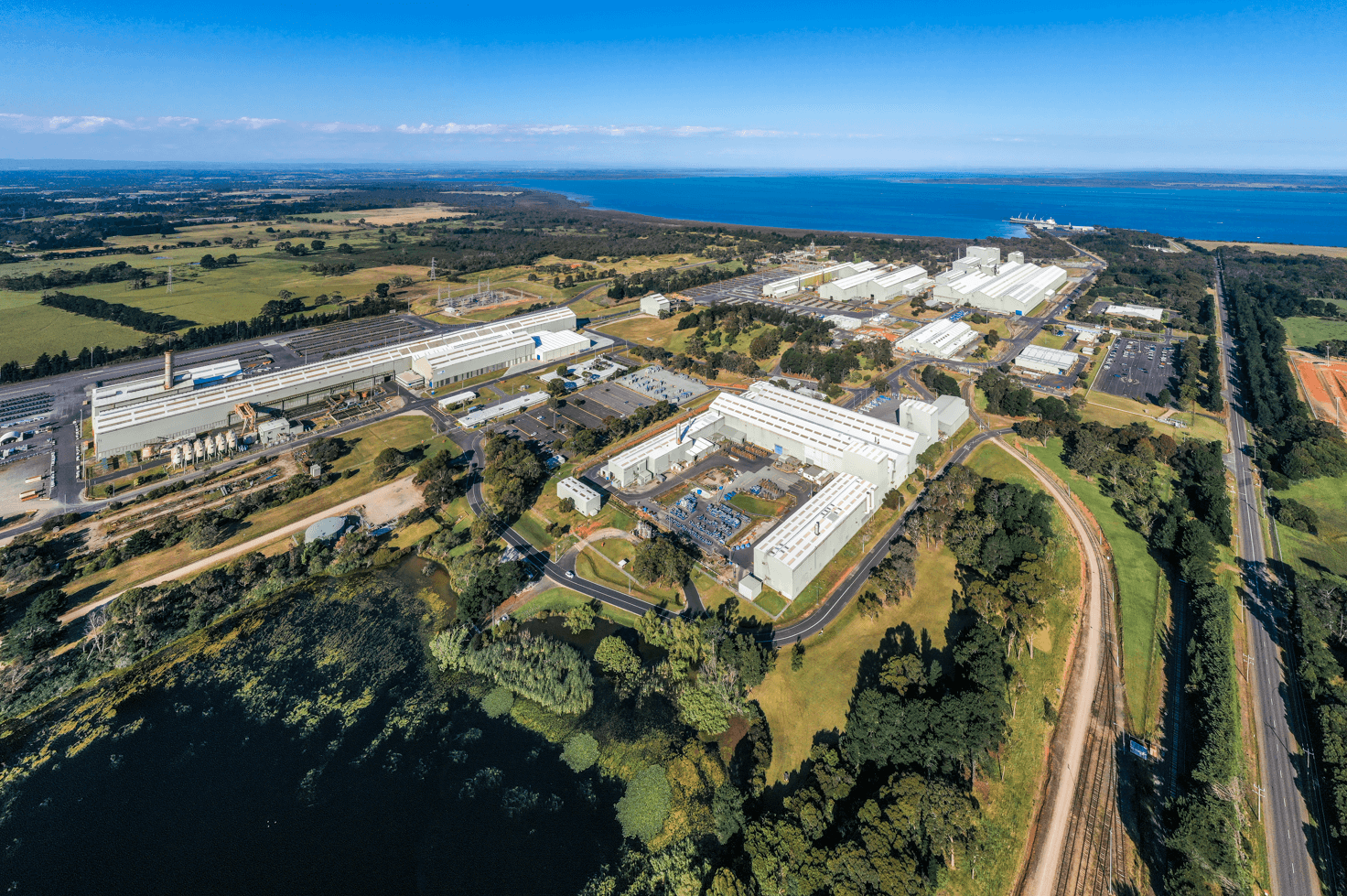
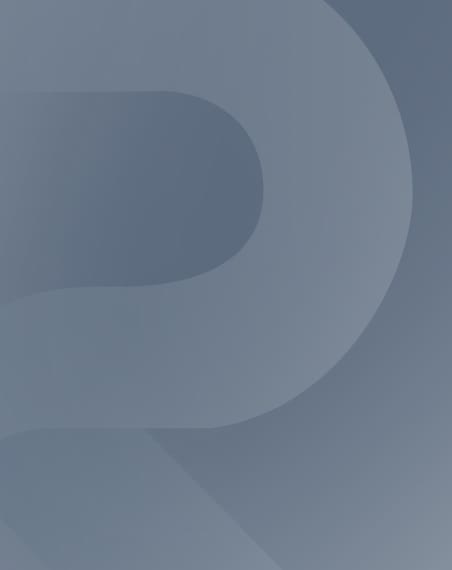
BlueScope’s Western Port Site Achieves ResponsibleSteel Certification
BlueScope has achieved its second ResponsibleSteel certification for its Western Port site in Victoria, Australia. BlueScope’s first certification was obtained by the company’s Port Kembla Steelworks in February 2022.
Western Port is part of a fully integrated steel supply chain with hot rolled coil sourced from BlueScope’s Port Kembla Steelworks. The Western Port site has an annual steel processing capacity of 1 million tonnes, supplying high-quality metal-coated and painted products to both domestic and export markets. The site employs over 800 people who are supported by approximately 100 contractors, suppliers, and supply chain partners.
Commenting on the site certification, BlueScope’s Chief Executive, Australian Steel Products, Tania Archibald, said, “BlueScope is proud to achieve ResponsibleSteel site certification for Western Port. The certification reflects the outstanding efforts of our Western Port team, the quality of our operations, and provides our customers, shareholders, and communities with the confidence that BlueScope’s Western Port Works meets the very high environmental, social and governance performance standards required by ResponsibleSteel site certification. Through the audit process across all 12 sustainability principles, our approach to engaging with our communities, as well as our safety, supply chain, and human resource systems, were highlighted as areas of particularly high performance.”
BlueScope is a global steelmaker, making and supplying steel across 16 countries, employing 16,500 people. The company specialises in metal coating and painting for building and construction.
Annie Heaton, CEO of ResponsibleSteel, said, “This certification is a real testament to the hard work and dedication demonstrated by the site’s leadership and all of the site’s workers. The site has committed to a 30% reduction in emissions intensity by 2030 and has worked diligently to minimise its impact on the surrounding environment. The Western Port site has proven particularly strong in engaging and supporting local communities through Community Liaison Committee meetings and local projects. As one of the founding members of ResponsibleSteel, BlueScope has consistently championed our Standard as the most rigorous standard for steel. This second site certification for BlueScope represents real progress in the company’s sustainability journey and is a vital step towards the sourcing of responsibly produced steel products by the construction industry in Australia.”
The audit was conducted by BSI and involved an extensive review of documentation and news relating to the site, interviews with workers and local stakeholders, and an onsite visit.
BlueScope’s Chief Executive Climate Change & Sustainability, Gretta Stephens emphasised the importance of a multi-stakeholder approach to drive transparency and performance across the steel industry: “ResponsibleSteel site certification is an important step in supporting our stakeholder’s expectations for clear and transparent information about the sustainability performance of our operations. BlueScope’s commitment to sustainability across our global operations will continue to guide our ResponsibleSteel journey, as we strengthen our communities for the future.”
Read the public audit summary here.
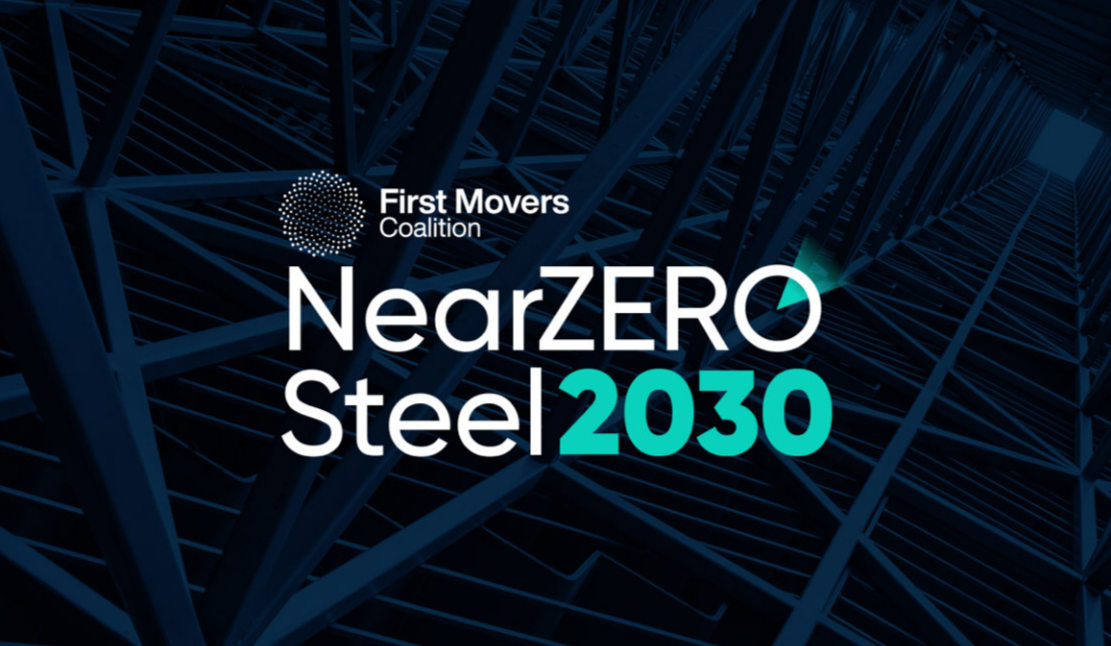
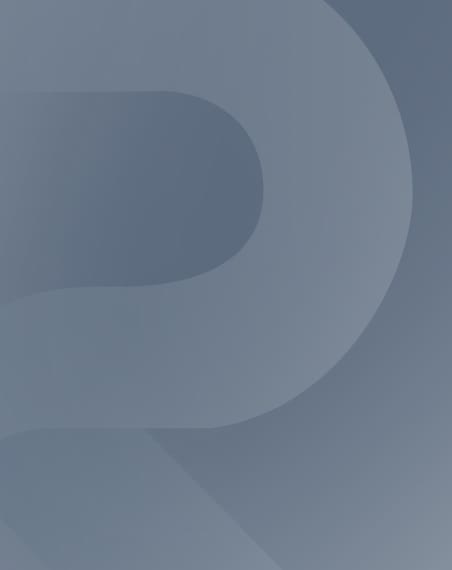
September 2023 Newsletter
Please view the September 2023 newsletter by clicking the link below:
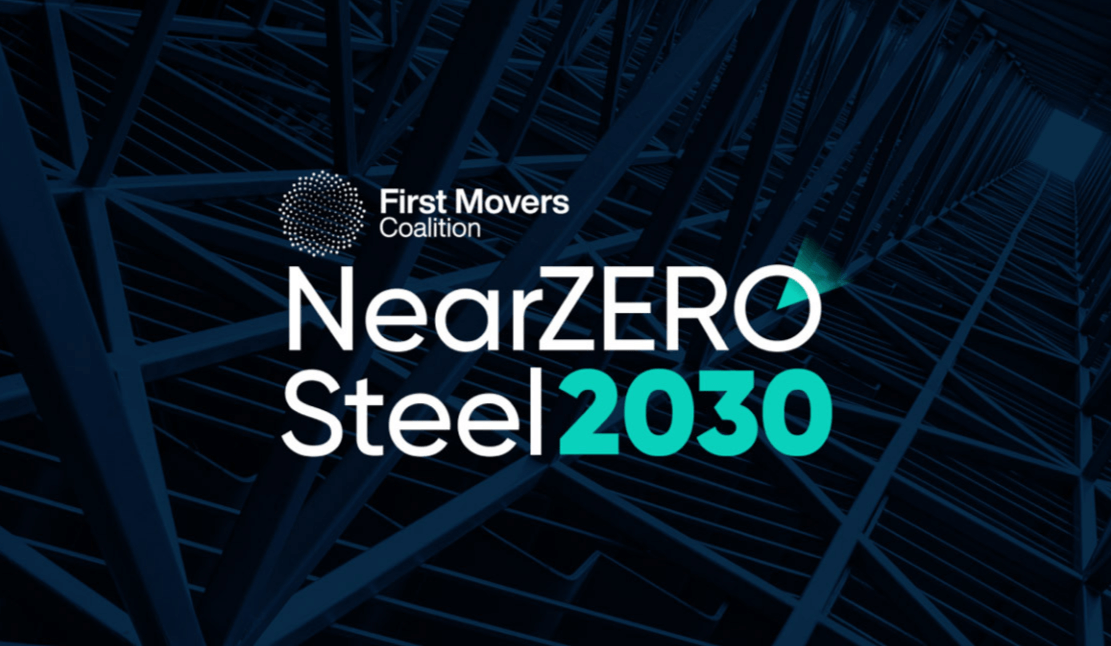
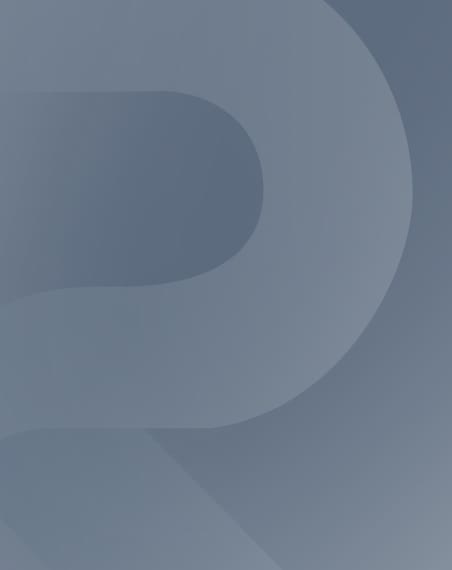
The Near-Zero Steel 2030 Challenge Launches At New York Climate Week
Last week at New York Climate Week, the World Economic Forum’s First Movers Coalition (FMC) together with RMI launched the Near-Zero Steel 2030 Challenge in collaboration with ResponsibleSteel, Greenhouse, Deloitte and BCG. The Challenge will run until December 2023 and will map existing plans, accelerate emerging solutions, and connect potential suppliers of near-zero-emissions steel to companies ready to purchase it.
What is the Near-Zero Steel 2030 Challenge?
Steelmakers need to see demand for near-zero steel to create a business case for new technology. To accelerate the production of near-zero steel, the Challenge will focus on three key areas: driving near-zero emissions steel solutions; enabling emerging technology solutions such as CCUS, green hydrogen, and direct electrolysis; and sending demand signals for near-zero steel, particularly from automotive, construction, infrastructure, and consumer goods sectors.
The FMC was established at COP26 to decarbonise seven hard-to-abate sectors currently accounting for around 30% of global emissions by using the purchasing power of its members to send a clear demand signal and by driving the uptake of new technologies on a commercial scale. FMC steel members, who include Orsted, Ford and Trane Technologies, commit to buying at least 10% near-zero steel by 2030. Alongside the Challenge, the FMC is developing a Supplier Database to map potential near-zero steel projects. In tandem, RMI has established a Sustainable Steel Buyers Platform for the procurement of near-zero steel in North America. In New York in September, RMI launched a Request For Information (RFI) which will be followed by a buyers-led Request For Proposal (RFP). The RFP will incorporate willing Near-Zero Steel Supply Challenge participants in North America in a process that will result in a collective request for up to 2 million tons of near-zero emissions steel with the goal being bilateral offtake agreements.
What is ResponsibleSteel’s role in the Challenge?
ResponsibleSteel is part of a wider ecosystem working to decarbonise the steel industry. Working collaboratively to drive alignment on carbon accounting and claims is a vital component to facilitate the credibility of near-zero steel projects. We need rules to define and measure near-zero steel to ensure everyone is pulling in the same direction as quickly and efficiently as possible. Our work with the FMC demonstrates that there is already an international definition of near-zero steel that is backed by a practical methodology. Certification against the ResponsibleSteel International Standard facilitates the financing, purchasing, labelling and trade of credibly labelled near-zero steel.
ResponsibleSteel provides the standard for how to measure near-zero steel. The Challenge will leverage our International Standard’s Decarbonisation Progress Level 4 by asking steelmaking sites to assess their projected emissions against this near-zero steel benchmark using the Standard’s Criteria 10.4 and 10.6: Climate Change and Greenhouse Gas Emissions. A toolkit will be available for steelmaking sites to undergo third-party pre-production assessment in 2024.
How can my company get involved in the Challenge?
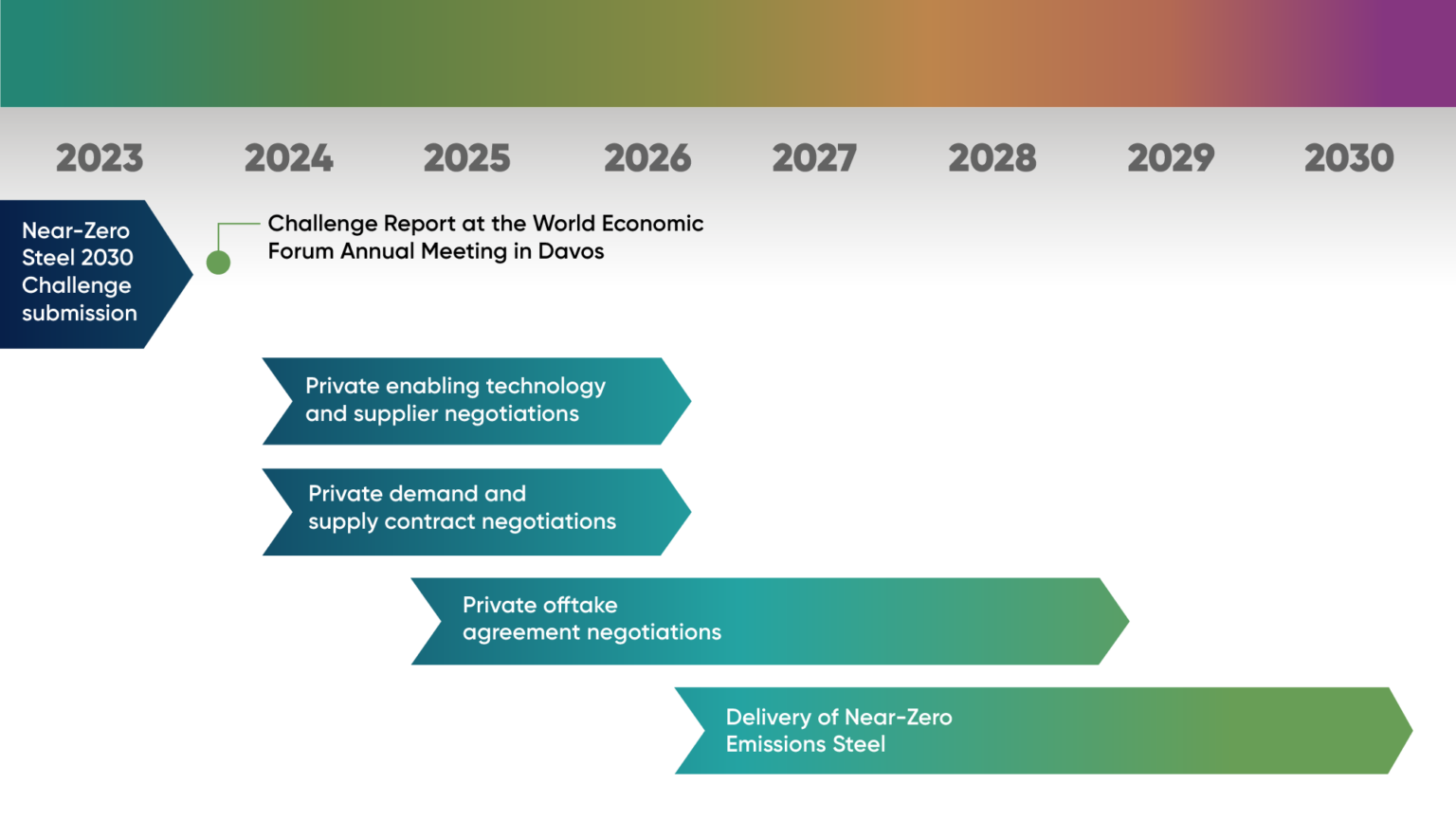
Multistakeholder collaboration is a key aspect of the Near-Zero Steel 2030 Challenge and success will require input from across the steel value chain, government, civil society, technology suppliers, and funding bodies. Companies interested in participating in the Challenge can submit Expressions of Interest this year and from 2024, the Challenge will work to connect suppliers with emerging decarbonisation technologies and buyers with future suppliers of near-zero steel.
Learn more about the Near-Zero Steel 2030 Challenge here.
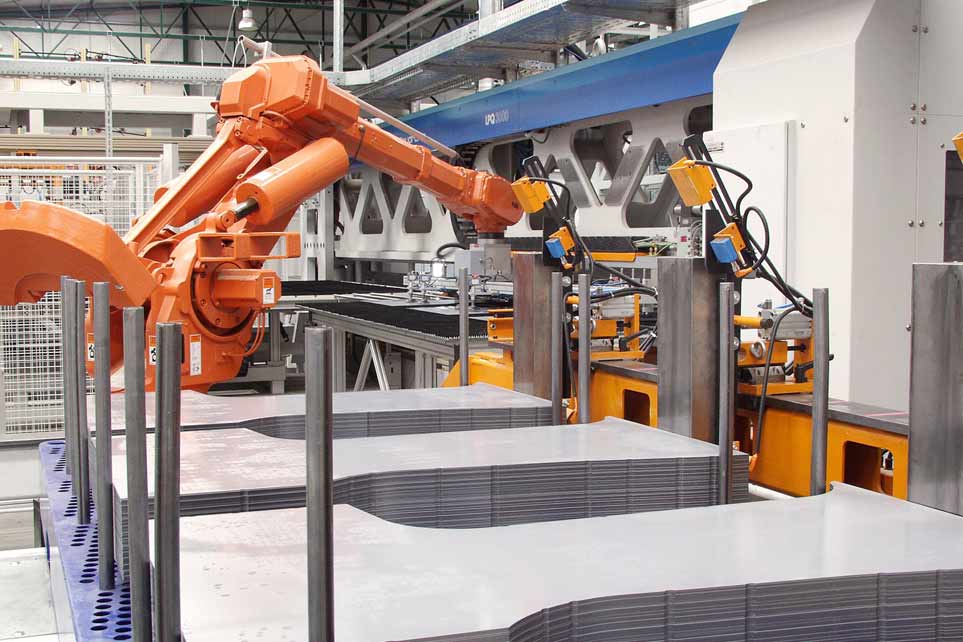
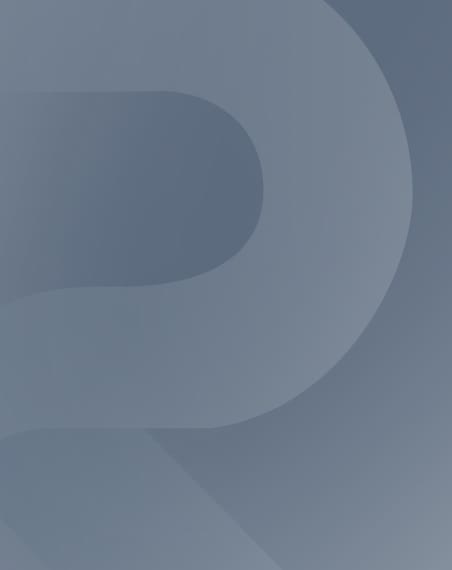
ArcelorMittal Tailored Blanks Zaragoza Earns ResponsibleSteel Certification
The site is ArcelorMittal’s fifth in Spain to become certified against the ResponsibleSteel International Standard, following the certification of sites forming the Asturias Cluster (Avilés and Gijón, Sagunto, Etxebarri and Lesaka) in 2022.
Located in the Pradillo II industrial area in Pedrola, 30 km from the capital of Aragón, ArcelorMittal Tailored Blanks Zaragoza is right in the centre of Spain’s automotive industry. The site is part of ArcelorMittal Europe’s Flat Products segment and receives galvanised steel coils from European sites which it processes to produce laser-welded blanks for the automotive industry. This technology provides a reduction in the weight of the vehicles, resulting in lower fuel consumption, while also enhancing safety for the users. In 2022, shipments amounted to a total of 5.2 million parts, with shipment volumes expected to rise to over 6 million parts this year.
ResponsibleSteel’s CEO, Annie Heaton commented, “This is an important step as we work to build a responsible steel value chain. ArcelorMittal Zaragoza’s galvanised steel coils come largely from existing ResponsibleSteel certified sites across France, Spain and Germany. So this certification is a real milestone for ResponsibleSteel, getting us one step closer to achieving certification across the value chain and giving Zaragoza’s automotive customers greater confidence that their steel has been produced in a way that respects both people and the planet every step of the way. As ArcelorMittal continues to work to certify sites globally, I look forward to seeing these links of the value chain continue to come together under the ResponsibleSteel programme to assure a full chain of custody from steel furnace to end use.”
The site underwent an independent audit conducted by DNV against Version 1.1 of the Standard. The site’s commitment to the health and safety of its employees and the preservation of local biodiversity were identified as particular strengths during the audit.
The site manager, Tomás Ramos, commented, “As a team, it has been a great satisfaction for us to achieve ResponsibleSteel certification. We were selected as the pilot plant among all the European subsidiaries in the Tailored Blanks division and, after all the efforts deployed, we have been able to deliver on this mandate. This certification would not have been possible without the engagement and professional commitment of all members of the team.”
He continued, “It has undoubtedly been a very interesting exercise and has enabled us to bring together, in a structured way, the complex and diverse range of activities that we have been implementing with our stakeholders. For us, the certification process has been an analytical journey across the Standard’s 12 principles and all its criteria and requirements. This exercise has enabled us to review all our actions and include the latest proposals to support the existing commitment to Sustainability, good Governance and the Health and Safety of all the parties involved in this project, which, ultimately, will ensure that the good results are shared by all.”
Read the public audit summary here.
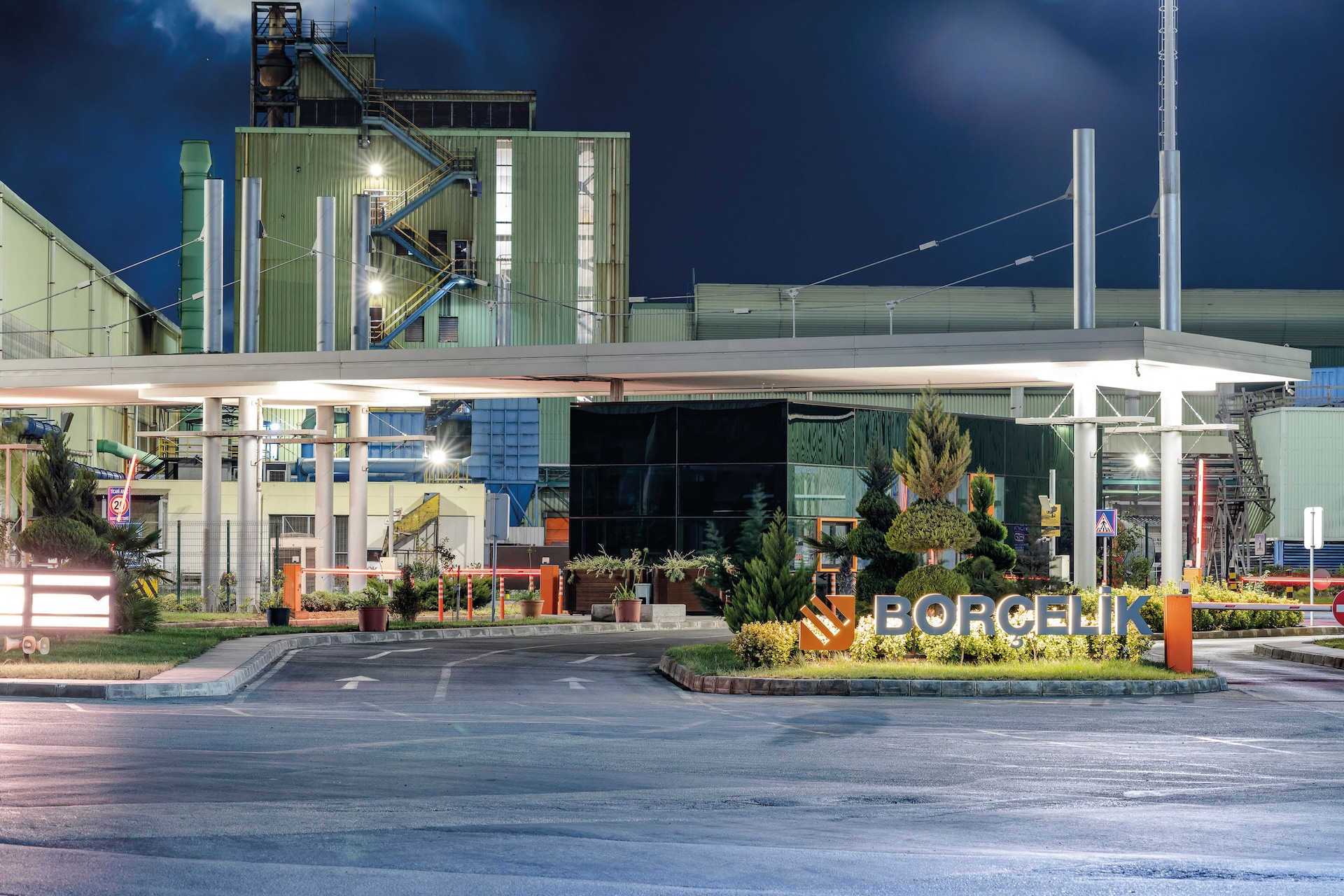
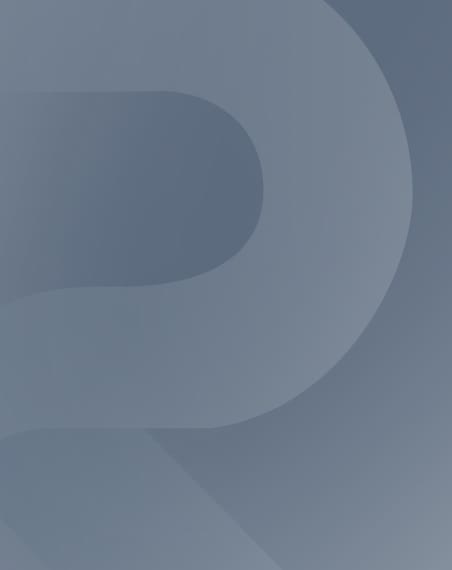
Borçelik Gemlik Becomes First ResponsibleSteel Certified Site In Turkey
Borçelik’s Gemlik site has become the first in Turkey to become certified against the ResponsibleSteel International Standard. Borçelik, a joint venture of Borusan Holding and ArcelorMittal, is Turkey’s biggest galvanized flat steel producer.
Borçelik became a ResponsibleSteel member in 2020, joining ArcelorMittal and many other of the world’s leading steel producers. ResponsibleSteel currently has around 15% of global steelmaking capacity in membership. The Gemlik site has a production capacity of 1.5 million tonnes and employs over 1000 workers and contractors.
ResponsibleSteel’s CEO, Annie Heaton, commented, “This first ResponsibleSteel certification of a site in Turkey demonstrates Borcelik’s drive to be a leader in the Turkish steel industry, and more importantly, the company’s commitment to implementing the most rigorous criteria for sustainability. On an environmental level, the company has committed to achieving net zero by 2050 and the site already has several energy efficiency projects as well as wind and solar plants in the works to support this journey. The site has gone above and beyond to minimise environmental impacts including setting up its own water stewardship project to monitor water efficiency and prevent future scarcity while on a human level, the site has demonstrated a deep commitment to ensuring workers’ rights and safety and equality in the workplace.”
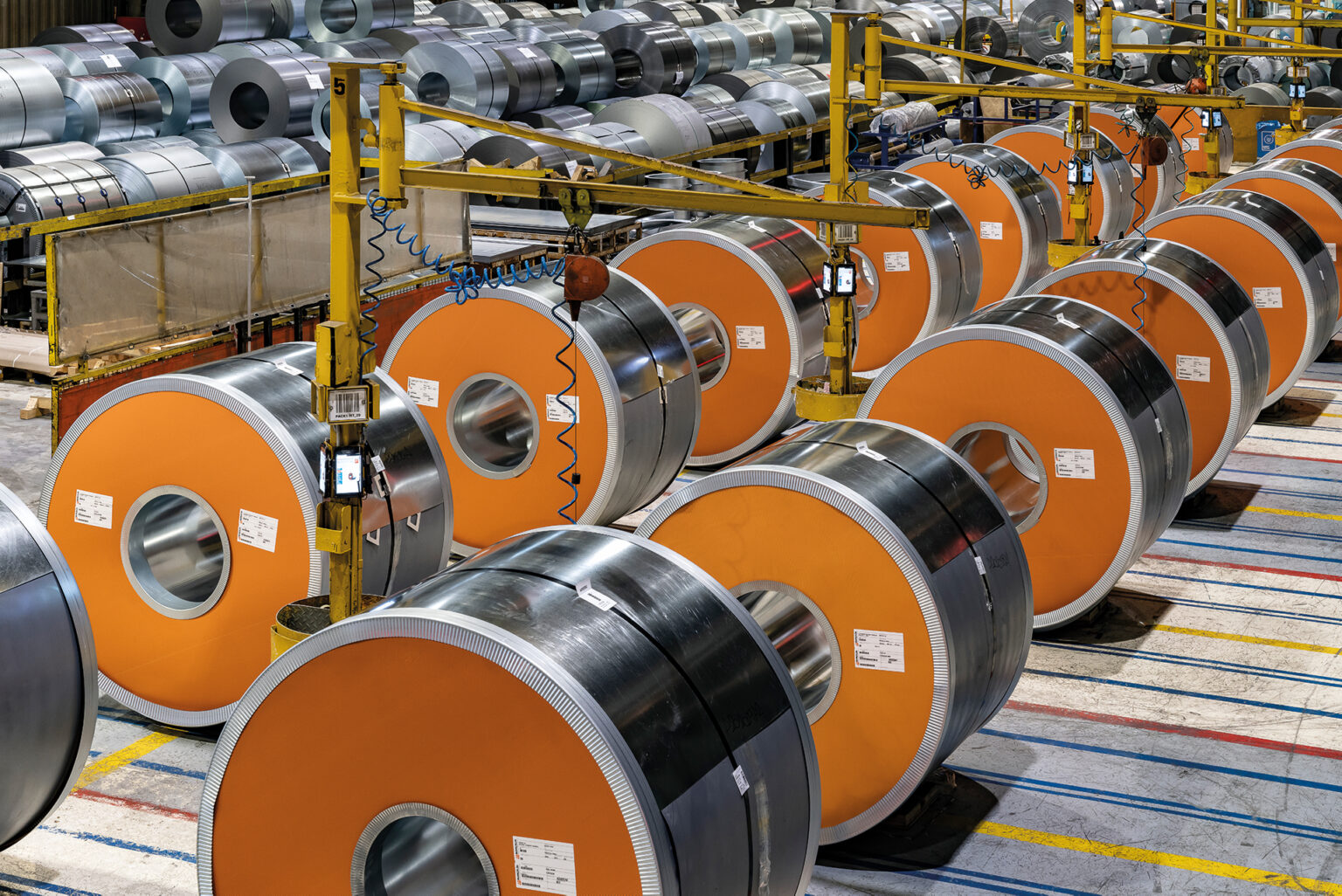
The site achieved certification following an independent audit conducted by CARES against Version 1.1. of the Standard. In addition to the site’s efforts to reduce its environmental impact, the site’s social governance was identified as a particular strength. Throughout the audit, the site repeatedly demonstrated its commitment to worker safety, growth and development.
Kerem Çakır, General Manager of Borçelik, stated that Borçelik has achieved significant progress towards the company’s sustainability goals. Çakır commented, “As one of the leading and pioneering institutions of our industry, we have been committed to sustainability and responsible business practices. We are very proud that the presence of this approach in all our business applications is confirmed with the ResponsibleSteel certification and we have achieved another first in our country with the certificate that we were awarded. As a responsible industry leader, we aim to inspire change in the steel industry and contribute to a more sustainable world in all areas.”
Serkan Ürkmez, Borçelik Sustainability Leader, added, “As Borçelik, we had undergone a very intense preparation period to comply with ResponsibleSteel standards. We worked together with our Sustainability Committee. The standard’s environmental and social expectations are really challenging. After this preliminary stage, we successfully completed a detailed and challenging 14-day audit process conducted by the leading independent audit firm UK CARES. At the end of this process, we are happy to be the first ResponsibleSteel site-certified institution in our country. We will continue to be an exemplary institution in our industry with our activities.”
Take a look at the audit summary here or read the press release here.
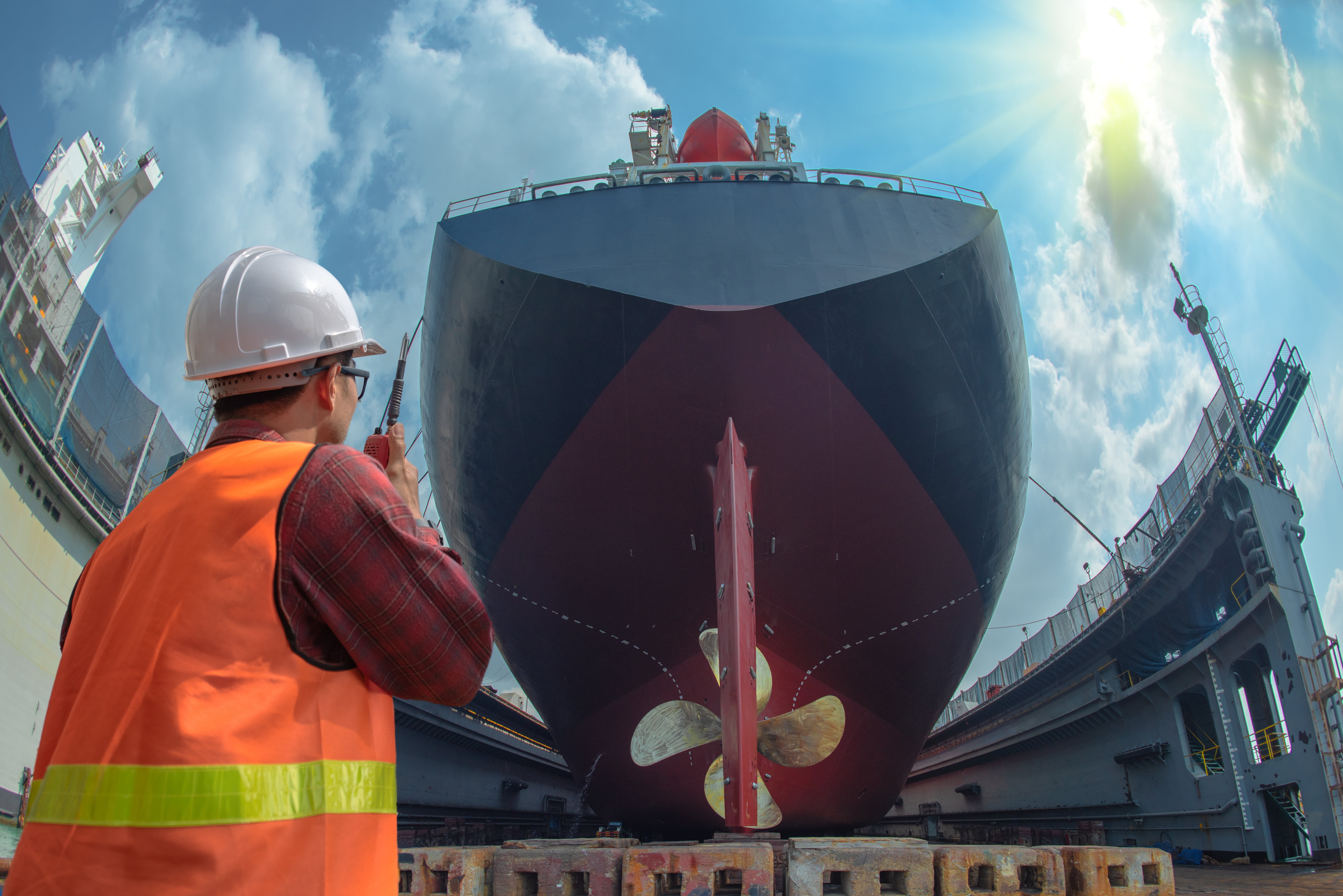
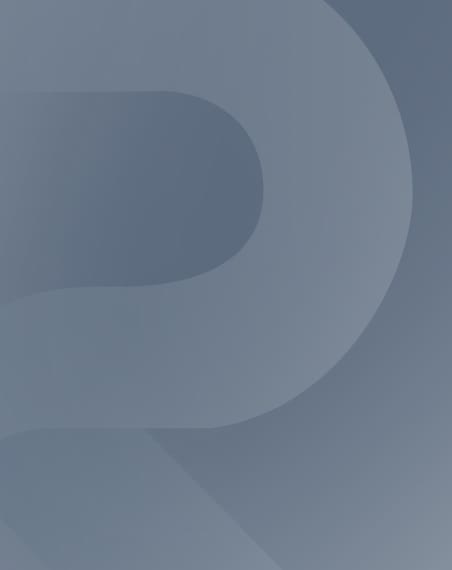
Member webinar: The near-zero steel 2030 challenge
We would like to invite ResponsibleSteel members to join a special webinar we will be hosting on Monday, September 11th at 12:30 pm (BST) with the First Mover’s Coalition (FMC) to give a first look at the upcoming Near-Zero Steel 2030 Challenge.
The Challenge, led by the FMC in collaboration with Greenhouse and with the support of RMI, ResponsibleSteel, Deloitte and BCG, will officially launch at Climate Week in New York next month.
In this webinar members will have the opportunity to hear about the objectives of the Challenge, the three parts that it is composed of, and how it relates to the ResponsibleSteel International Standard.
Representatives from the FMC, Greenhouse, RMI, and ResponsibleSteel will join to give an overview of the Challenge’s process, submission opportunities, and end goals.
This webinar will be a great opportunity for ResponsibleSteel members to have a sneak peek at this exciting project and understand how they can get involved ahead of its public launch.
There will also be a Q&A session following the speaker presentations and ample opportunity for a broad and dynamic discussion with members.
This webinar is open to all members and will be hosted by ResponsibleSteel via Microsoft Teams.
Please contact us if you are interest in joining.
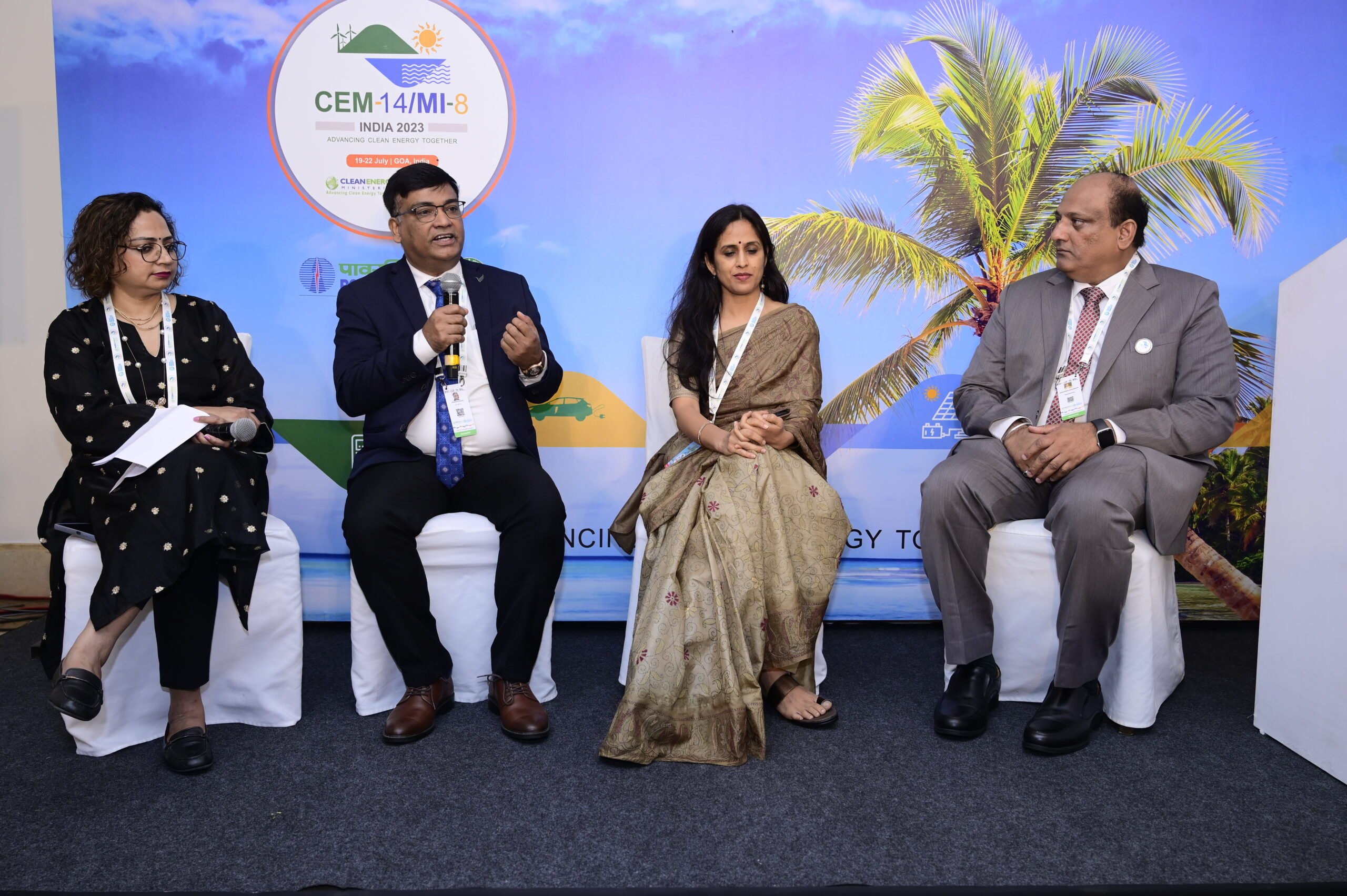
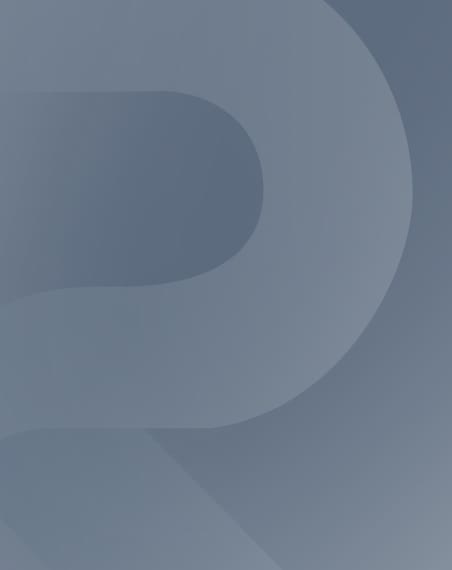
August 2023 Newsletter
Please view the August 2023 newsletter by clicking the link below:
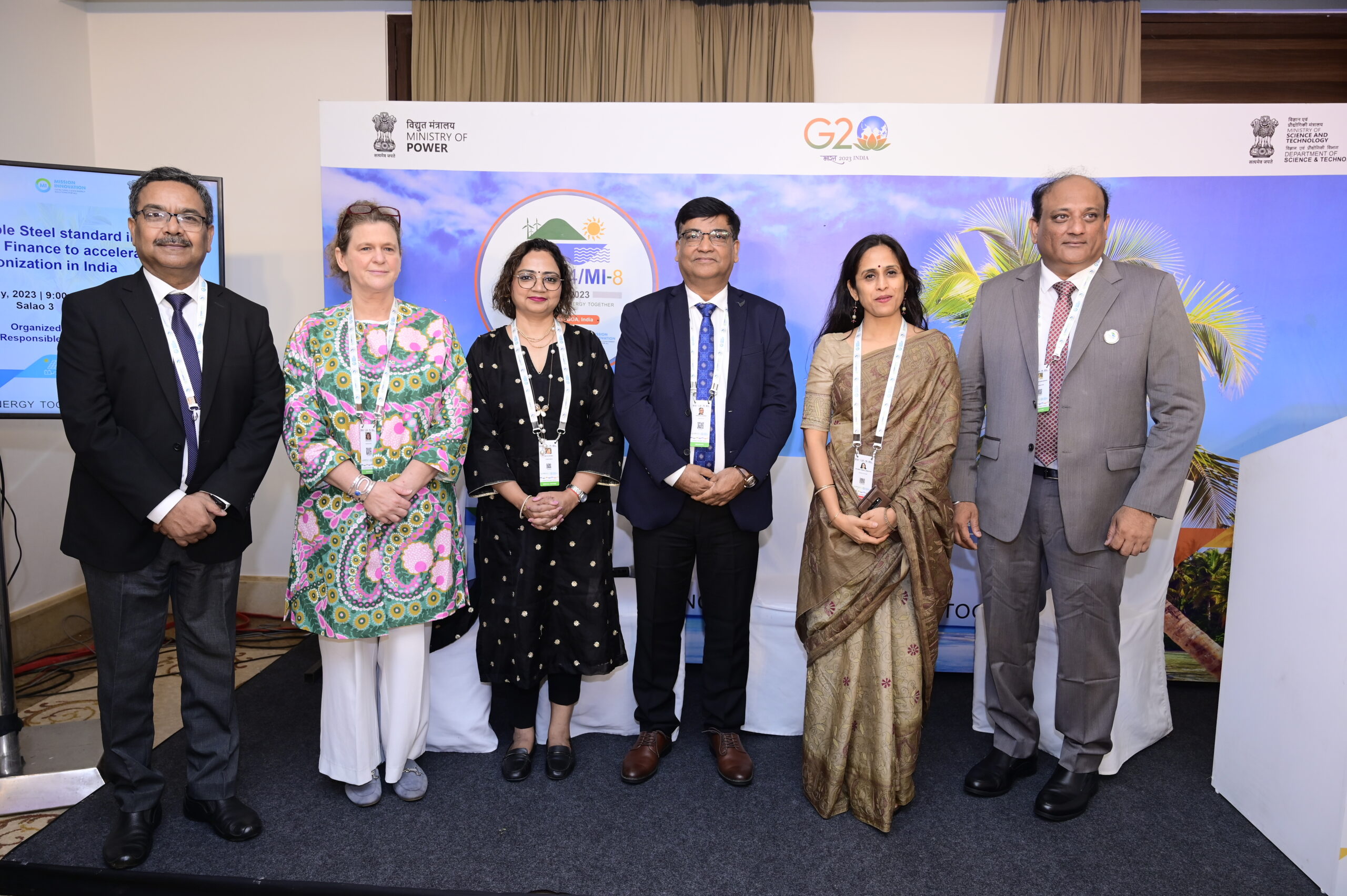
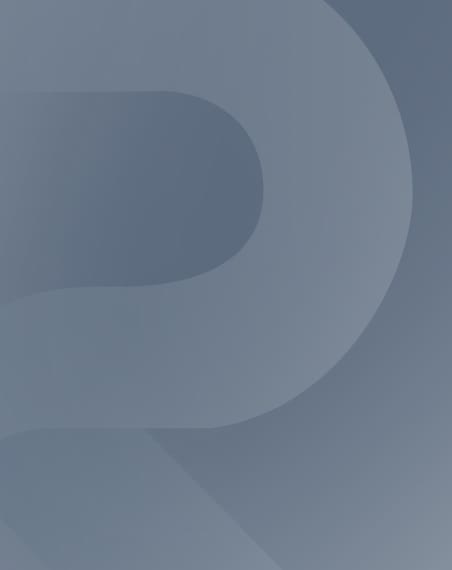
Accelerating Decarbonisation in India’s Steel Industry: The Challenges, the Tools and the Solutions
Now the most populous country in the world, India is also the second-largest producer of steel after China. According to the IEA, the Indian steel industry is projected to triple by 2050, making it the fastest-growing steel economy globally (IEA, Iron and Steel Technology Roadmap, 2020). The majority of India’s steel is used for domestic consumption – for infrastructure, transport, construction and consumer goods. Whether in airports or railway stations, steel use is increasing across India, and meanwhile, the expansion of renewable energy in the country, which also requires vast amounts of steel, is racing ahead at breakneck speed. This unprecedented growth in steel consumption is a vital part of India’s economic story.
But the steel industry also accounts for around 12% of India’s emissions, far more than the global average of 8%. So the country’s push to meet its net zero target by 2070 will rely heavily on the decarbonisation of its steel sector. Currently, almost half of Indian steel is produced via the traditional blast furnace route with the remaining being split between smaller less efficient induction furnaces and electric arc furnaces. Enormous efforts to decarbonise are already being made. Since 2005, emissions per tonne of crude steel in India have been reduced from around 3.1 tonnes to 2.5 tonnes. But the sheer amount of resources needed to accelerate decarbonisation remains huge.
There are many challenges. The lack of a transition fuel such as natural gas to accelerate the phase-out of coal is a significant issue. What is more, the use of the lower-grade iron ore found in India requires more energy for reduction. And while countries with long histories of producing and consuming steel – and all the associated emissions – now have the luxury of large stocks of scrap, India’s access to scrap is extremely limited today. A far more comprehensive plan is needed to reimagine the entire industry.
Deep thinking on the solutions is clearly happening within government. The Indian Ministry of Steel recently set up 13 task forces to investigate the policies needed to tackle the decarbonisation challenge from multiple angles: to improve energy and material efficiency, to enable the transition to renewable energies, to price carbon emissions, to stimulate green finance and, underpinning all these, to define the embodied emissions of steel.
Major steel companies are working to decarbonise at pace. Jindal Steel and Power has already committed to net zero by 2047, Tata Steel by 2045, and JSW by 2050. All of these are well ahead of the national 2070 target. But these ambitious targets require equally ambitious and comprehensive decarbonisation plans which will also accommodate rapidly expanding demand. To accommodate the steel growth foreseen in the Indian economy, the government is projecting a doubling in steel capacity by 2030, and much of the planning for this so far is via the traditionally emissions-heavy blast furnace route. Herein lies the challenge. Such companies will need to demonstrate how their new blast furnace investments can align with their net-zero targets. Investors are increasingly looking for transition roadmaps.
Whilst Indian steel companies may understand the technologies needed to reduce emissions, the processes are vastly more expensive, and so they need to see a clear business case: signals that their customers are ready to pay the premium on lower-emissions steel; facilitative policies from government to reduce costs and market incentivisation for technologies available in the near term; an effective price on carbon; preferential finance for decarbonisation projects. Such measures may all form part of steel company roadmaps to net zero.
Last month, as part of the 14th Clean Energy Ministerial in Goa, ResponsibleSteel brought together key stakeholders from the steel industry, downstream market, and government to discuss the role of the ResponsibleSteel International Standard in impacting policy, finance and the energy transition to accelerate decarbonisation in India’s steel industry at pace and scale. The event featured keynotes from the Secretary to the Ministry of Steel, the Secretary General and Executive Head of the Indian Steel Association, and ResponsibleSteel’s CEO. ResponsibleSteel also hosted a panel discussion on the challenges and solutions needed to achieve an equitable and just transition between representatives from the Ministry of Steel, JSW Steel and SteelZero. What’s clear is that to accelerate decarbonisation in India at scale and at speed, we need to share learning and build skills, not only to maximise scrap recovery but to drive demand and finance for low-emissions primary steelmaking on a vast scale.
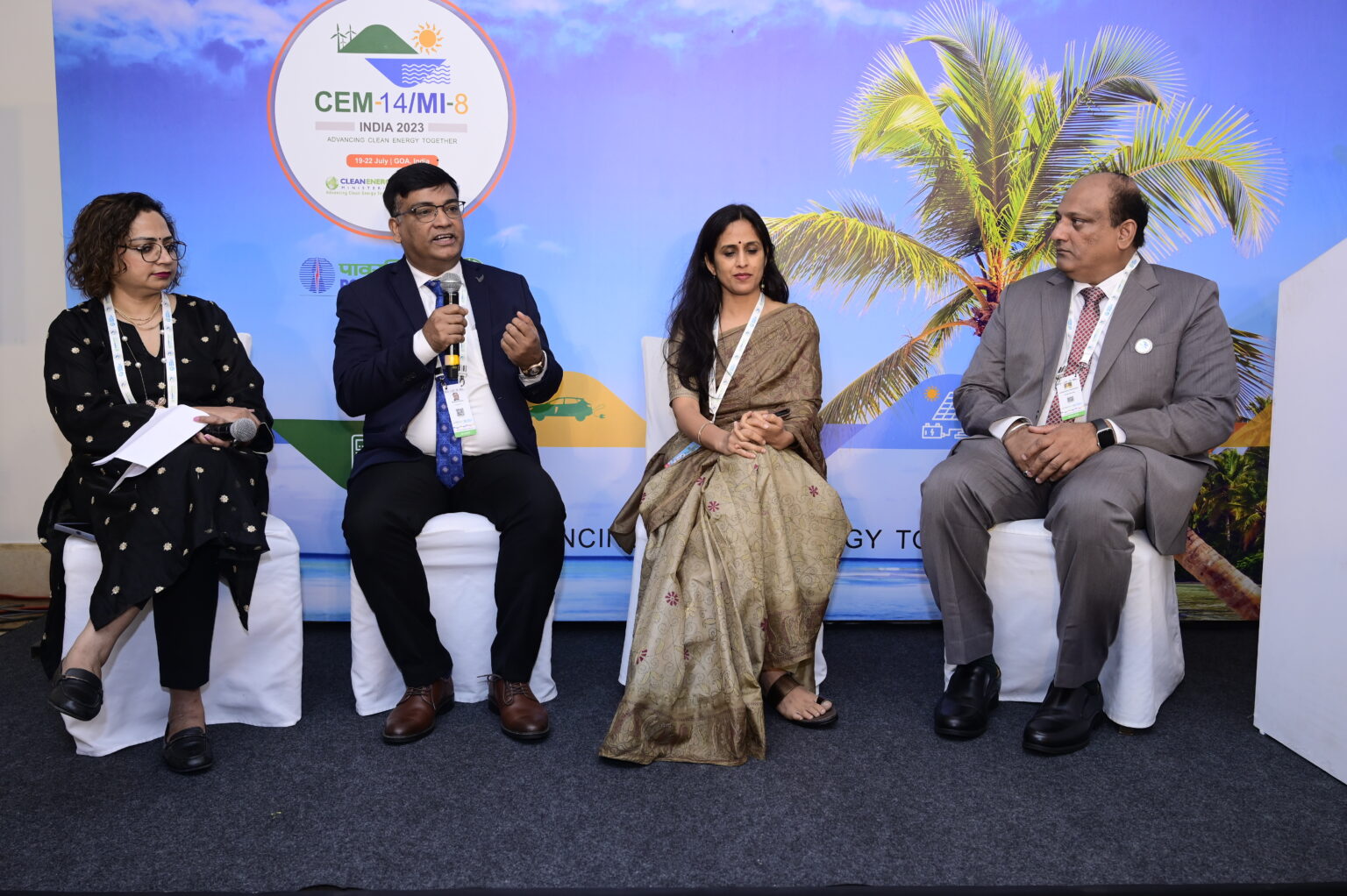
This means clean energy at scale. India has already made rapid progress on renewable electricity, reaching a capacity of 168 GW in the last ten years. The Indian government has targeted 50% renewable electricity by 2030, with an unparalleled 50GW a year in the pipeline over the next five years – more than the US or Europe installed in 2022. There is also a lot of talk on green hydrogen. The Indian government aims to have 5 million tonnes by 2030. Both the achievements to date and the plans ahead are inspiring examples of ambitious government strategy.
But whilst renewable energy is core to the decarbonisation roadmap for steelmaking in India, the shift to green hydrogen in India is complex due to the limited reserves of natural gas as a transition fuel. In the meantime, alternative ways of thinking are emerging to avoid a costly wholesale switch to H2 based DRI before green hydrogen is available. Tata Steel has recently demonstrated the 24/7 injection of hydrogen in the blast furnace as a reductant and believes this could deliver a 15% to 20% reduction in CO2 emissions. With additional capital expenditure, the potential is as much as 30% or, some say, even more.
The industry has also shown promising progress on carbon capture from coal used in the blast furnace as an intermediate technology that can divert vast volumes of carbon emissions and produce methanol. Currently, pilots are demonstrating the potential to deliver 15-20% emissions reduction, with the potential thought to be higher. At present, however, the costs involved prevent it from being scaled as a viable source of methanol. Improving efficiencies in the processing of input materials is another element under development, with innovations emerging to enable lower-grade iron ores to be used directly for reduction without need for sintering, for example.
Efforts to maximise the use of scrap are also underway. JSW and Tata Steel have invested in scrap collection after policies were introduced in recent years to mandate the end-of-life recycling of vehicles and facilitate the growth of metal scrapping centres in India.
Finally, development of carbon capture and storage technology is hampered by high costs, a lack of market incentives and a lack of concerted research and development. The potential for CCS in India has been subject to geological uncertainties, and yet the outlook may be more promising than once thought. For instance, basalts can mineralise captured carbon for effective and permanent storage. A recent study showed India has one of the largest onshore basalt formations in the world, and around 360GW CCS capacity in both basalts and deep saline formations, excluding no-go and densely populated areas (CEEW, 2023). Meanwhile, India’s annual emissions today are just over 3GW.
But underpinning all of this is the need for a common language for steel decarbonisation within countries and between countries. We need a consistent method of measuring and defining near-zero steel that is effective in driving down emissions globally. As Shri Nagendra Nath Sinha, Secretary for the Indian Ministry of Steel, stated, “It has to be clear, it has to be credible and it has to be standardised.” This is why ResponsibleSteel’s work is so critical. For Prabodha Acharya, JSW’s Chief Sustainability Officer, “Many customers are asking about green steel, and I don’t know what they mean by green steel, but when they ask for ResponsibleSteel we have a definitive standard… This is going to be the gold standard.”
It also has to be equitable. The ResponsibleSteel International Standard takes the approach of a ‘scrap variable scale’ to define decarbonisation progress levels. To incentivize decarbonisation in a way that is both effective and fair globally, not only in countries with the luxury of high scrap stocks. To avoid a commercial ‘race for scrap’ with no net gain for the climate, rather than encouraging the decarbonisation of steel production across the board and particularly from iron ore. To drive the entire global industry to net zero.
As ResponsibleSteel’s CEO Annie Heaton remarked, “We need to rise above the interests of individual companies, of individual countries, and individual technologies to drive decarbonisation at a global level.” Shri Alok Sahay, Secretary General & Executive Head of the Indian Steel Association, believes ResponsibleSteel plays a vital role in creating a more equitable system. “To decarbonise, it’s vital that we foster partnerships. ResponsibleSteel can bring everyone together, and help build a level playing field.”
You can watch a recording of ResponsibleSteel’s event at the Clean Energy Ministerial here.
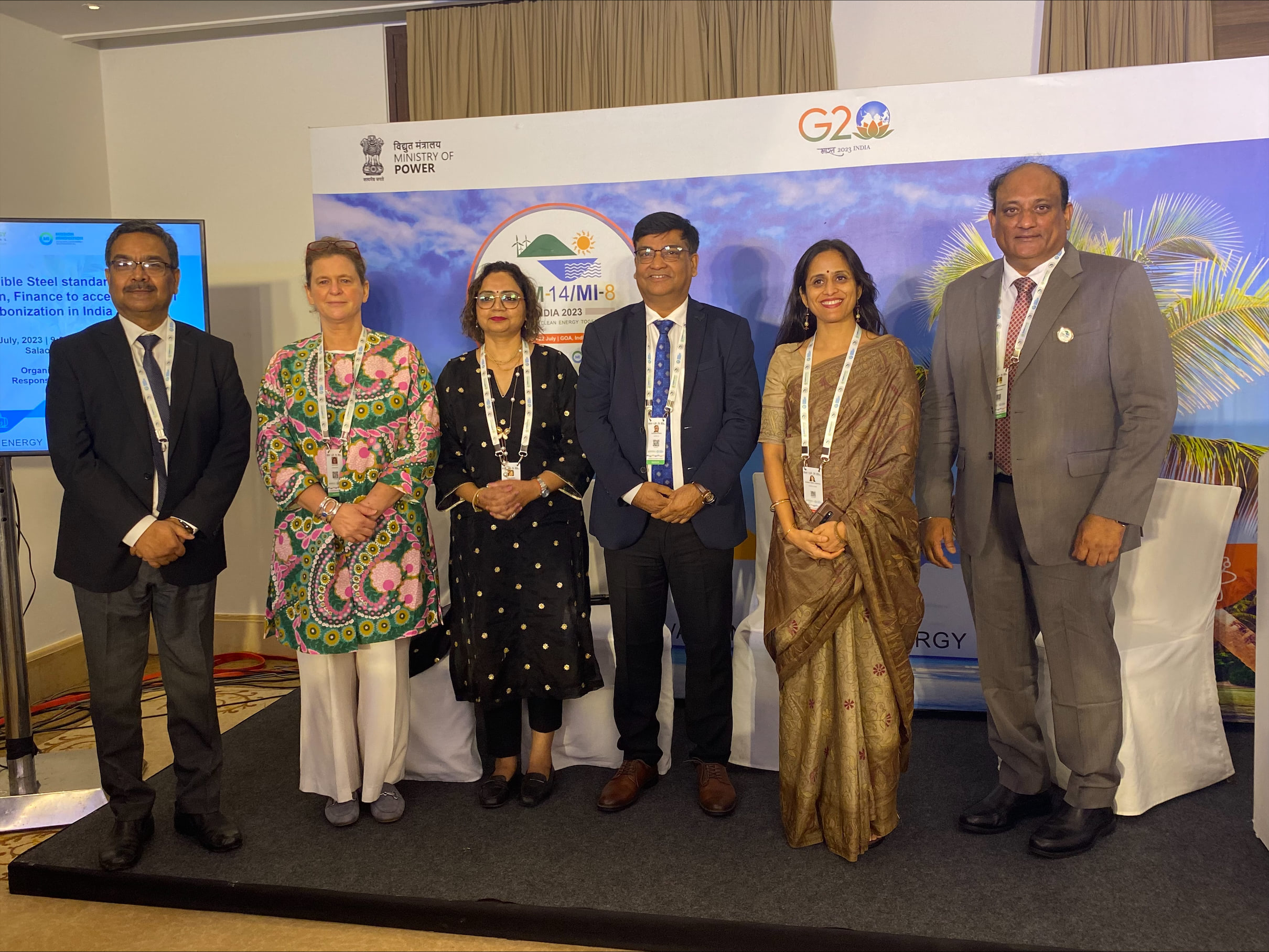
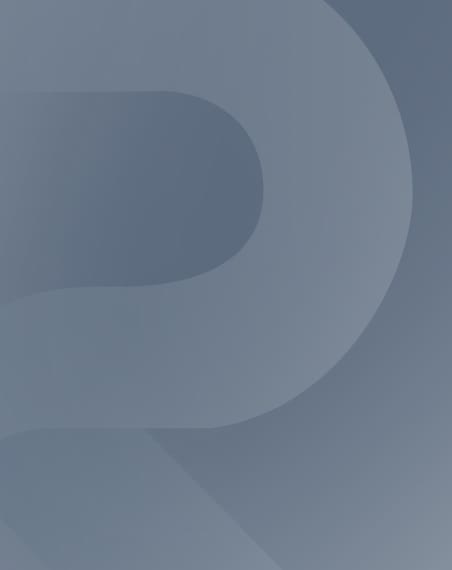
July 2023 Newsletter
Please view the July 2023 newsletter by clicking the link below:
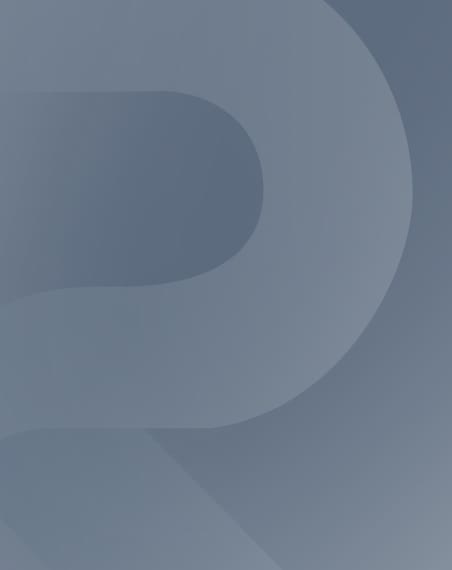
ResponsibleSteel in India: The First Movers Coalition In-Country Workshop, Surfacing Supply of Near-Zero Emission Steel
India is the world’s second-largest steel producer. The steel industry accounts for around 12% of India’s emissions and steel production is set to grow rapidly. This month ResponsibleSteel is in India to dive into the particular dynamics of the challenges in a country where the population uses one-third of the global average steel consumption per head.
As part of the Steel Breakthrough Agenda, we have been working with the First Movers Coalition to drive alignment and accelerate steel decarbonisation. The First Movers Coalition aims to pull forward the deployment of clean and deeply decarbonising technologies through its members’ commitments to procure 10% from near-zero sources by 2030.
We were delighted to participate in last week’s First Movers Coalition’s In-Country Workshop: Surfacing Supply of Near-Zero Emission Steel in New Delhi.
Our CEO, Annie Heaton, spoke about the practicalities of activating these commitments in the Indian context. Steel production is set to double by 2030. The challenge is immense. The major Indian steel companies are investing in technology innovation. Yet the conditions are not in place to accelerate deployment of decarbonisation projects.
Consolidated demand-side signals, reduced-cost finance, and ambitious and accelerated policy levers are all needed. But as Annie explained, “above all, a common carbon measurement standard and definition of near zero steel is needed to ensure these all work together.” The ResponsibleSteel International Standard has the potential to provide such a framework to drive equitable steel decarbonisation globally.
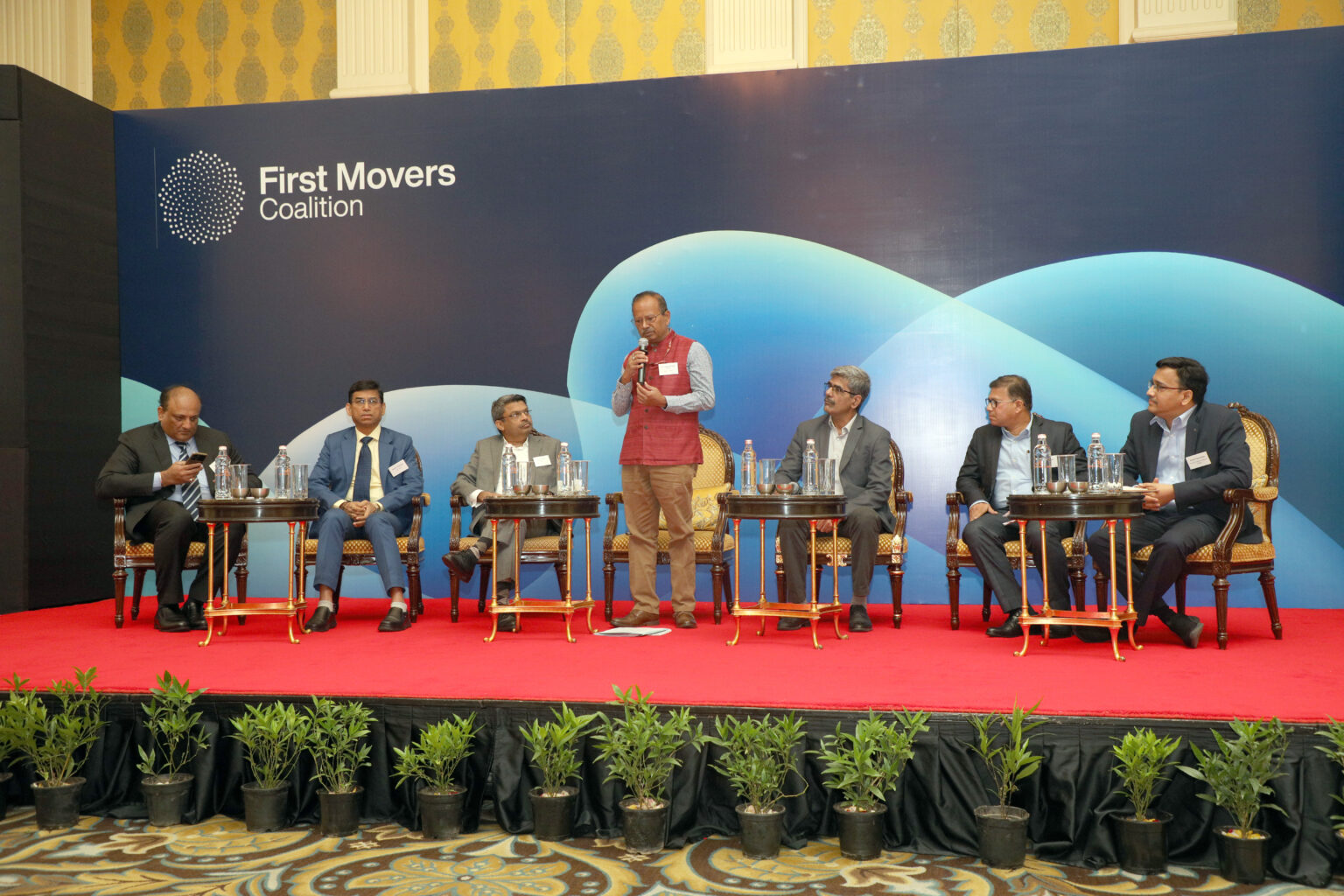
Shivakumar Kuppuswamy, ResponsibleSteel’s Director of Development and Innovation, also hosted a distinguished panel of guests who provided first hand observations of what it will take to accelerate steel decarbonisation in India. The panellists included Secretary Shri Nagendra Nath Sinha from the Indian Ministry of Steel, alongside Lenin D’Souza, Deputy General Manager of Mahindra, Sohanjeet Randhawa, Director for Sustainability Affairs & Group Communications for Volvo Group, Rajesh Goyal, Sr. Vice President of ReNew Power, Manish Chourasia, Managing Director of Tata Cleantech Capital Limited, and Mr Anand Parasramka, CFO at Saarloha Advanced Materials Limited – Kalyani Ferresta.
At the top of the FMC workshop’s agenda was the need for a strategy to capture CCUS potential as well as hydrogen growth, and the development of a carbon reduction incentive programme. On top of this, government-backed green bonds, low-interest debt, and risk-sharing processes were all suggested as interventions the government could support in order to drive the necessary investments in steel decarbonisation.
Next up, ResponsibleSteel will be hosting an event as part of the Clean Energy Ministerial in Goa this week. On July 22nd, we will be bringing together key stakeholders from the steel industry, downstream, and government, to discuss the role of the ResponsibleSteel International Standard in impacting policy, finance and the energy transition in order to accelerate steel decarbonisation in India.
Find out more about this and other upcoming events here.
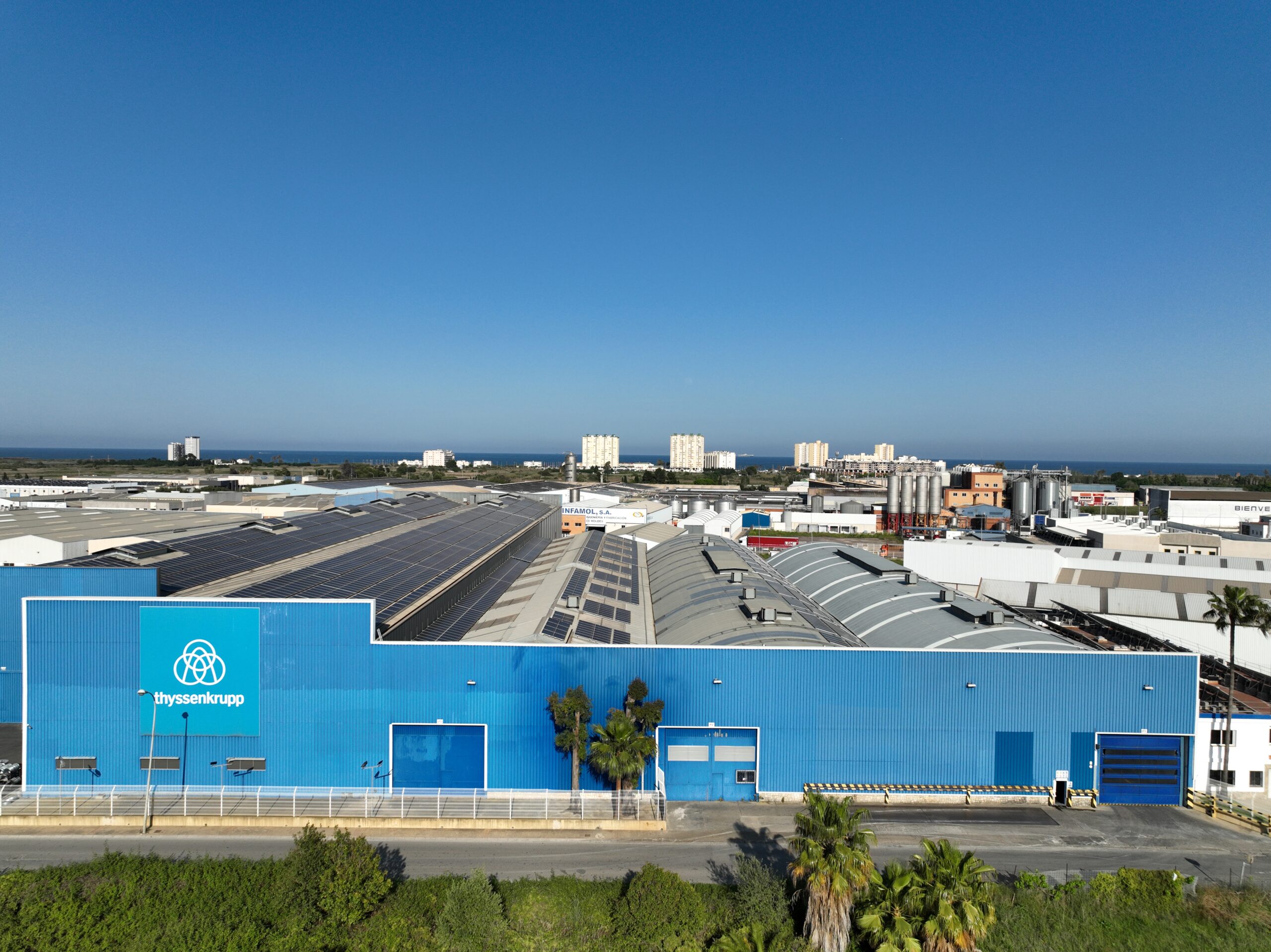
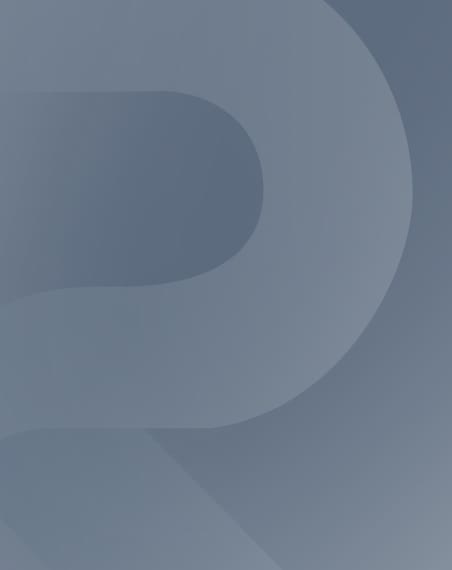
June 2023 Newsletter
Please view the June 2023 newsletter by clicking the link below: